Angehenden Ingenieuren Einblicke in moderne und nachhaltige Produktion zu geben und sie zu eigenen Projekten inspirieren – das ist das Ziel des BMW Group Smart Melbourne Scholarship. Das Förderprogramm führte nun einige Tüftler von Australien bis nach Deutschland ins BMW Group Werk Leipzig.
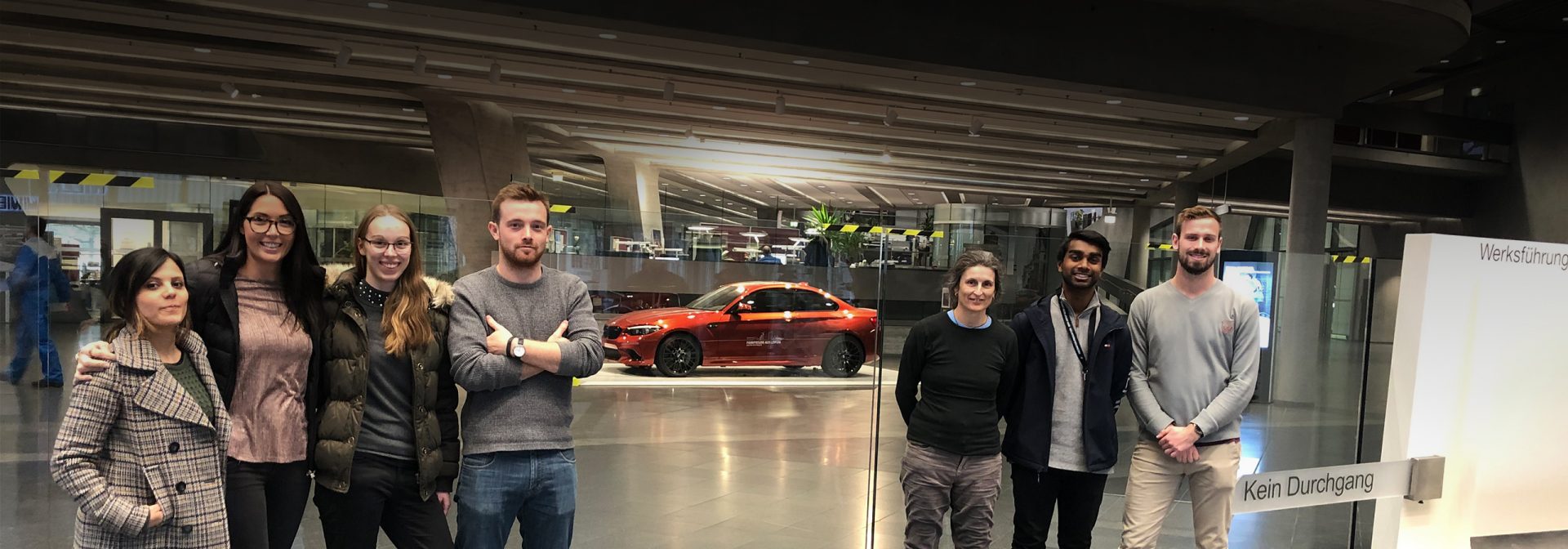
„I go to sleep dreaming of how to change the world and wake hungry to try“ – Sätze wie diese sagt Matthew Wildoer. Sein Wille zur Veränderung bezieht sich vor allem auf eines: Techniken zu entwickeln, die unsere Nutzung von Umweltressourcen nachhaltiger machen. Neben seinem Studium im australischen Melbourne will der 23-jährige Student der Ingenieurwissenschaften nun sehen, welche Techniken weltweit genutzt werden, um Produkte heute schon so umweltverträglich wie möglich zu produzieren.
Gemeinsam mit vier Kommilitoninnen und Kommilitonen hat er sich deshalb für das BMW Group Smart Melbourne Scholarship beworben. Das Pilotprogramm richtete sich an Studierende der Swinburne University of Technology, die mit eigenen Projektideen besondere Kreativität im Bereich nachhaltige urbane Mobilität bewiesen haben. Seinen Teilnehmern ermöglicht es, in einer Studienreise nach Deutschland Einblicke in die Produktionsstätten und Kooperationsprojekte der BMW Group zu gewinnen.
