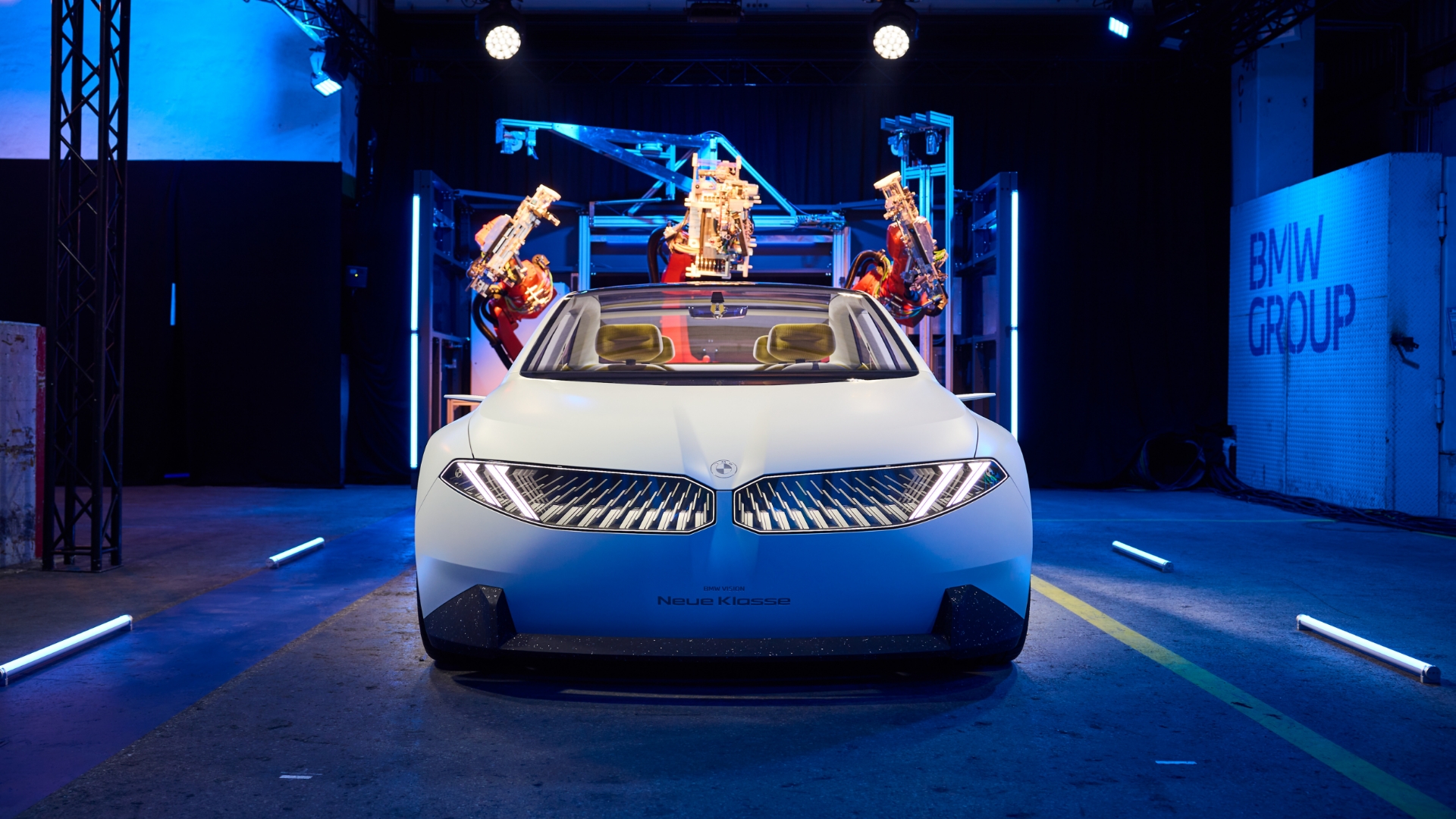
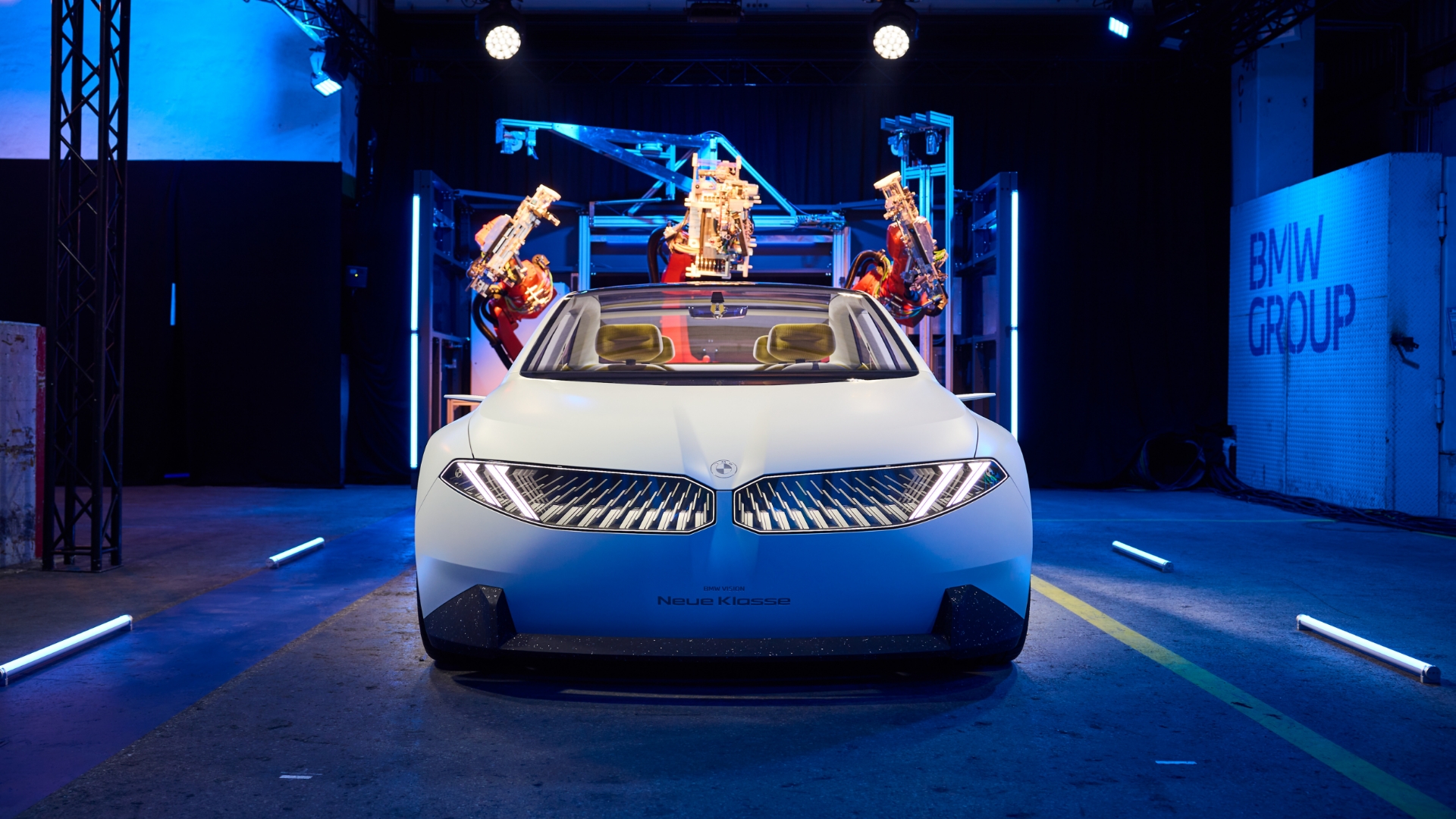
World of Production
The four dimensions of the BMW iFACTORY are efficiency, sustainability, digitalisation and people. It is the BMW Group’s strategic master plan for production and is already setting new standards and providing important impulses for the future. The concept is being implemented at all BMW Group sites.
