In Dingolfing stellt die BMW Group seit 2013 E-Antriebe her, nun startet die Produktion der fünften Generation. Das Unternehmen erhöht seine Kapazität umfassend und eröffnet ein eigenes Kompetenzzentrum für E-Antriebsproduktion. Bis zu 2.000 Beschäftigte werden hier BMW E-Antriebe fertigen – und das für bis zu 500.000 Fahrzeuge pro Jahr.
An seinem größten europäischen Fertigungsstandort in Dingolfing hat die BMW Group das Kompetenzzentrum E-Antriebsproduktion eröffnet. Damit beschleunigt das Unternehmen seinen Hochlauf der E-Mobilität und setzt mit seiner Produktion Maßstäbe bei der Transformation der Industrie. Schon seit 2013 werden in Dingolfing E-Antriebskomponenten produziert, nun baut die BMW Group ihre Kapazitäten deutlich aus.
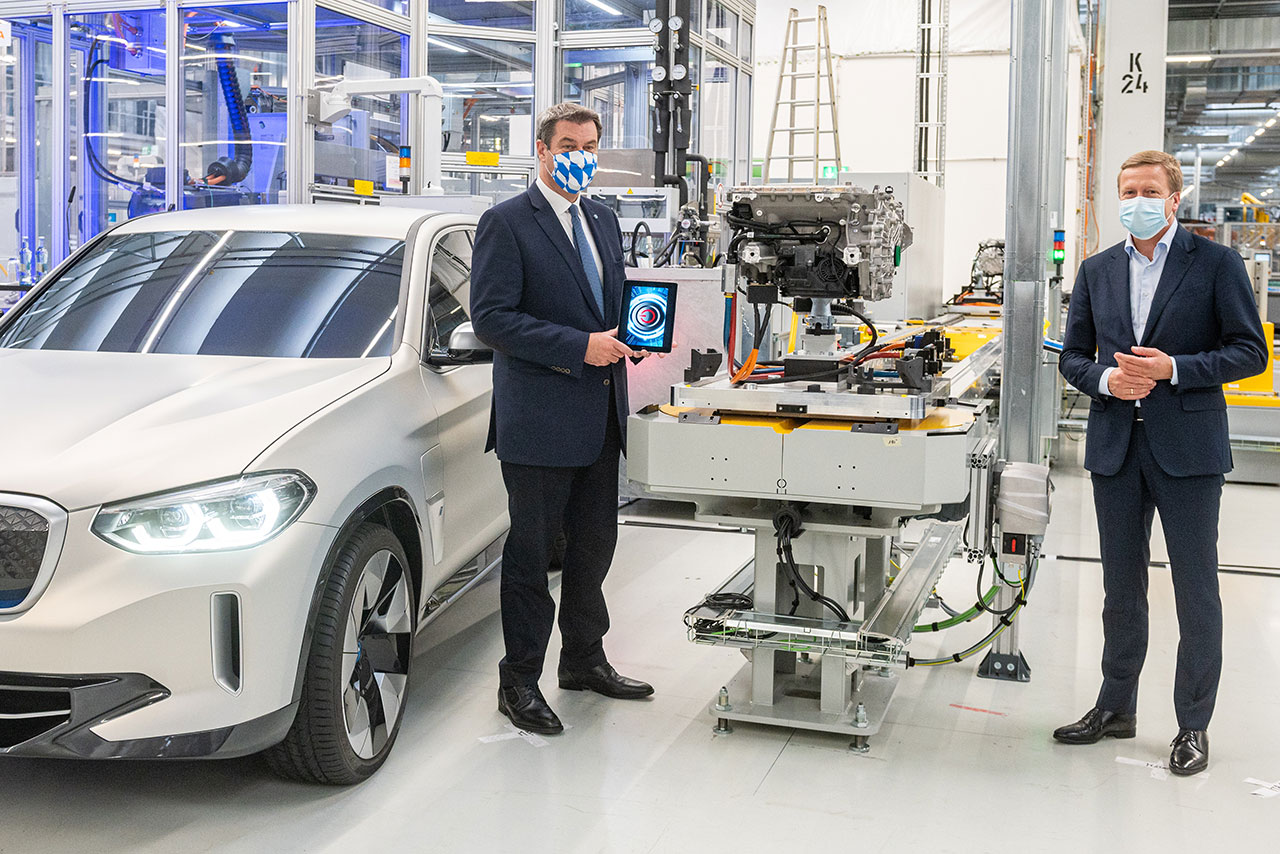
Der bayerische Ministerpräsident Markus Söder und der Vorstandsvorsitzende der BMW AG, Oliver Zipse, nahmen die Produktion des neuen, hochintegrierten BMW E-Antriebs symbolisch in Betrieb.
