Giving aspiring engineers insights into modern and sustainable production and inspiring them to create their own projects – that is the aim of the BMW Group Smart Melbourne Scholarship. The sponsorship programme has now taken some inventors all the way from Australia to as far as Germany and the BMW Group Leipzig plant.
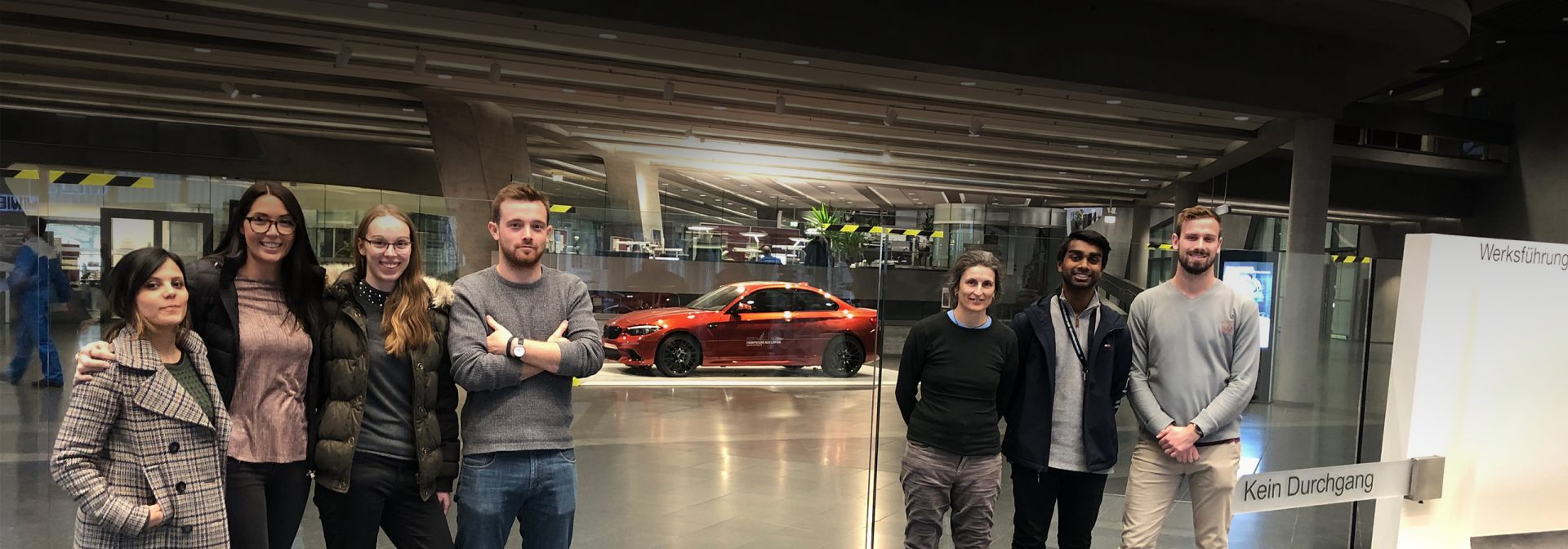
“I go to sleep dreaming of how to change the world and wake hungry to try” – statements such as this come from Matthew Wildoer. His will to bring about change relates above all to one thing – developing technologies that render our use of environmental resources more sustainable. In addition to his studies in Melbourne, Australia, the 22-year-old student of engineering sciences now wishes to see which technologies are today already being employed worldwide to manufacture products as environmentally friendly as possible.
Along with four fellow students, he therefore applied for the BMW Group Smart Melbourne Scholarship. The pilot programme addressed students of the Swinburne University of Technology, who by virtue of their own projects have demonstrated exceptional creativity in the area of sustainable urban mobility. It enables participants during a study tour to Germany to gain insights into the BMW Group’s production facilities and cooperative projects.
One of the highlights: the visit to the BMW Group Leipzig plant. Each day, over 5,300 employees produce more than 1,000 vehicles, including the particularly sustainable BMW i3 and i8 with electric or hybrid drive respectively. However, not only the vehicles produced here are oriented towards the sustainable use of resources, but also the production process itself. Indication of this visible even from a distance: the four large wind power plants located on the factory premises. The BMW Group Leipzig plant was honoured, inter alia, with the renowned “Lean & Green Management Award” for its effective sustainability concept.
Here at the Leipzig plant, the students gain deeper insight into the most important production areas, ranging from the pressing plant to the body shop and the assembly line. The future engineers discuss critical issues: “Exactly what plans exist to reduce resource consumption even further?” or “Will the BMW Group find the right balance between sustainable production and efficient production?” And “What positive impacts does it have on the environment when the BMW Group applies special adhesive bonding methods for body construction as opposed to welding?”
However, not only is production crucial for the sustainability of a plant but, of course, also the energy footprint of the product itself. The most important thing here: the vehicle weight. The entire ‘life module‘, i.e. the passenger cabin of an i3, consists of CFRP, a carbon fibre reinforced plastic. This material is 50 percent lighter than high-tensile steel and 30 percent lighter than aluminium. CFRP is considered one of the most significant materials for the vehicles of tomorrow. The use of this innovative material has, for example, ‘relieved’ the BMW i3 of up to 350 kilograms in weight versus a conventional vehicle with electric drive. As a matter of fact, the five students were able to lift the life module, which weighed only 137 kilograms, quite effortlessly.
“It would be far better if everyone could see these innovations at first glance,” says Rusul Abduljabbar. The doctoral candidate with Iraqi roots came to Australia to study and, like Matthew Wildoer, is participating in the BMW Group Smart Melbourne Scholarship. This applies, she believes, to all sustainable materials: The natural fibre kenaf, which is used for the interior trim, for the wood on the interior trim strips, which is gained from sustainable cultivation, and, of course, the carbon fibre used for the passenger cabin. Therefore, her proposal is: “How about selling the BMW i3 ‘stripped’ for viewing purposes and simply doing without the paint finish?”
At the end of their tour, the young engineers then encounter sustainability of a very tasty kind: Bees! Around 20 bee colonies have meanwhile settled at the BMW Group Leipzig plant. They make use of the high ecological standard at the plant and on the meadows, which the BMW Group deliberately does not mow in order to preserve the flora for insects. One is convinced that engineers of the next generation can still learn a great deal from nature, whether it be ‘lightweight construction’ or ecological drive systems. But until then, their product can be put to splendid use. For honey bread made by Bees Manual Work.