Einer der Höhepunkte dabei: Der Besuch im BMW Group Werk Leipzig. Über 5.300 Mitarbeiterinnen und Mitarbeiter produzieren hier Tag für Tag mehr als 1.000 Fahrzeuge, unter anderem die besonders nachhaltigen BMW i3 und i8 mit Elektro- beziehungsweise Hybridantrieb. Doch nicht nur die hier hergestellten Fahrzeuge, auch der Produktionsprozess selbst ist an Ressourcenschonung ausgerichtet. Ein schon von weitem sichtbares Zeichen dafür: die vier großen Windkraftanlagen auf dem Werksgelände. Für sein wirksames Nachhaltigkeitskonzept ist das BMW Group Werk Leipzig unter anderem mit dem renommierten „Lean & Green Management Award“ ausgezeichnet.
Hier im Werk Leipzig lernen die fünf Studierenden die wichtigsten Produktionsbereiche vom Presswerk über den Karosseriebau bis zur Montage genauer kennen. Die zukünftigen Ingenieure diskutieren kritische Fragen: „Was ist konkret geplant, um den Ressourcenverbrauch weiter zu reduzieren?“ oder „Findet die BMW Group die richtige Balance zwischen nachhaltiger Herstellung und effizienter Produktion?“ Und: „Welche positiven Auswirkungen hat es auf die Umwelt, wenn die BMW Group beim Karosseriebau statt Schweißverbindungen spezielle Klebeverbindungen nutzt?“
Bedeutend für die Nachhaltigkeit eines Werkes ist jedoch nicht nur die Produktion, sondern natürlich auch die Energiebilanz des Produktes an sich. Was hier zählt: vor allem das Gewicht eines Fahrzeugs. Das gesamte ‚Life-Modul‘, also die Fahrgastzelle eines i3, besteht aus CFK, einem kohlenstofffaserverstärkten Kunststoff. Das Material ist um 50 Prozent leichter als hochfester Stahl und um 30 Prozent leichter als Aluminium. CFK gilt als einer der bedeutendsten Baustoffe für die Fahrzeuge von morgen. Den BMW i3 beispielsweise hat die Verwendung dieses innovativen Baumaterials im Vergleich zu einem herkömmlichen Fahrzeug mit Elektroantrieb um bis zu 350 Kilogramm ‚erleichtert‘. Tatsächlich könnten die fünf Studierenden das Life-Modul mit seinen lediglich 137 Kilogramm mühelos anheben.
„Viel besser wäre es, wenn jeder diese Innovationen auf den ersten Blick sehen könnte“, sagt Rusul Abduljabbar. Die Doktorandin mit irakischen Wurzeln kam für ihr Studium nach Australien und nimmt wie Matthew Wildoer am BMW Group Smart Melbourne Scholarship teil. Das gelte, findet sie, für alle nachhaltigen Werkstoffe: die Naturfaser Kenaf, die für die Innenverkleidung genutzt wird, für das Holz der Interieurleiste, das aus nachhaltigem Anbau stammt, und eben auch für die Karbonfasern der Fahrgastzelle. Ihr Vorschlag daher: „Wie wäre es, den BMW i3 zu Anschauungszwecken ‚nackt‘ zu verkaufen und auf die Lackierung einfach zu verzichten?“
Auf Nachhaltigkeit sehr schmackhafter Art stoßen die Nachwuchsingenieure dann zum Ende ihrer Tour: Bienen! Rund 20 Völker haben sich mittlerweile beim BMW Group Werk Leipzig angesiedelt. Sie nutzen den hohen ökologischen Standard am Werk und die Wiesen, die bewusst nicht gemäht werden, um die Flora für Insekten zu erhalten. Von der Natur, so die Überzeugung, können auch Ingenieure der kommenden Generation noch viel lernen. Sei es beim ‚Leichtbau‘ oder dem ökologischen Antrieb. Bis dahin aber lässt sich ihr Produkt trefflich nutzen. Für ein Honigbrot made by Bees Manual Work.