Mit der fünften Generation des BMW E-Antriebs, der in Dingolfing künftig gefertigt wird, werden E-Motor, Getriebe und Leistungselektronik in einem zentralen Gehäuse zusammengefasst. Die neue Generation des BMW E-Antriebs kommt erstmals im neuen BMW iX3 zum Einsatz, der noch im Spätsommer dieses Jahres in China seinen Produktionsstart haben wird.
In ihrem Kompetenzzentrum in Dingolfing produziert die BMW Group künftig auf acht Produktionslinien E-Antriebskomponenten, also Batteriemodule, Hochvoltbatterien und E-Motoren, um damit ihre elektrifizierten Fahrzeuge auszustatten. In den kommenden Jahren wird das Unternehmen weitere vier Linien aufbauen, so dass der Standort die Produktionskapazität deutlich erhöht. Mittelfristig werden bis zu 2.000 Beschäftigte in der Produktion der E-Antriebe am Standort Dingolfing tätig sein.
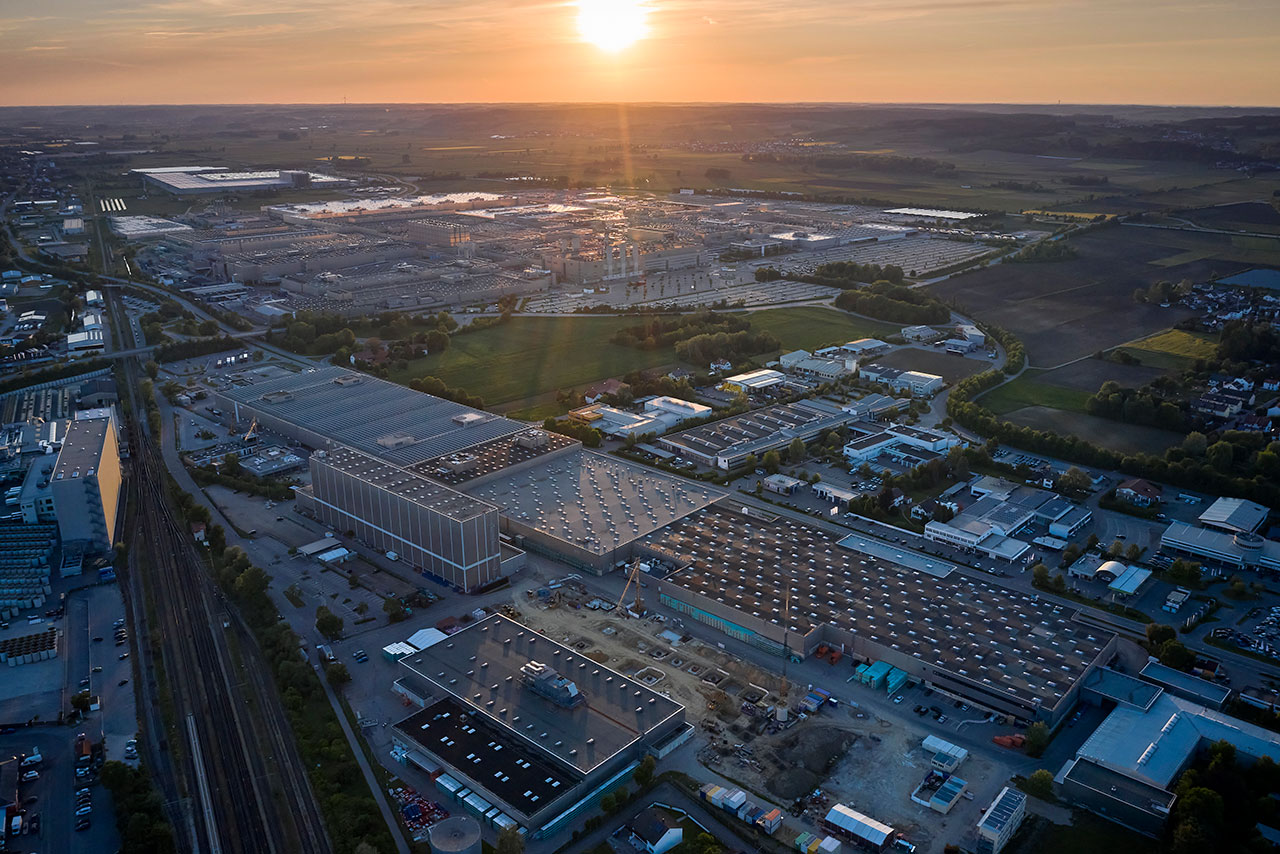
Seit 2013 werden in Dingolfing E-Antriebskomponenten produziert, nun baut die BMW Group ihre Kapazitäten am Standort deutlich aus.
