The BMW Group has been making e-drives in Dingolfing since 2013. Now, production of the fifth generation begins. The company is massively increasing capacity and opening a separate Competence Centre for E-Drive Production. Up to 2,000 employees will build BMW e-drives here for as many as 500,000 vehicles per year.
The BMW Group has opened the Competence Centre for E-Drive Production at its largest European manufacturing location in Dingolfing. In this way, the company is stepping up its e-mobility ramp-up and setting new standards for the transformation of the industry with its production. Electric powertrain components have been produced in Dingolfing since 2013 and the BMW Group is now significantly expanding its capacity.
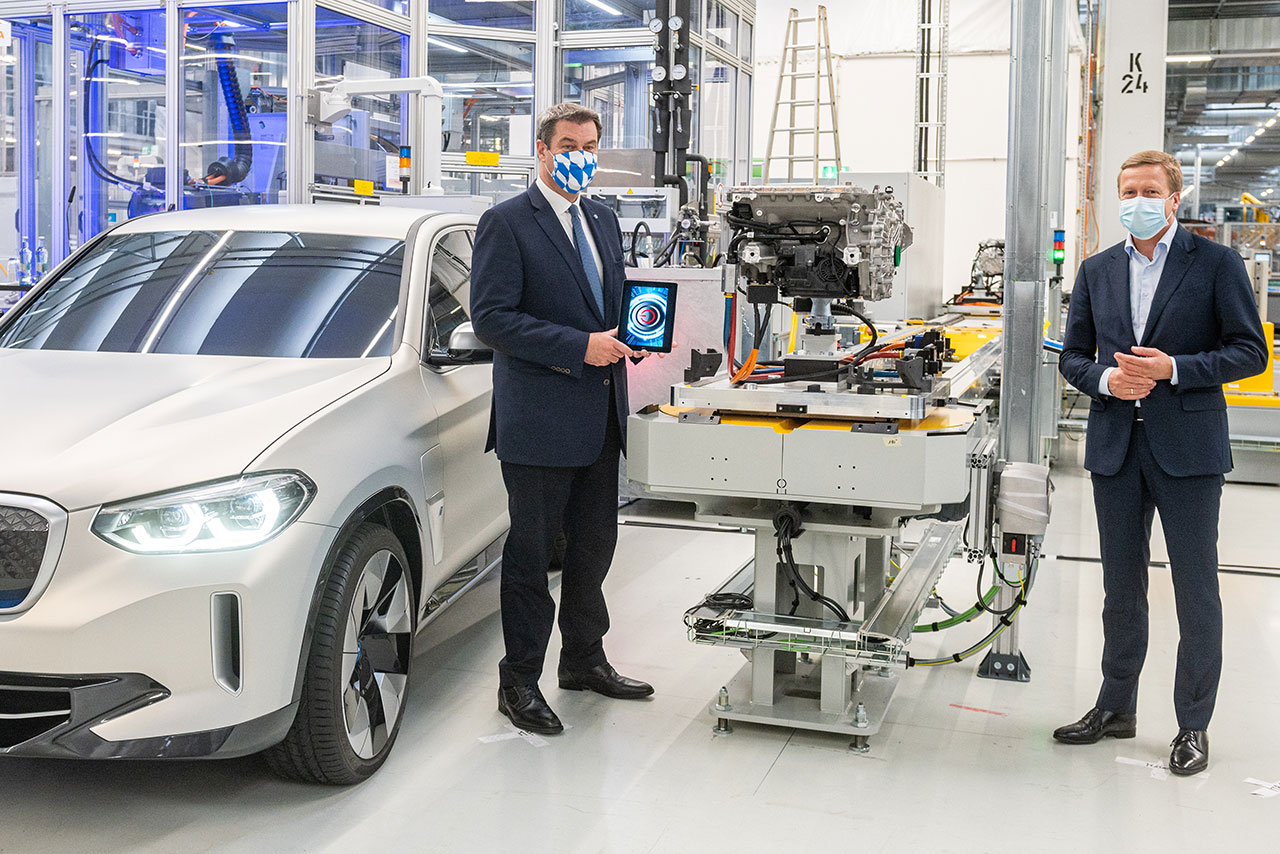
Bavarian Minister-President Markus Söder and Chairman of the Board of Management of BMW AG Oliver Zipse symbolically launched production of the new, highly integrated BMW e-drive.
