and mixing
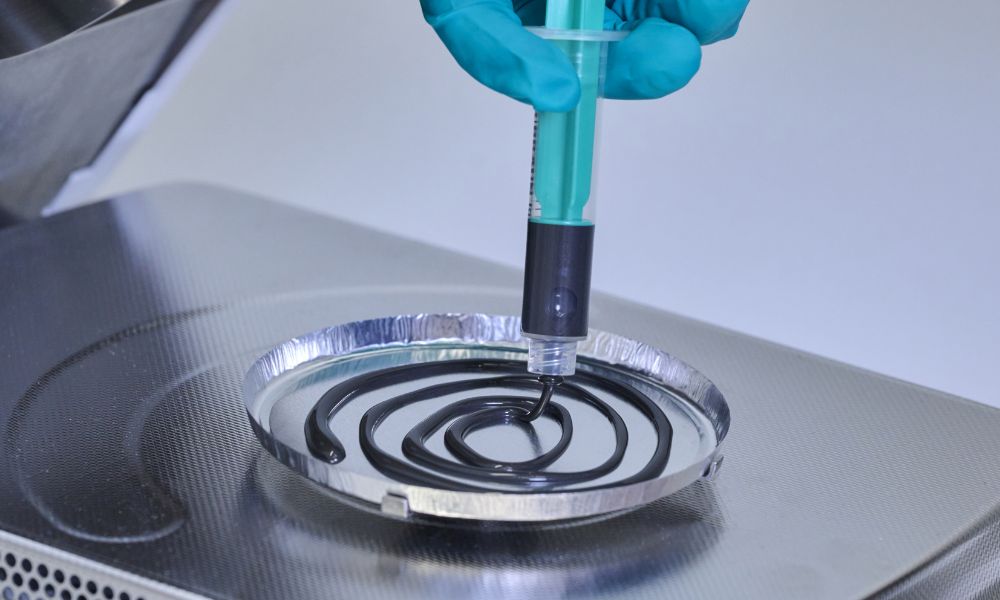
Cell production begins by making the electrodes. First, the different active materials are combined with binders and solvents in set quantities, creating the slurry.
and drying
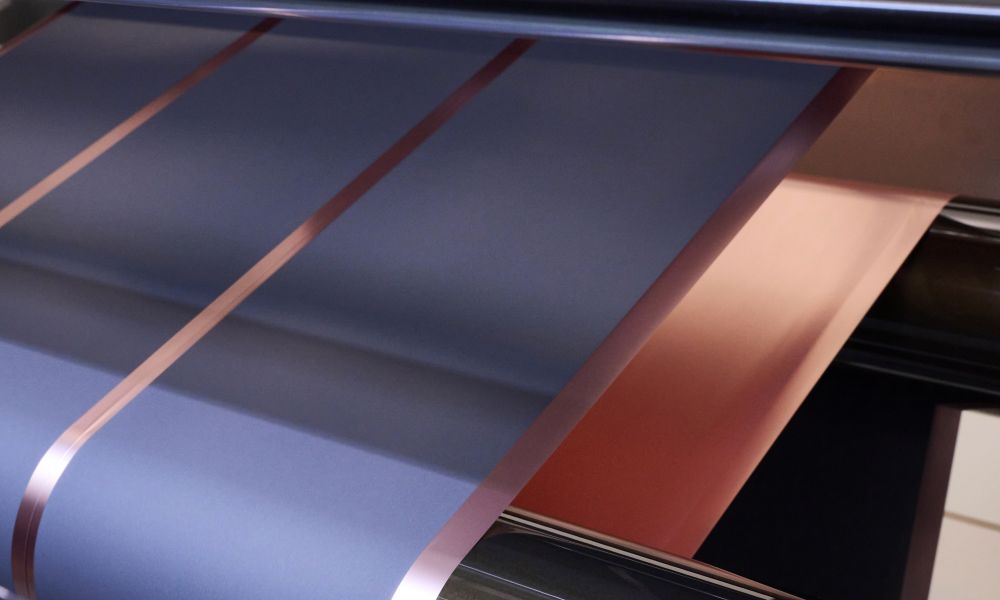
The slurry is applied to very thin metal foils and the coating then dries over 25 metres.