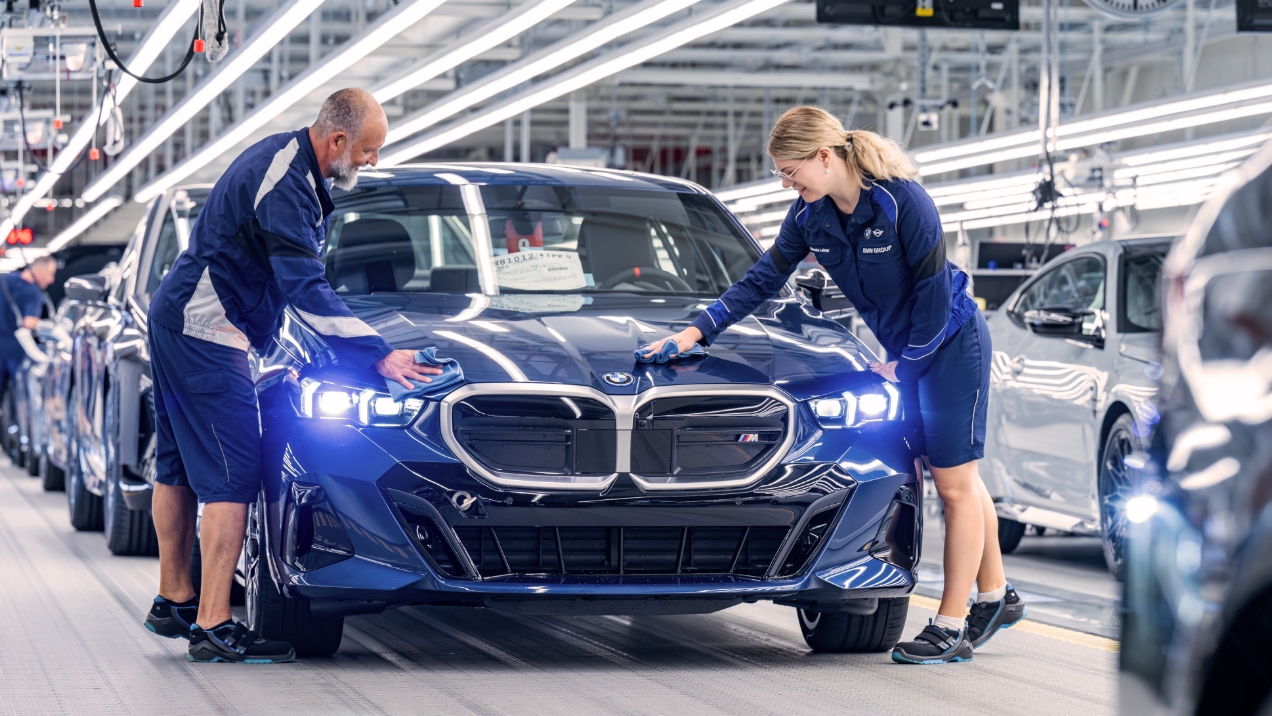
The BMW Group takes a market-oriented approach and offers a comprehensive range of products to meet a wide variety of customer needs. In this context, the highly flexible design of the production network has proved to be a major advantage. Flexible plants manufacture all vehicles on a single production line regardless of drivetrain technology. This means that the BMW Group can deliver in all market situations and can also adapt quickly to changing conditions. Resilience like this pays off – especially in times of geopolitical volatility.
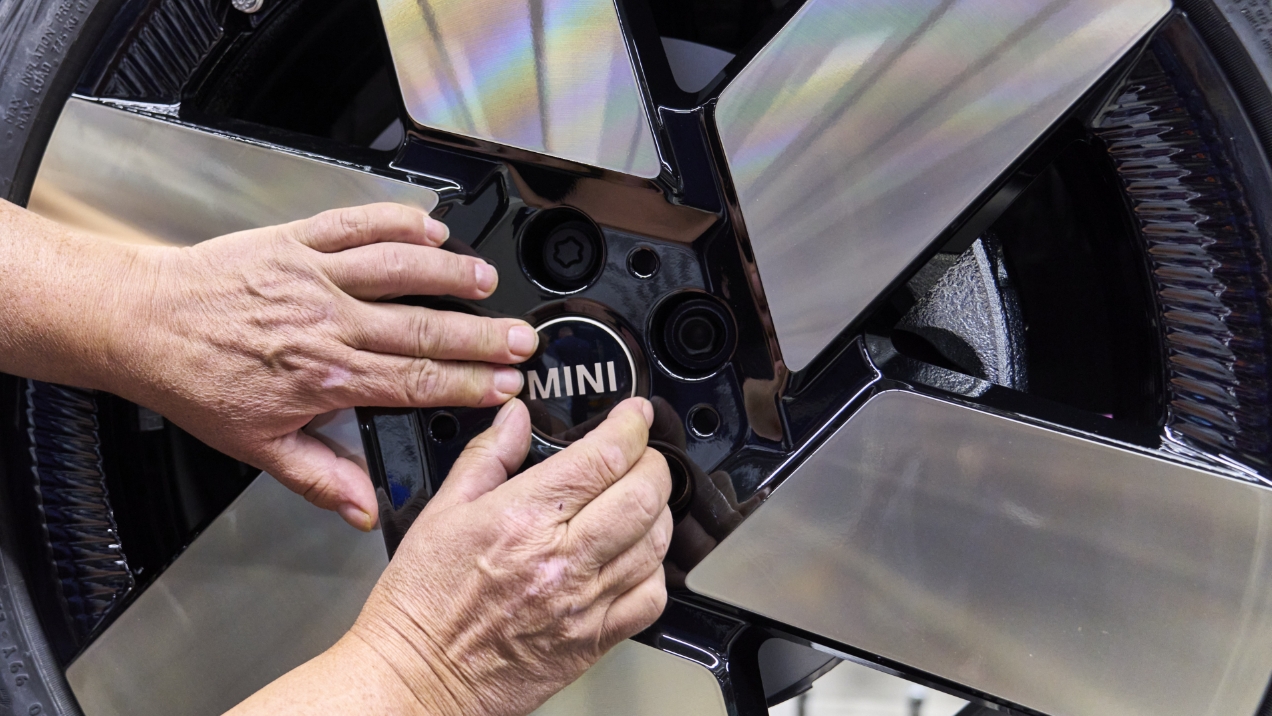
We are going to look at four locations: Munich, Spartanburg, Shenyang and Dingolfing, all of which exemplify why the BMW Group’s production strategy makes the difference when it comes to competition.
Munich
The Munich plant is not only the Company’s home plant, but also a testament to its adaptability. It has been continuously evolving for over 100 years – and is currently transitioning to all-electric production.
The first all-electric model, the BMW i4, rolled off the production line here in 2021. Vehicles with an electrified drivetrain now account for almost half of the plant’s output. The NEUE KLASSE will enter production from 2026, initially alongside the current models. Starting in 2027, Munich will be the first German location in the production network to produce only electric vehicles.
The BMW Group is investing around € 650 million in this rebuild. It includes, among other things, a new vehicle assembly line and a new bodyshop that will make the plant fit for the future. The rebuild has two distinguishing features: first, it is being completed while the plant is still in operation – around 1,000 vehicles leave the site every day. Second, its planning was completely virtual. This enabled production planners and plant engineers to work together to simulate operations in the new facilities using a 3D model, and thus identify and overcome challenges at an early stage. This made planning faster and more efficient.