The fifth-generation BMW e-drive that will be produced in Dingolfing combines the electric motor, transmission and power electronics in a central housing. The new generation of the BMW e-drive will be used for the first time in the new BMW iX3, which will go into production in China in late summer.
At the Competence Centre in Dingolfing, the BMW Group will produce electric powertrain components, such as battery modules, high-voltage batteries and electric motors for installation in electrified vehicles on eight production lines. Over the coming years, the company will set up four additional lines, which will boost the location’s production capacity significantly. Up to 2,000 employees will work in production of e-drives at the Dingolfing location in the medium term.
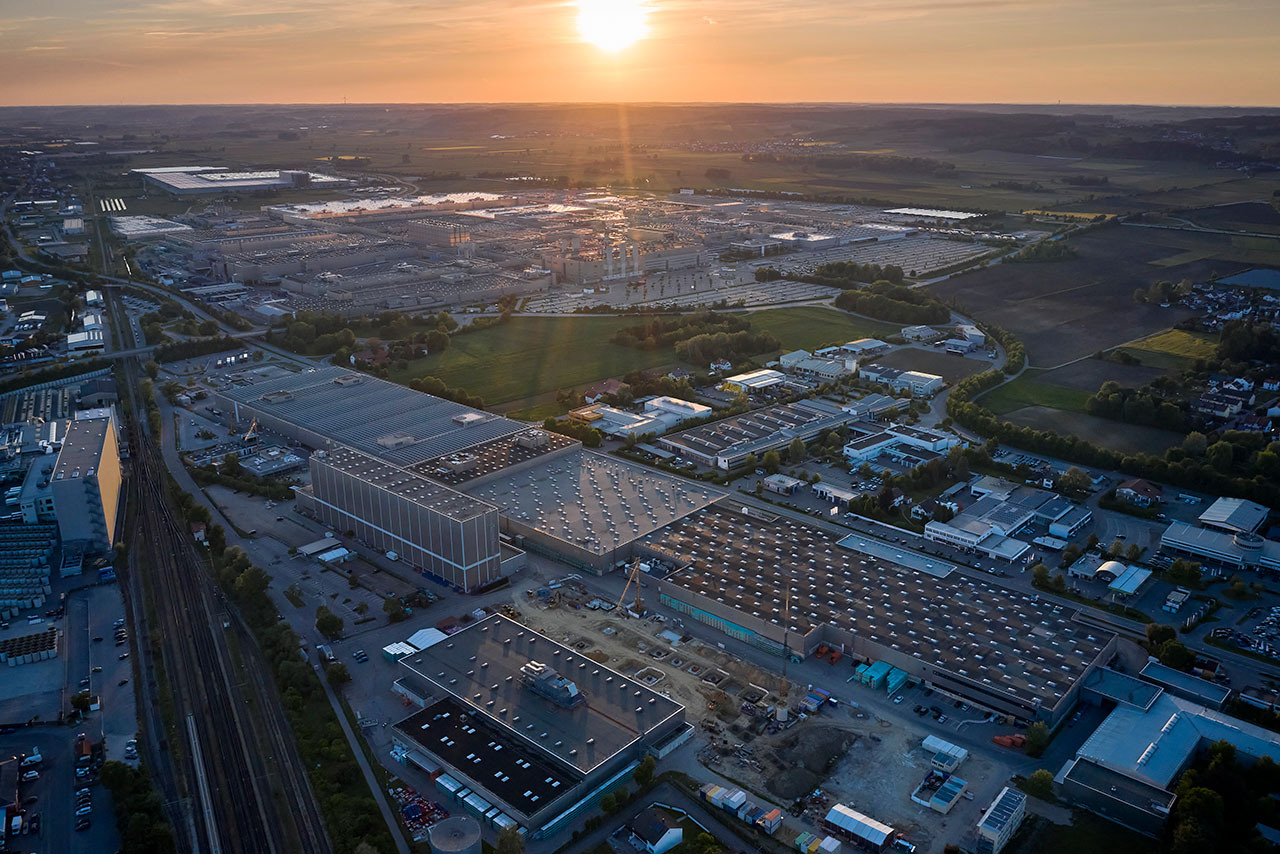
Electric powertrain components have been produced in Dingolfing since 2013. The BMW Group is now significantly expanding capacity at the site.