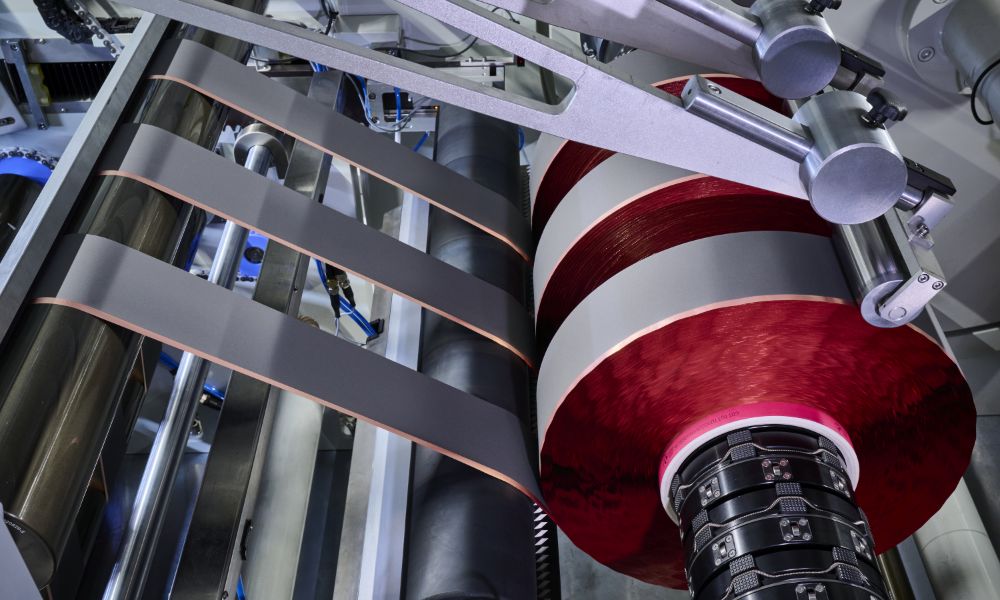
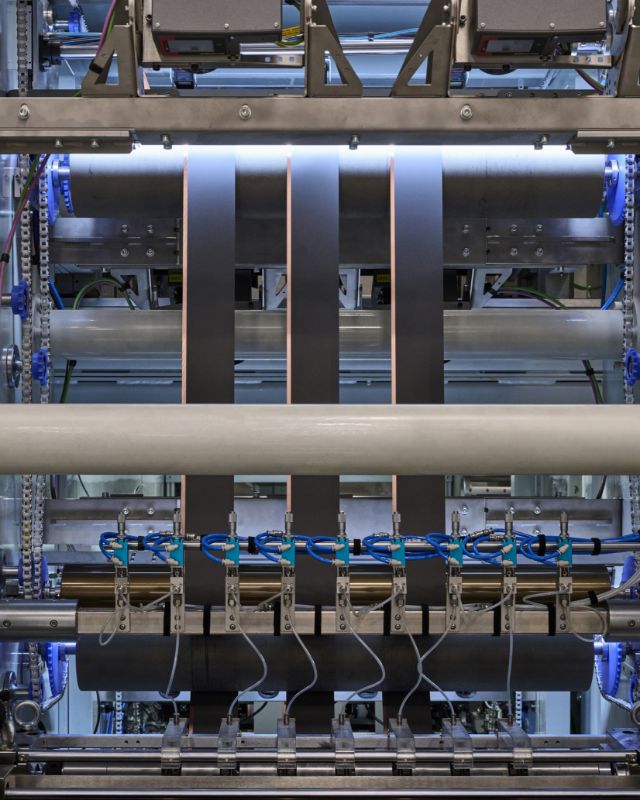
Several pairs of rollers compact the coated foils in a process known as calendering. This a highly precise process, as the foil is only a few micrometres thick – thinner than the threads of a spider’s web. The coating is also only micrometres thick.