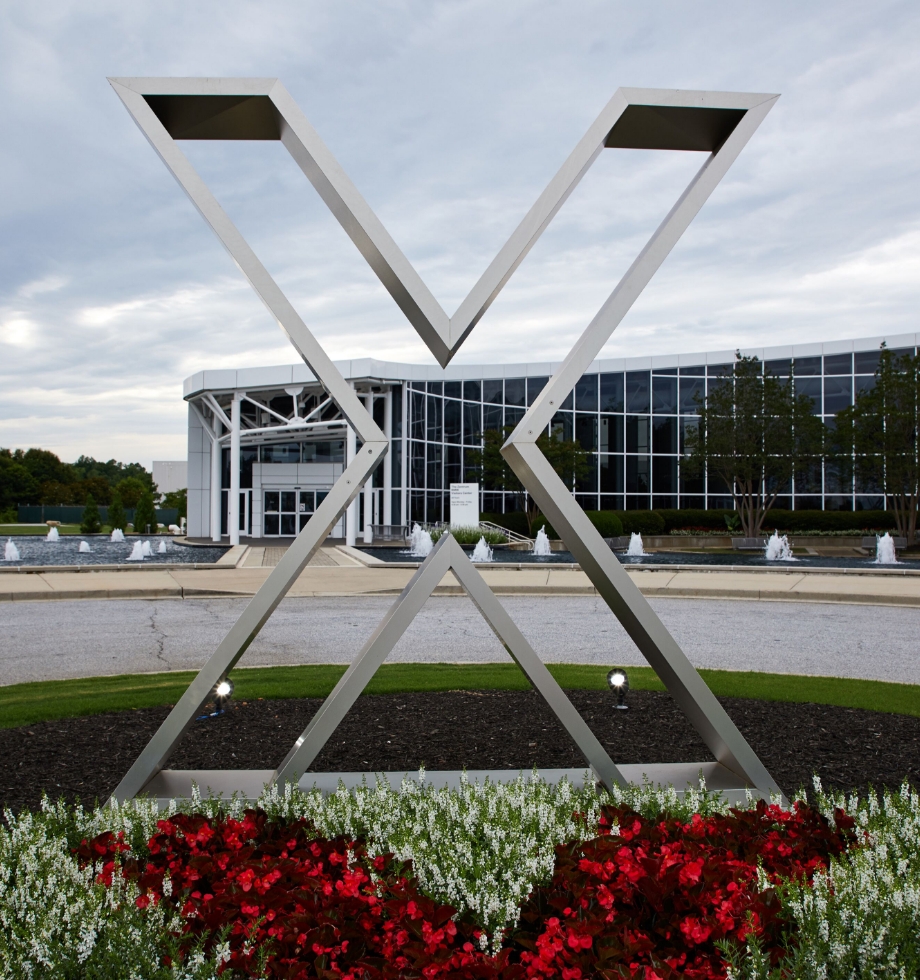
Spartanburg
Global distribution of value creation & technology openness
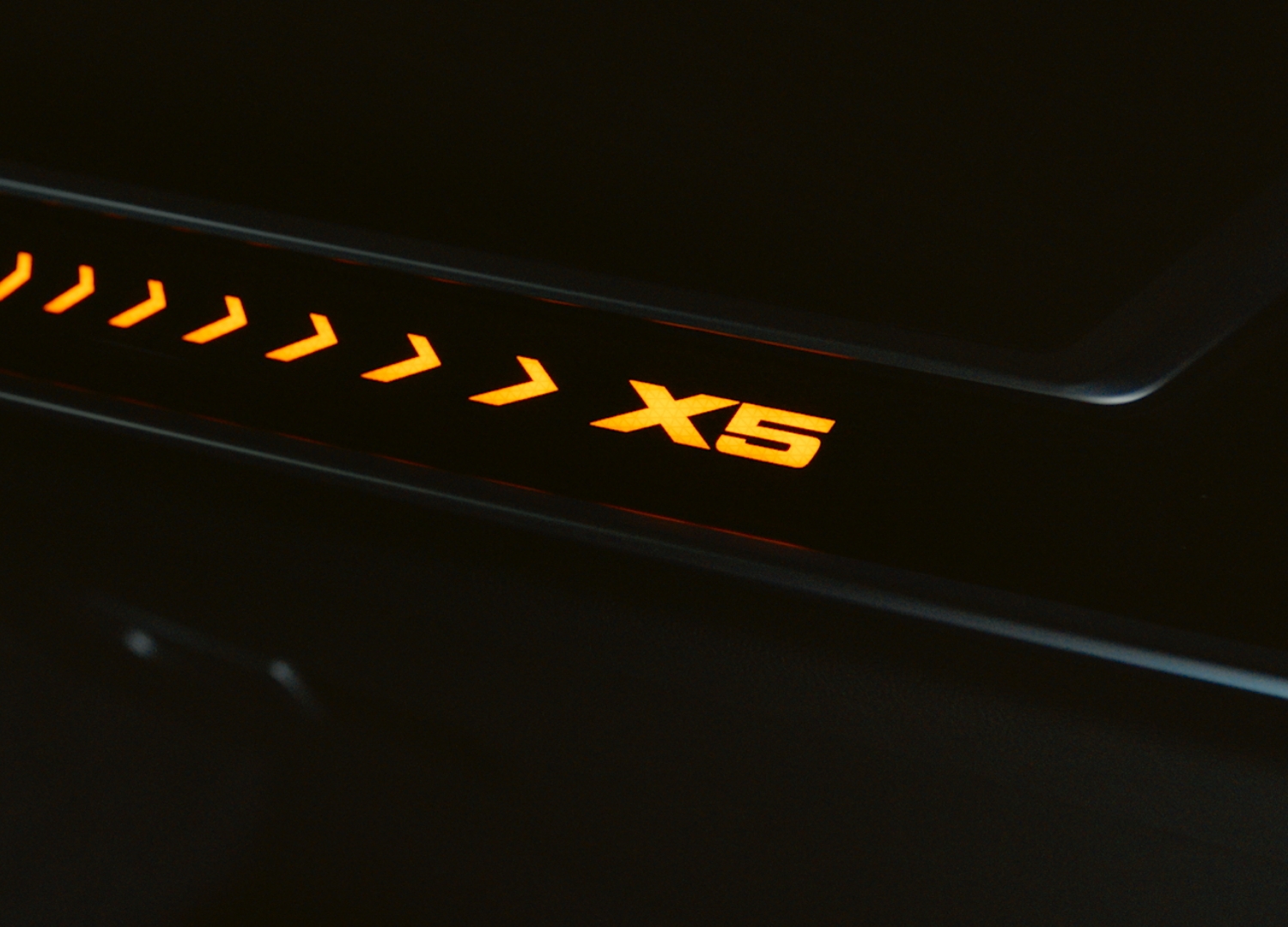
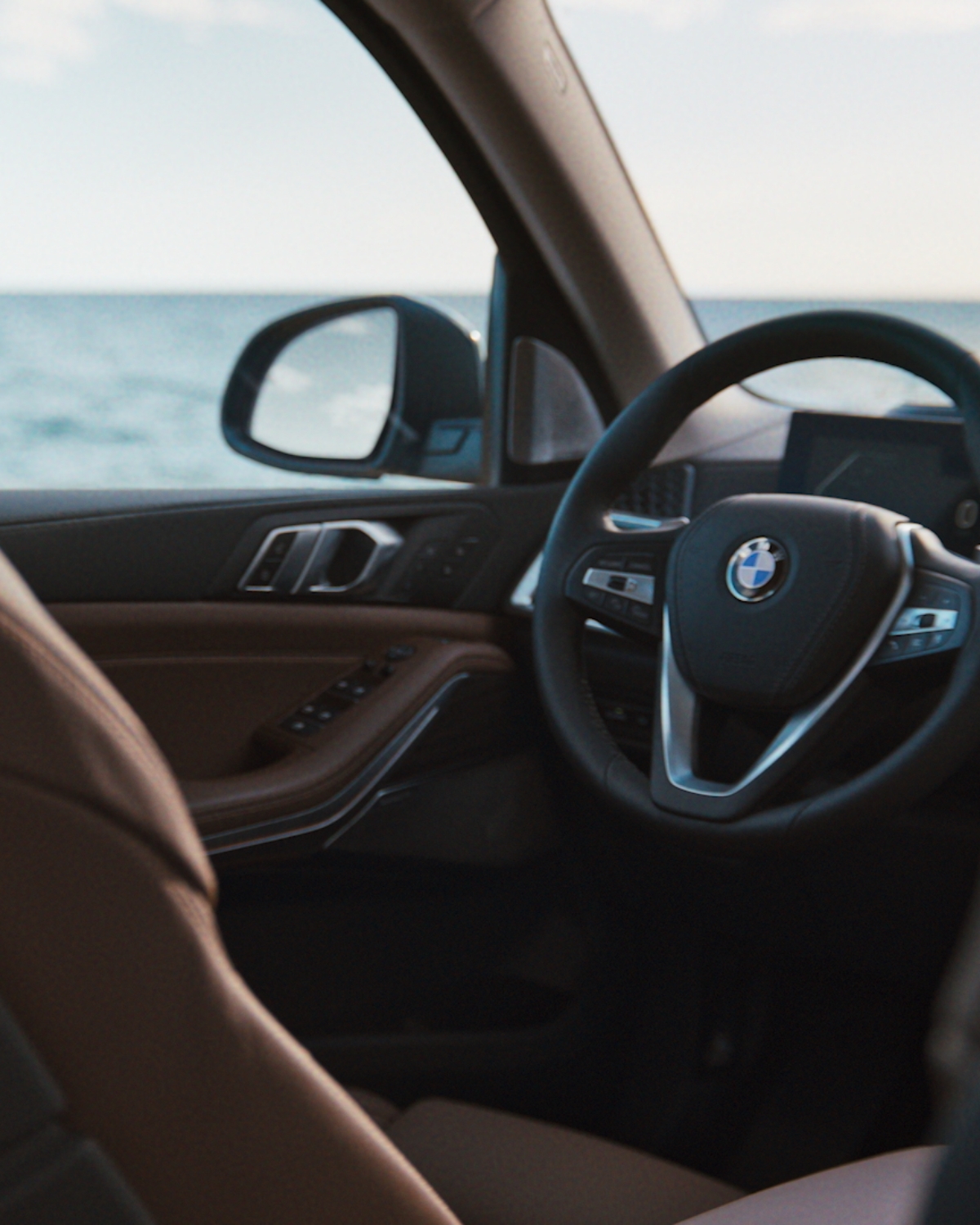
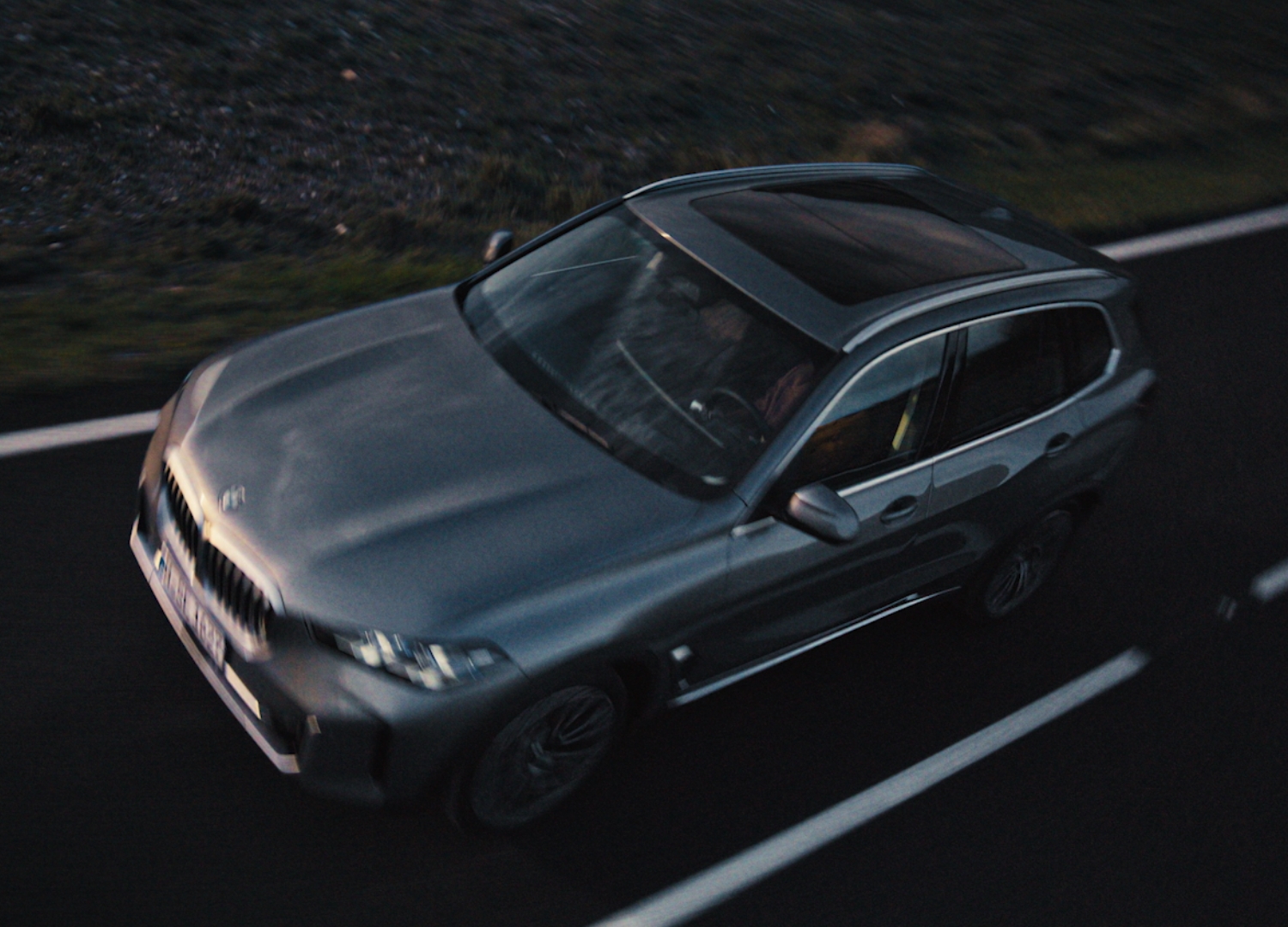
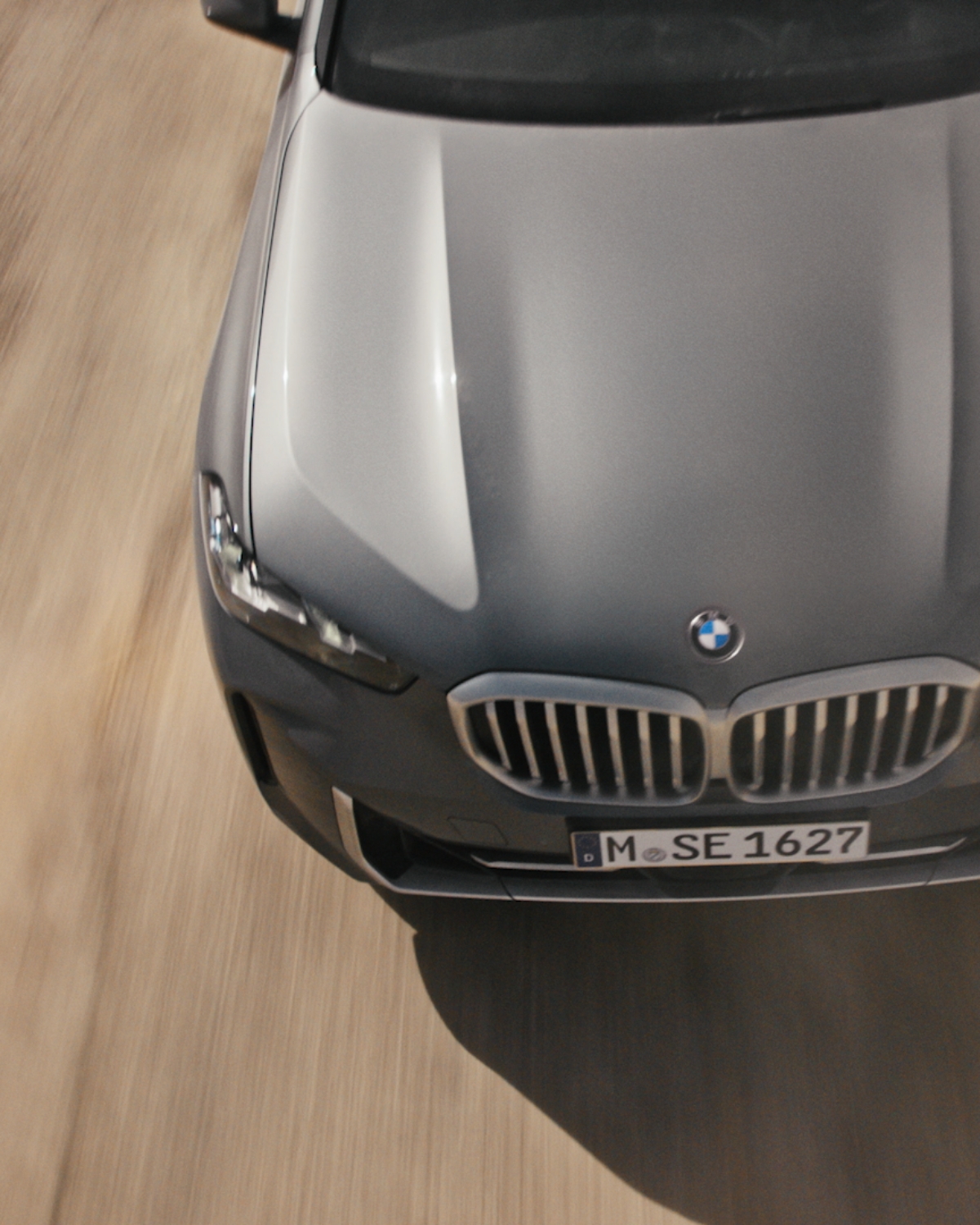
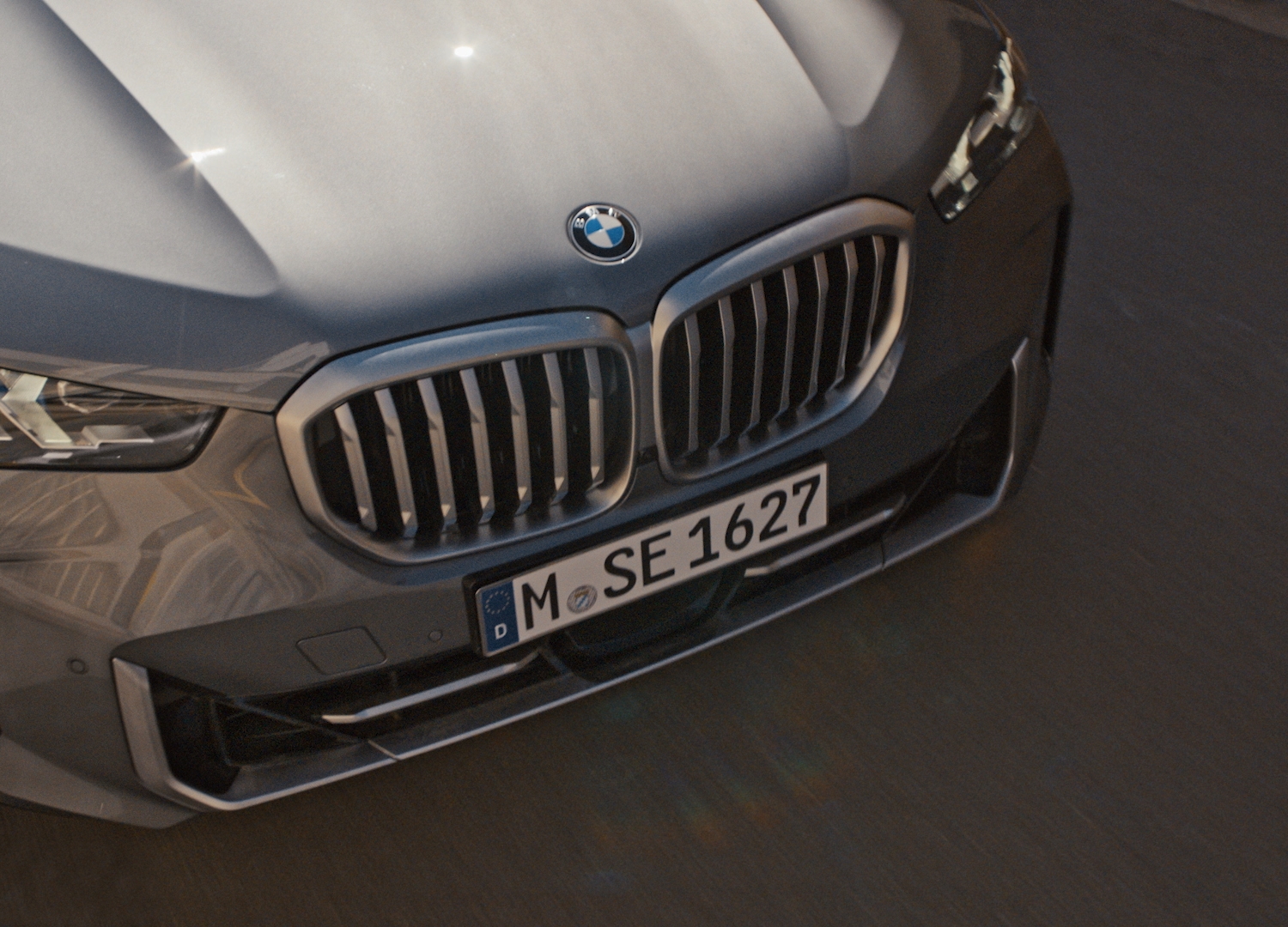
Global distribution of value creation & technology openness
The Spartanburg plant – known as “Home of the X” – is a prime example of the Company’s strategic distribution of value creation. Given that North America is the principal market for BMW X models, with sales accounting for around half of the production volume, these vehicles are also produced locally. Production based on market demand reduces currency risks and strengthens the resilience of the production network. Europe, the US and China each produce more or less the same number of BMW Group vehicles as are sold there. Furthermore, Spartanburg was once again the largest exporter of vehicles from the US in 2024 in terms of value – with its exports totalling more than 10 billion US dollars.

The BMW Group is currently investing 1.7 billion US dollars in the South Carolina site – the largest single expansion in the history of the plant. In this context, the plant is gearing up for electromobility. This means that, by the end of 2026, the same production line will be able to produce all-electric, combustion and plug-in hybrid vehicles. A high-voltage battery assembly plant is being built in nearby Woodruff to supply Gen6 vehicle batteries. In keeping with its “local for local” approach, the BMW Group is setting up battery production in or in close proximity to its production plants.