Oliver Zipse, Vorsitzender des Vorstands der BMW AG, sagte anlässlich der Eröffnung: „Wir fahren die Elektromobilität weiter hoch und setzen Maßstäbe bei der Transformation unserer Industrie. Schon 2022 werden wir allein in Dingolfing E-Antriebe für über eine halbe Million elektrifizierte Fahrzeuge pro Jahr fertigen können. Gleichzeitig produzieren wir vollelektrische Fahrzeuge, Plug-in-Hybride und Modelle mit Verbrennungsmotor im jeweils nachgefragten Mix auf einem Band und bieten unseren Kunden so die ‚Power of Choice‘. Das zeigt: Wir haben die Weichen gestellt, um den Wandel unserer Industrie zu einer echten Erfolgsgeschichte zu machen.“
Inhouse-Produktion von Hochvoltbatterien und E-Motoren.
Bereits 2021 soll ein Viertel der in Europa verkauften Fahrzeuge der BMW Group einen elektrischen Antrieb haben, 2025 ein Drittel und 2030 die Hälfte. Im Jahr 2023 wird die BMW Group ihren Kunden 25 elektrifizierte Modelle anbieten, rund die Hälfte davon mit rein elektrischem Antrieb. Die BMW Group verfügt über eine umfassende Kompetenz entlang der gesamten Wertschöpfungskette. Sowohl der neue, hochintegrierte E-Antrieb als auch die neuen Hochvoltbatterien wurden inhouse in enger Zusammenarbeit zwischen den Fachabteilungen aus der Entwicklung und der Produktion entwickelt. Im Kompetenzzentrum E-Antriebsproduktion bündelt das Unternehmen das Know-how für die Großserienproduktion von E-Antrieben und stellt eine effiziente Produktion sicher, die kurzfristig auf die jeweilige Nachfrage nach Antrieben für voll- oder teilelektrische Fahrzeuge reagieren kann.