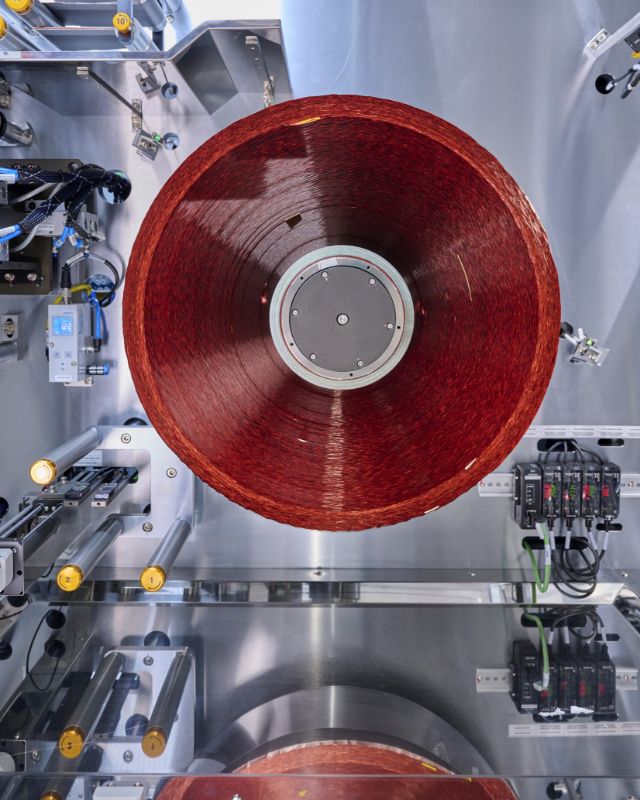
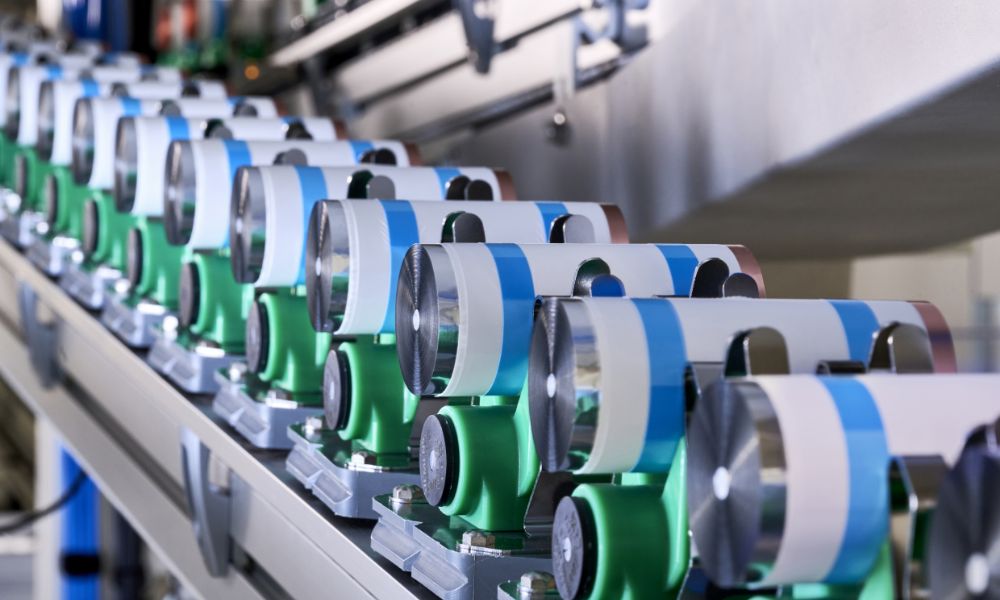
In the cell assembly stage, the coated foils – known as calendered electrodes – are wrapped around jelly rolls with a separator and inserted into the cell housing. The cells are then filled with electrolyte.
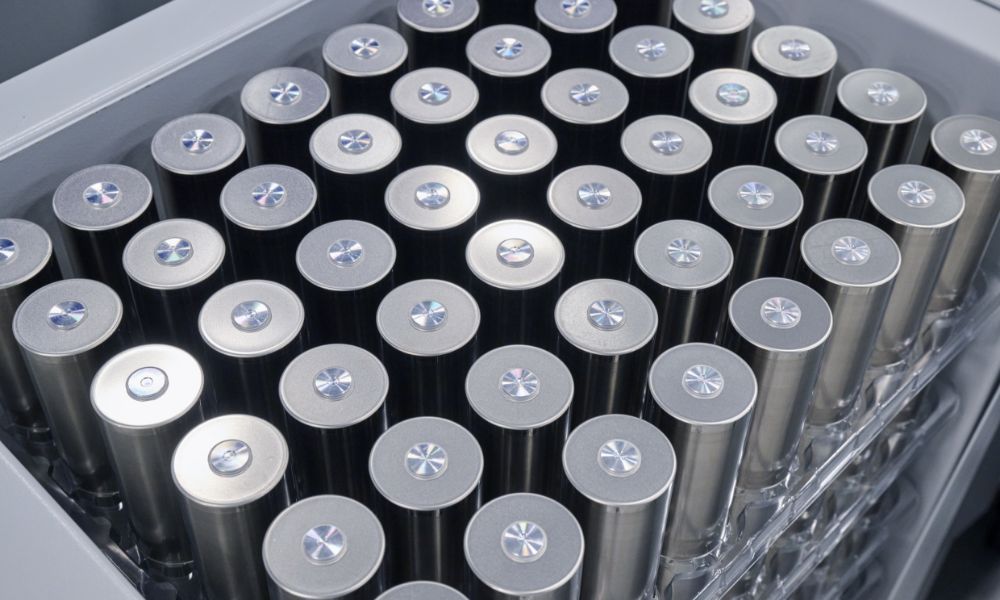
The round cells are charged for the first time and then checked.