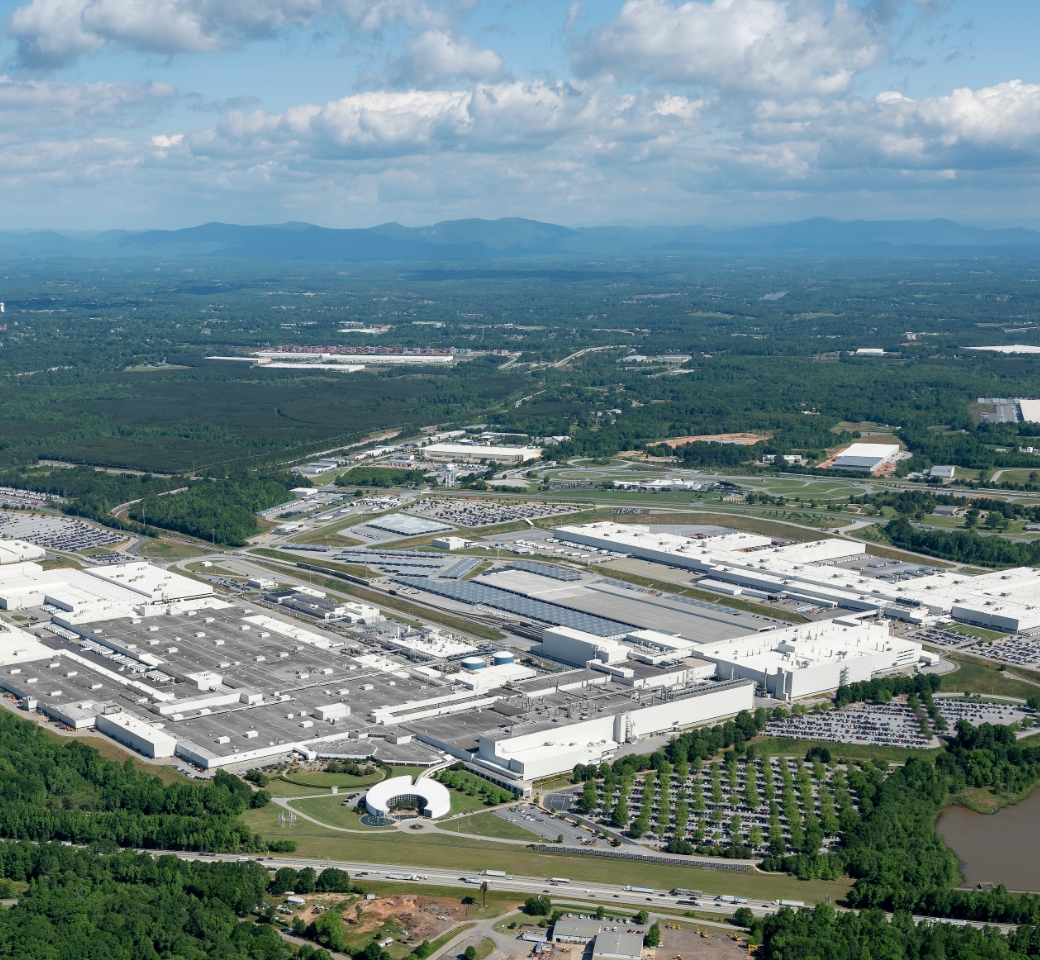
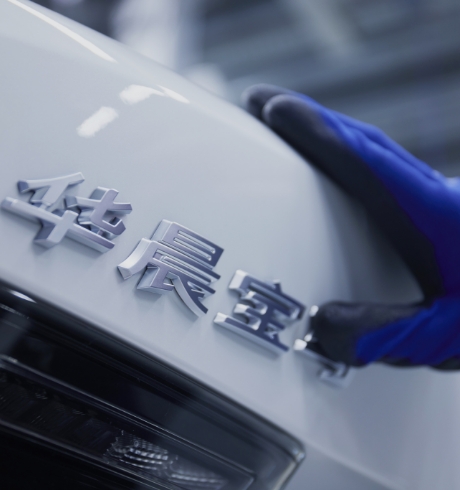
Shenyang
Digital technologies & resource-efficient production
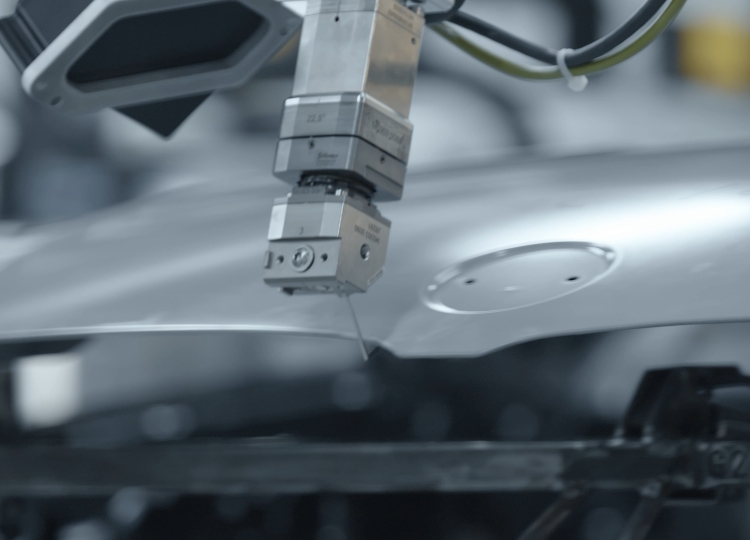
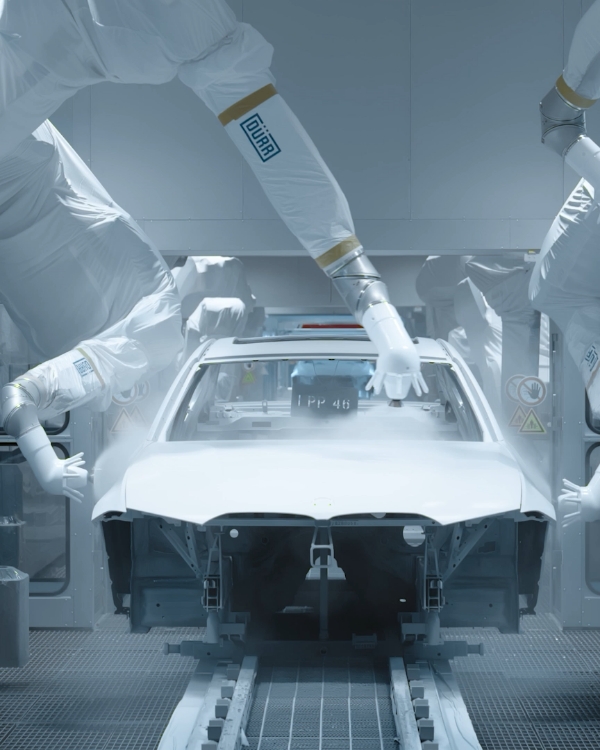
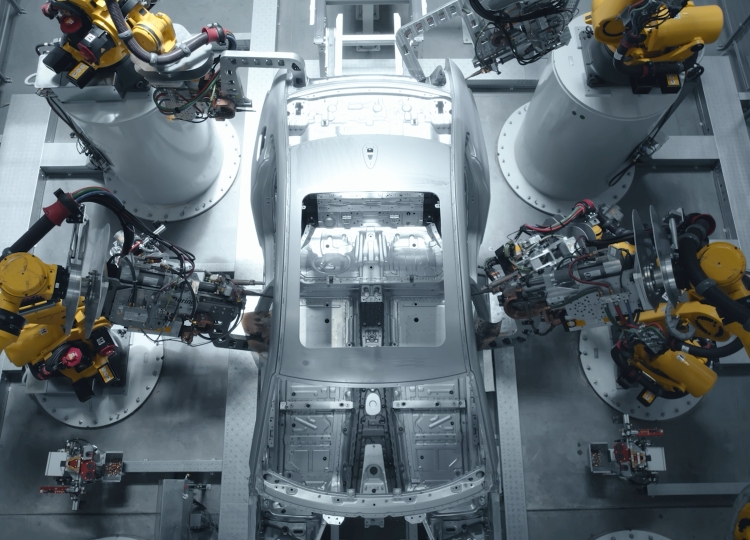
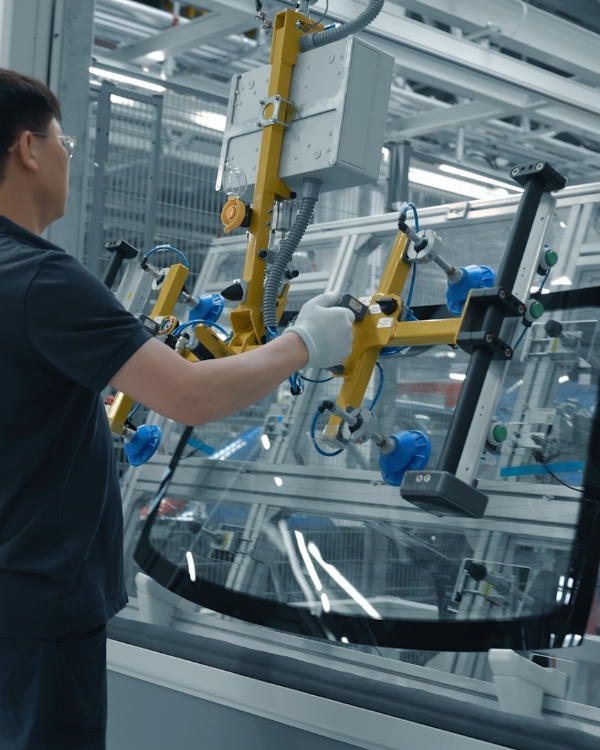
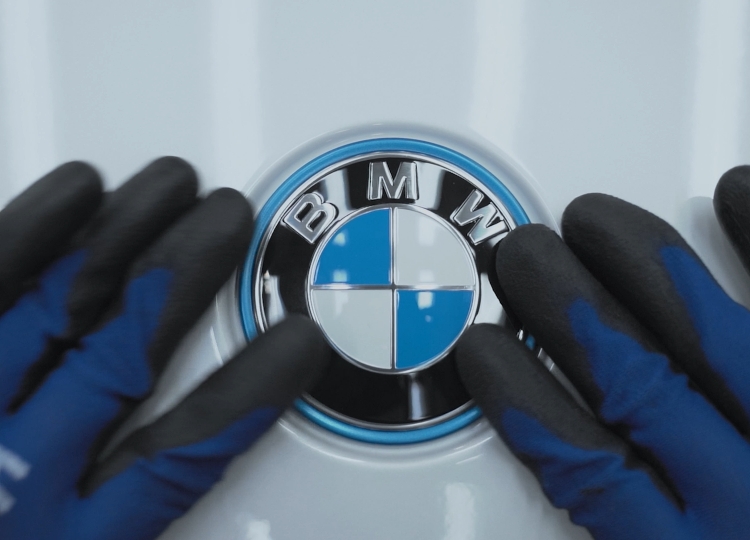
Digital technologies & resource-efficient production
BMW Brilliance Automotive Ltd. (BBA) is stepping up the use of digital technologies at its production plants in Shenyang. They employ comprehensive data monitoring: an intelligent, AI-supported system that monitors the entire production process and the consumption of water, electricity and gas in real time, thus facilitating their optimal use.