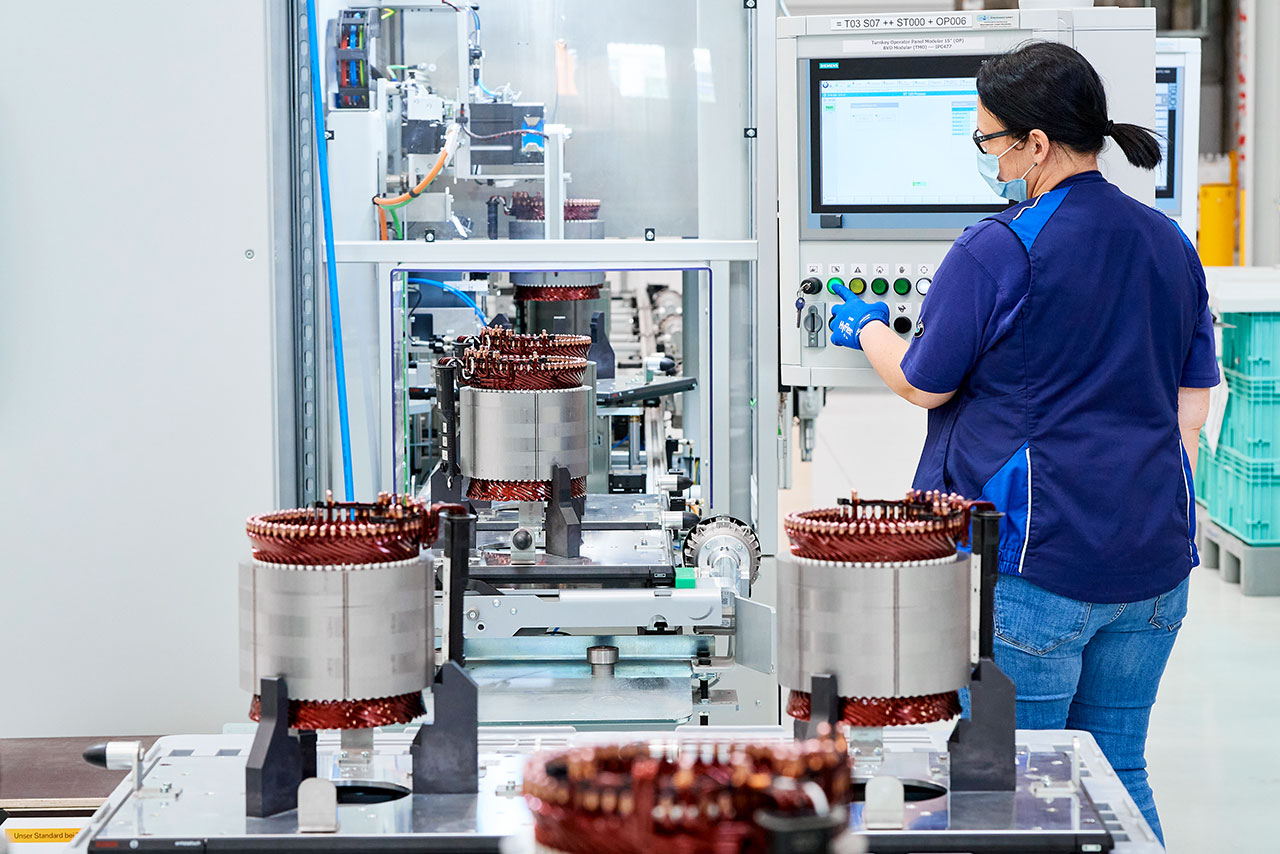

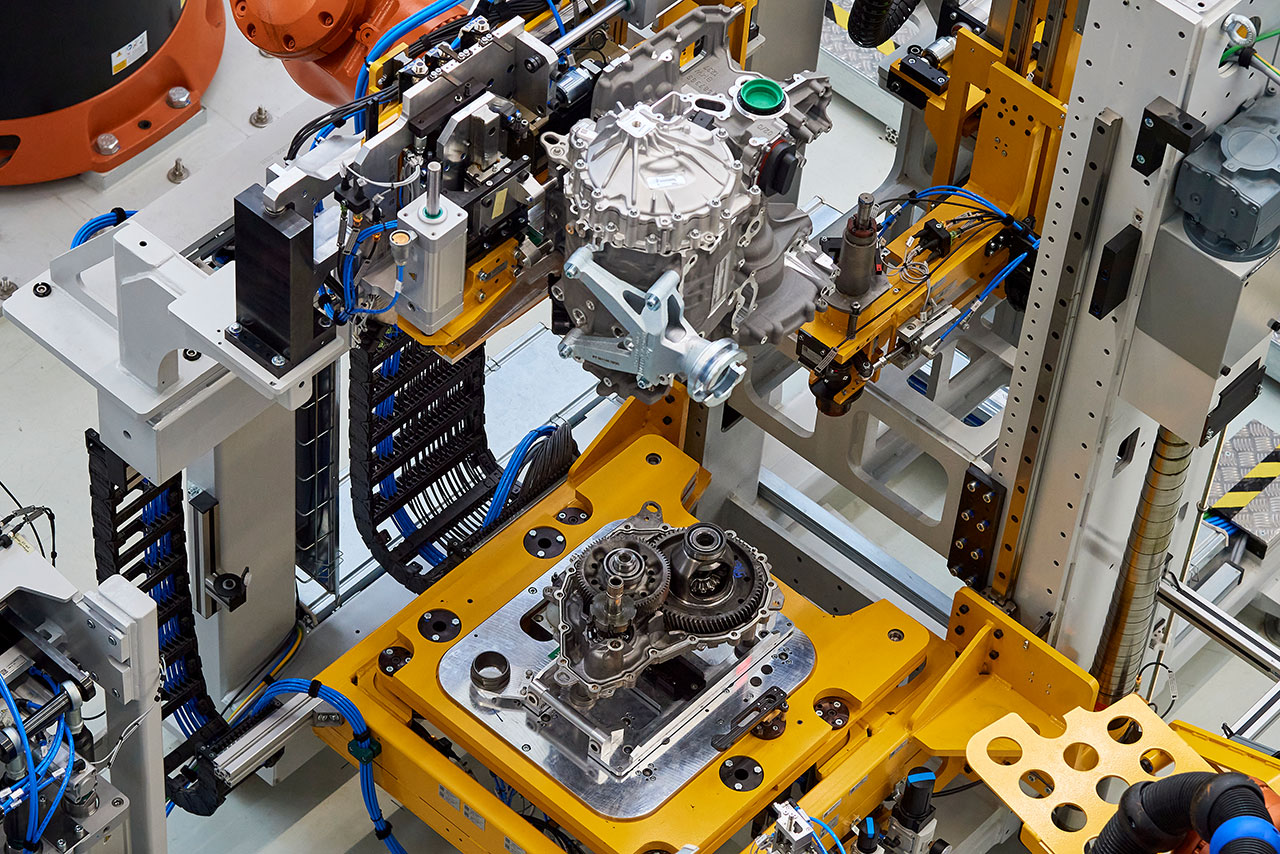
Der BMW E-Antrieb der fünften Generation: E-Motor, Getriebe und Leistungselektronik sind in einem gemeinsamen Gehäuse untergebracht.
Auch für die neuen Hochvoltbatterien der fünften Generation hat das Kompetenzzentrum den Produktionsprozess der Batteriemodule technisch standardisiert und so weiterentwickelt, dass - entsprechend des wachsenden Angebots an elektrifizierten Fahrzeugmodellen - verschiedene Modulvarianten auf der gleichen Linie gefertigt werden können. Damit stellt das Unternehmen nicht nur produktionstechnologisch die Weichen, sondern sichert auch Arbeitsplätze und Schlüsselqualifikationen.
Standort Dingolfing: Transformation zur Elektromobilität.
Schon heute sind rund zehn Prozent aller in Dingolfing produzierten Fahrzeuge elektrifiziert. Mit dem Anlauf des BMW iNEXT im Jahr 2021 wird das Werk Dingolfing in der Lage sein, vollelektrische Fahrzeuge, Plug-in-Hybride und Modelle mit Verbrennungsmotor auf einem Band zu produzieren.
Dingolfing verfügt über eine langjährige Expertise im Bau von Komponenten für E-Fahrzeuge. Schon seit 2013 laufen hier im Serienbetrieb die Hochvoltbatterien für den BMW i3 vom Band. Seit 2015 produziert der Standort zudem E-Motoren. Ein Großteil der Hochvoltbatterien und E-Motoren aller elektrifizierten Fahrzeuge der BMW Group kommt aus dem Kompetenzzentrum E-Antriebsproduktion.