Using renewable energies also helps to reduce carbon emissions. A large-scale geothermal energy project will ensure the heating supply for the on-site Powertrain Plant and the Gen6 high-voltage battery production facility. As part of the project, 28 geothermal wells have been installed over an area measuring 580,000 square metres.
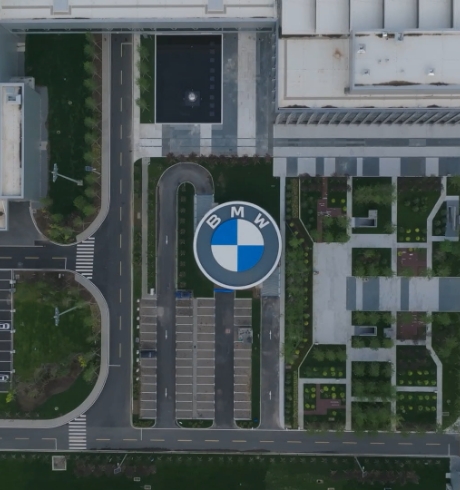
Shenyang is relying on BEACON – a self-developed technology platform – in order to optimise opportunities in the areas of quality control, identifying irregularities, intelligent site management, logistics planning and energy management. BEACON continuously integrates state-of-the-art AI applications like LLMs, Multimodal Models and AI agents to drive forward the use of generative AI and digitalisation at the BMW Group in China.
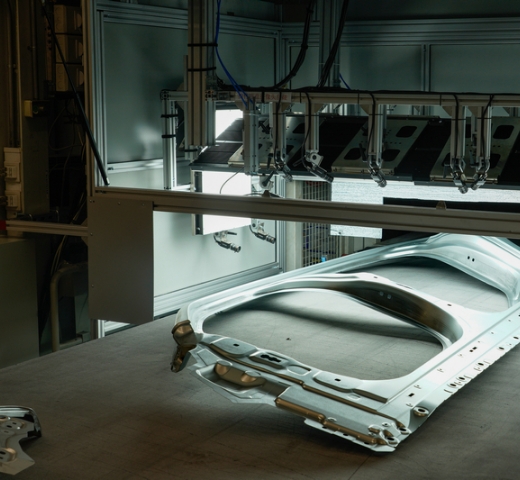
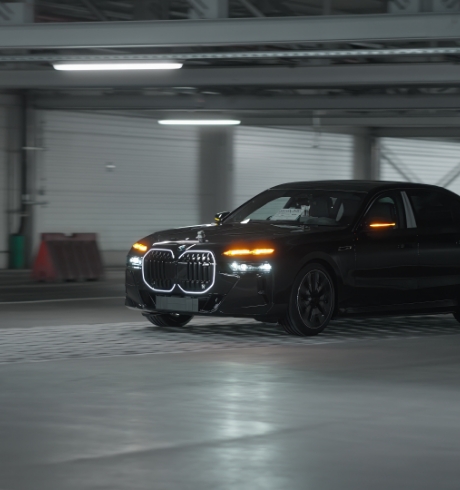
Dingolfing
Automated Driving In-Plant & quality control
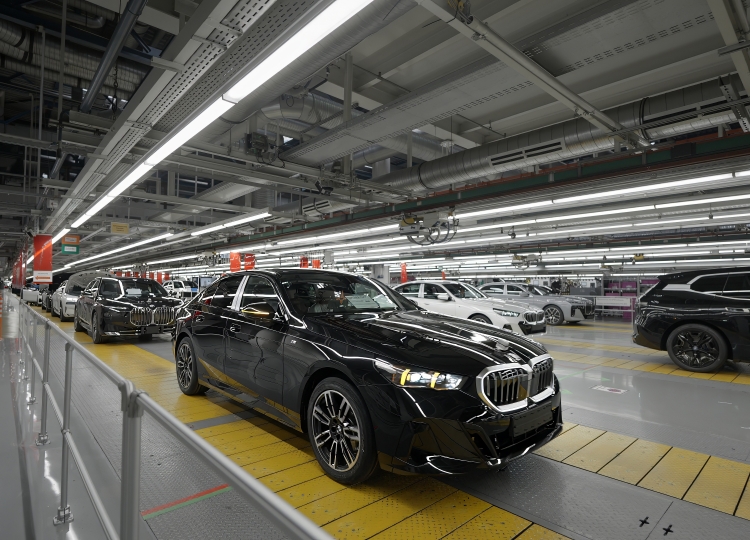
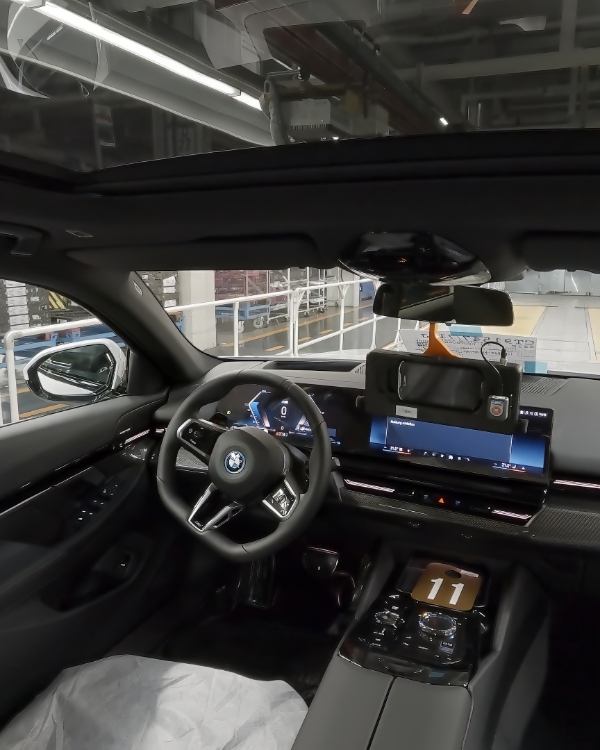
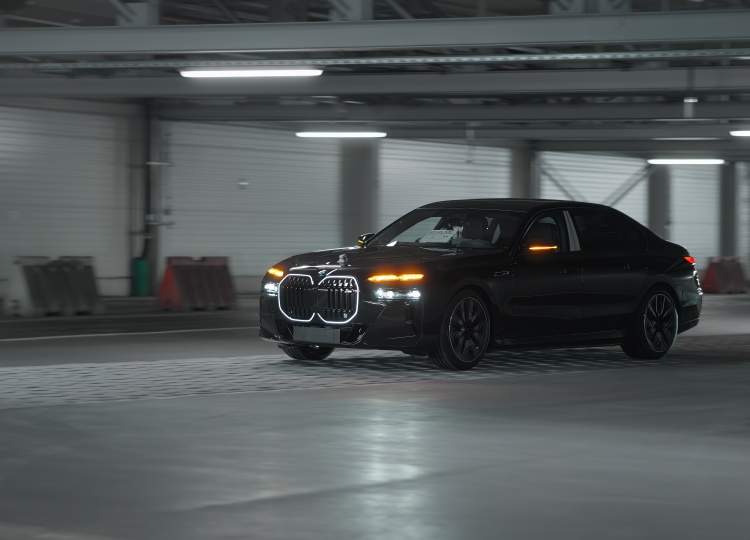
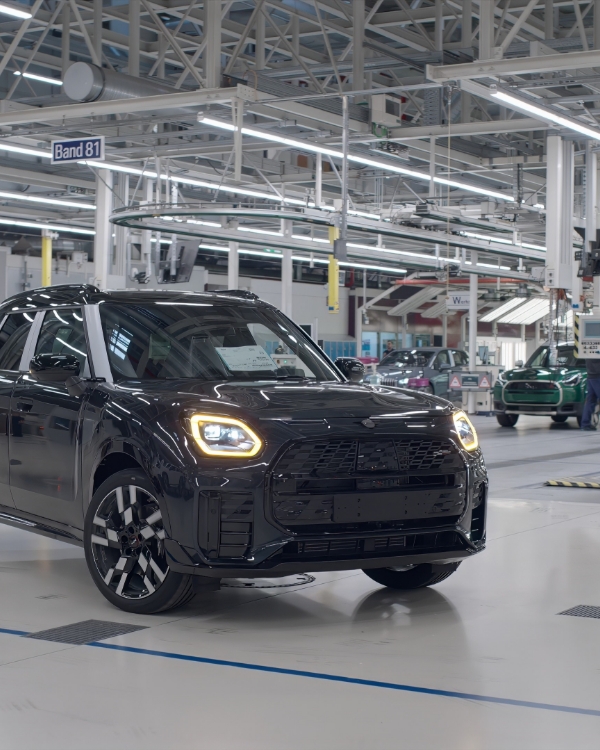
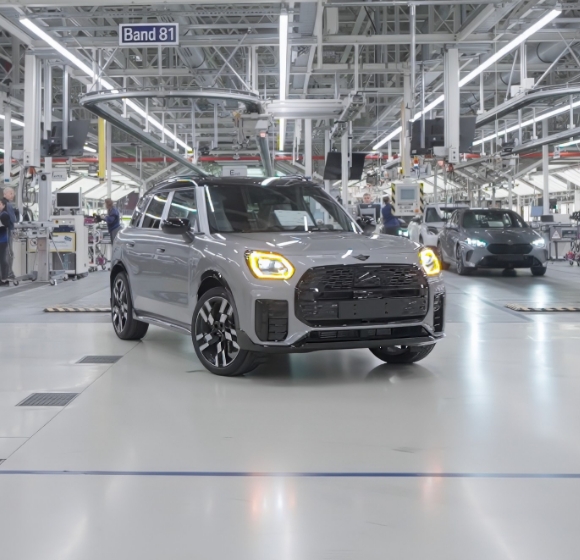
Automated Driving In-Plant & quality control
At Dingolfing, BMW 5 and 7 Series models travel autonomously for over a kilometre through the plant – from the assembly line to the short test course to the finishing area. “Automated Driving In-Plant” (AFW) is possible thanks to