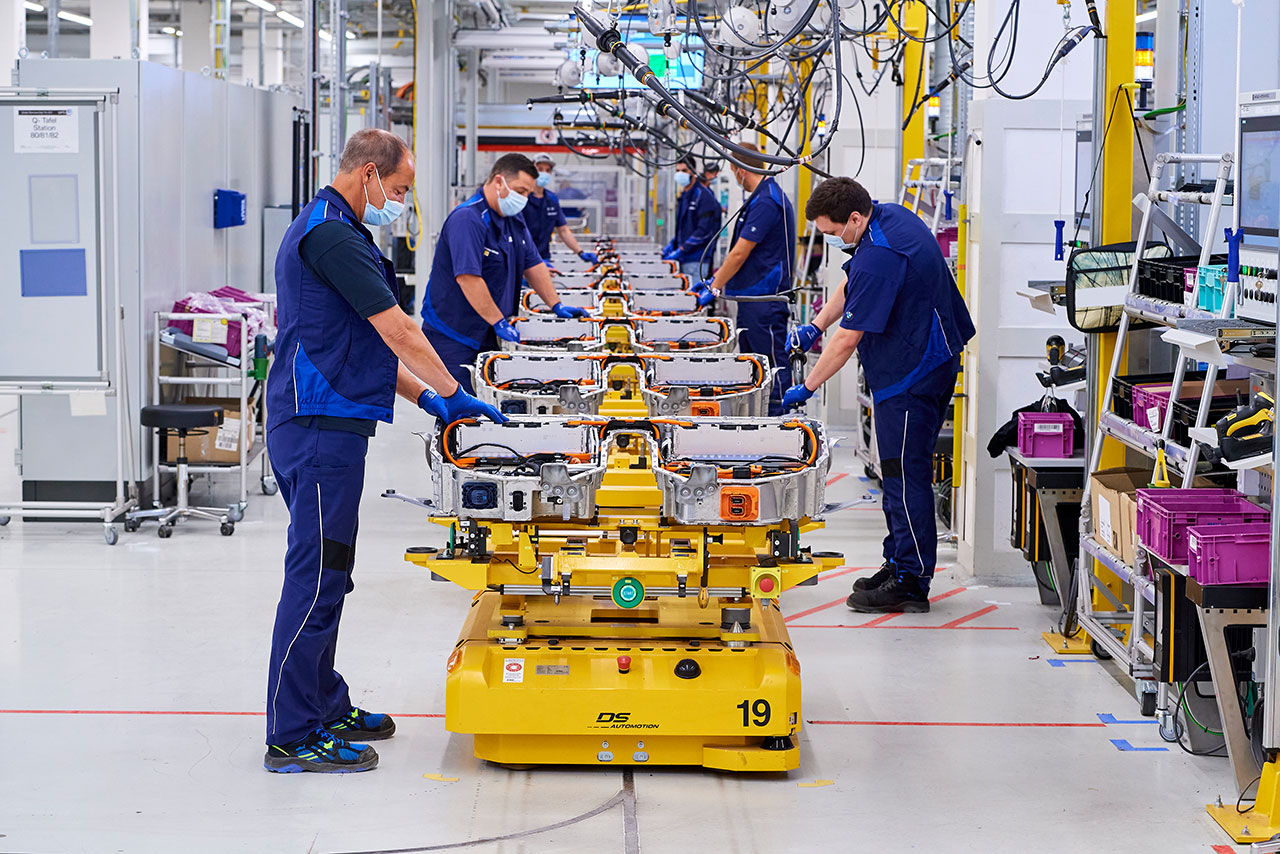
Die Hochvoltspeicher der fünften Generation der BMW eDrive Technologie sind skalierbar, modular und dadurch flexibel einsetzbar.
Die fünfte Generation der BMW eDrive Technologie.
Anlässlich der Eröffnung hat das Kompetenzzentrum mit der Produktion des E-Antriebs der fünften Generation begonnen. Bei dieser hochintegrierten E-Antriebskomponente sind der E-Motor, das Getriebe und die Leistungselektronik in einem gemeinsamen Gehäuse untergebracht. Zudem werden keine Seltenen Erden mehr benötigt. Das Antriebssystem ist mit allen Fahrzeugkonzepten kompatibel und wird in verschiedenen Leistungsstufen für unterschiedliche Modelle verfügbar sein. Die hochintegrierte Bauweise des Systems ermöglicht eine deutliche Steigerung der Leistungsdichte.
Die fünfte Generation der BMW eDrive Technologie umfasst zudem neue, leistungsfähigere Hochvoltbatterien. Diese können dank ihrer skalierbaren, modularen Baukastenauslegung flexibel in der jeweiligen Fahrzeugarchitektur und den jeweiligen Produktionsstandorten zum Einsatz kommen. Aktuell bereitet das Kompetenzzentrum den Hochlauf der Produktion dieser neuen Hochvoltbatterien vor.