Europe’s largest infrastructure for LiDAR, a remote sensing technology. The vehicles use laser lights and sensors along the route to help them navigate and detect obstacles. Following successful certification, the pilot project was scaled up to include Plant Leipzig in 2024; other plants are set to follow. The BMW Group plans to extend the use of Automated Driving In-Plant to other areas in the future, including driving through testing zones and use in outdoor distribution areas.
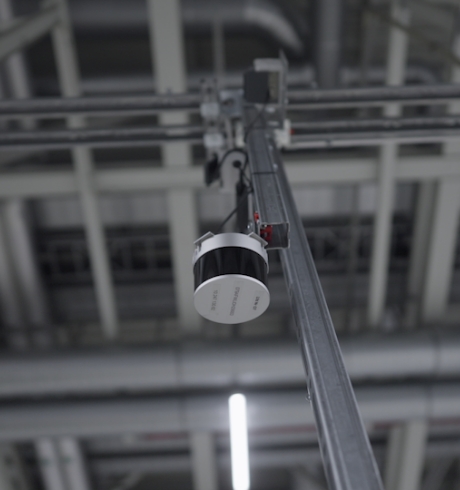
In addition, cloud-based and AI-supported methods are optimising processes right from the production line. Car2X, for instance, connects vehicles with the system in real time. The vehicles communicate autonomously with plant personnel and document any irregularities, thus actively participating in their own production process. This adds an extra level of production quality assurance. What is more, the AIQX (Artificial Intelligence Quality Next) IT platform automates quality control using sensors and AI.
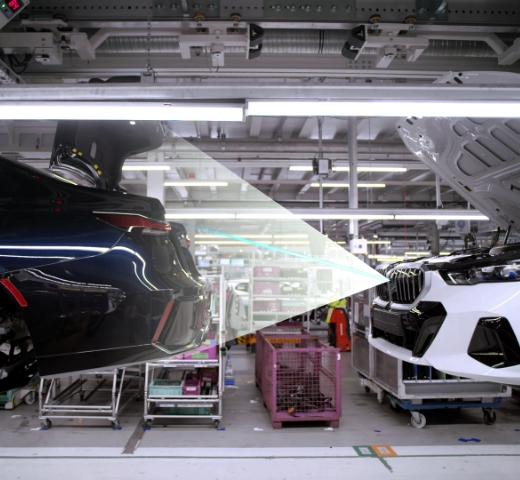
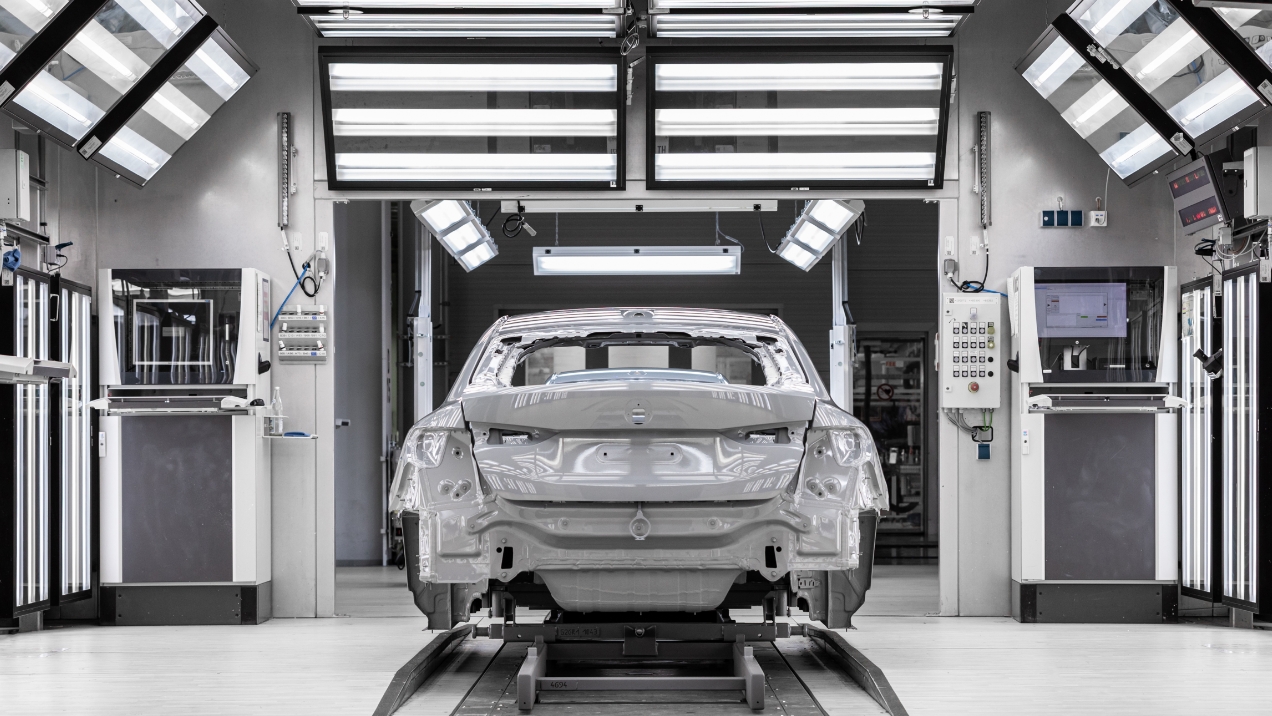
Virtual production planning, flexible and market-oriented production, AI-supported applications, resource-efficient processes and smart, interconnected production: the BMW Group is setting new standards and providing important impetus for the future of production thanks to its pioneering technologies and processes.