Oliver Zipse, Chairman of the Board of Management of BMW AG, said at the inauguration: “We continue to ramp up electromobility and set standards for the transformation of our industry. By 2022, we will be able to produce e-drives for more than half a million electrified vehicles per year in Dingolfing alone. At the same time, we will produce a mix of fully-electric vehicles, plug-in hybrids and models with a combustion engine on a single line, as required by demand, so we can offer our customers the ‘Power of Choice’. This shows how we have paved the way for making the shift in our industry a real success story.”
In-house production of high-voltage batteries and electric motors.
A quarter of BMW Group vehicles sold in Europe should have an electric drive train by 2021; a third in 2025 and half in 2030. In 2023, the BMW Group will offer its customers no fewer than 25 electrified models – around half of them with a pure electric drive train. The BMW Group possesses extensive expertise throughout the entire value chain. Both the new, highly integrated e-drive and new high-voltage batteries were developed in-house in close cooperation between development departments and production. The company is pooling its expertise in large-scale standard production of electric drive trains at the Competence Centre for E-Drive Production and thereby ensuring efficient production that can respond to demand for drive trains for fully and partially-electric vehicles at short notice.
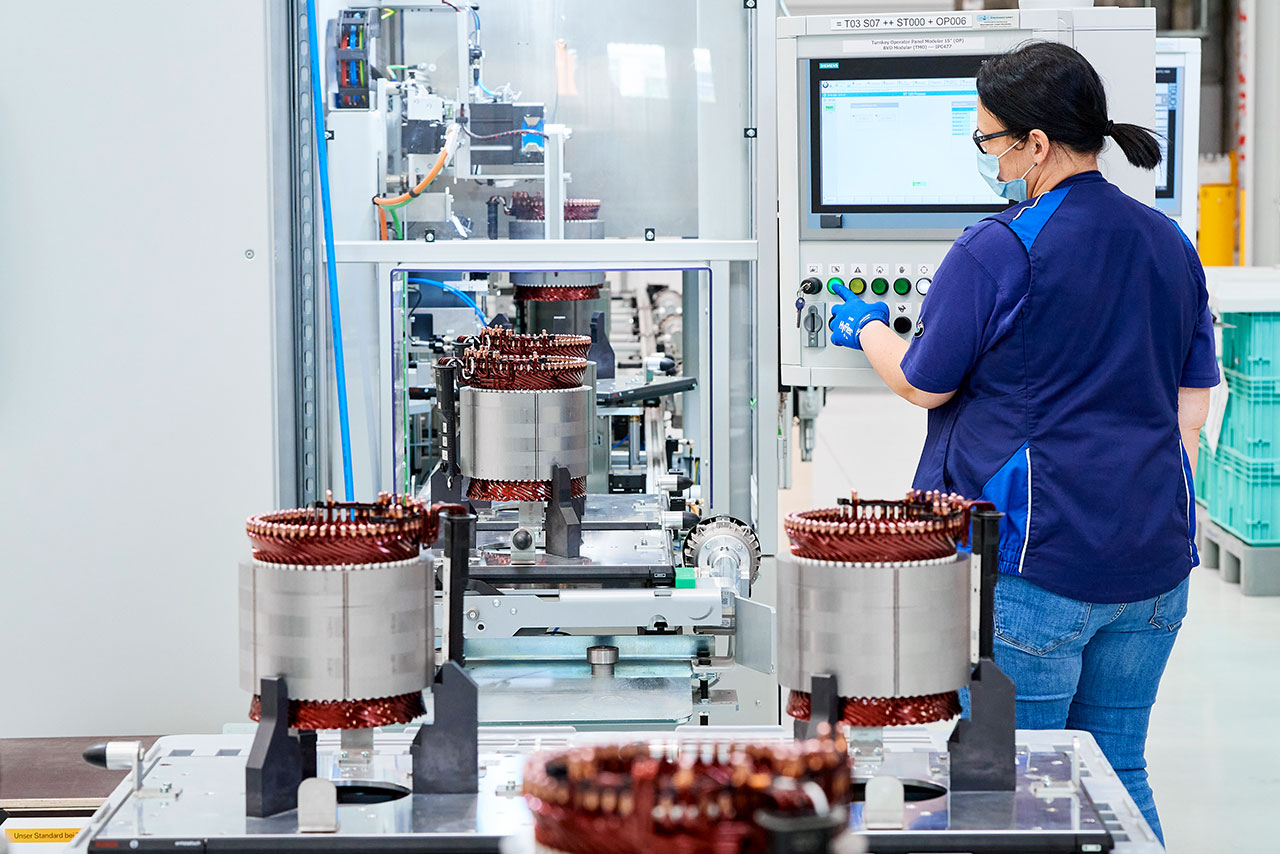
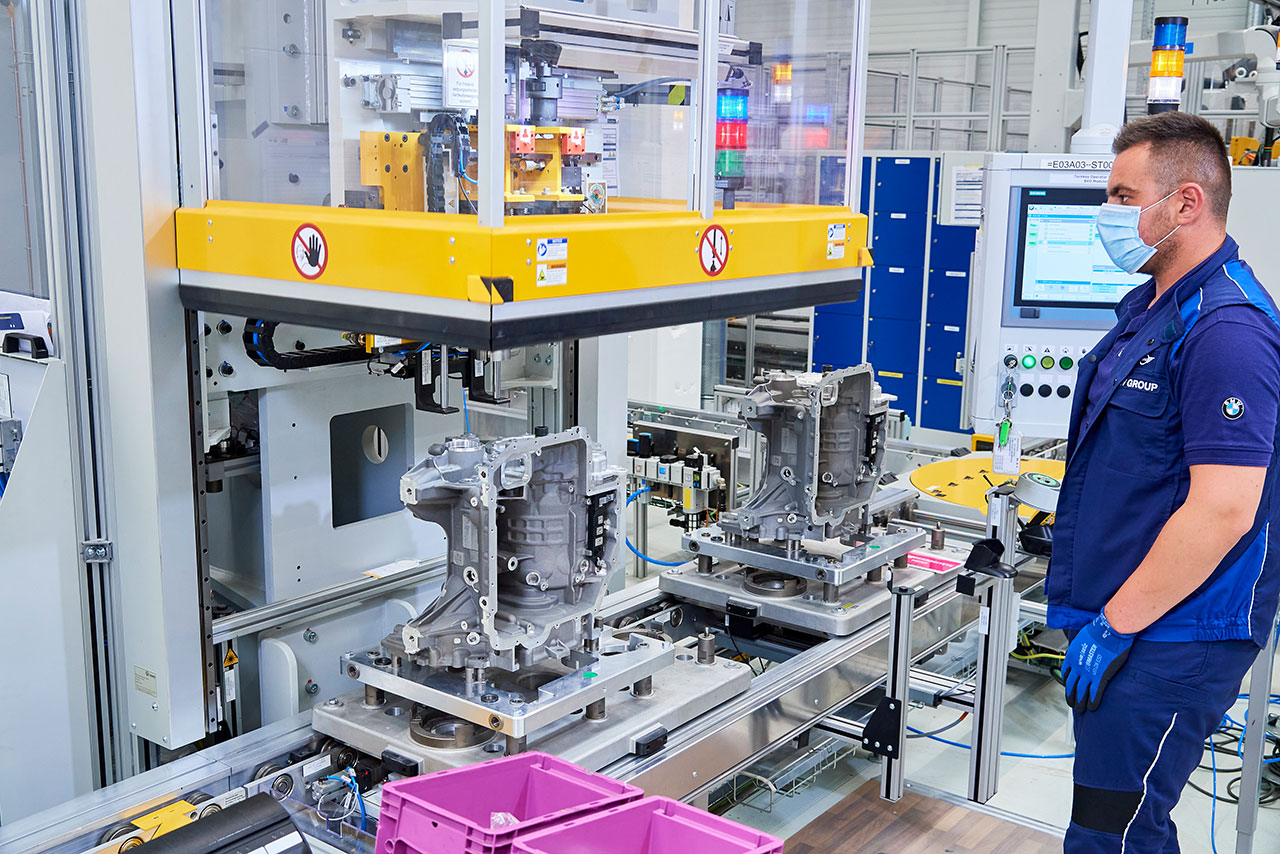
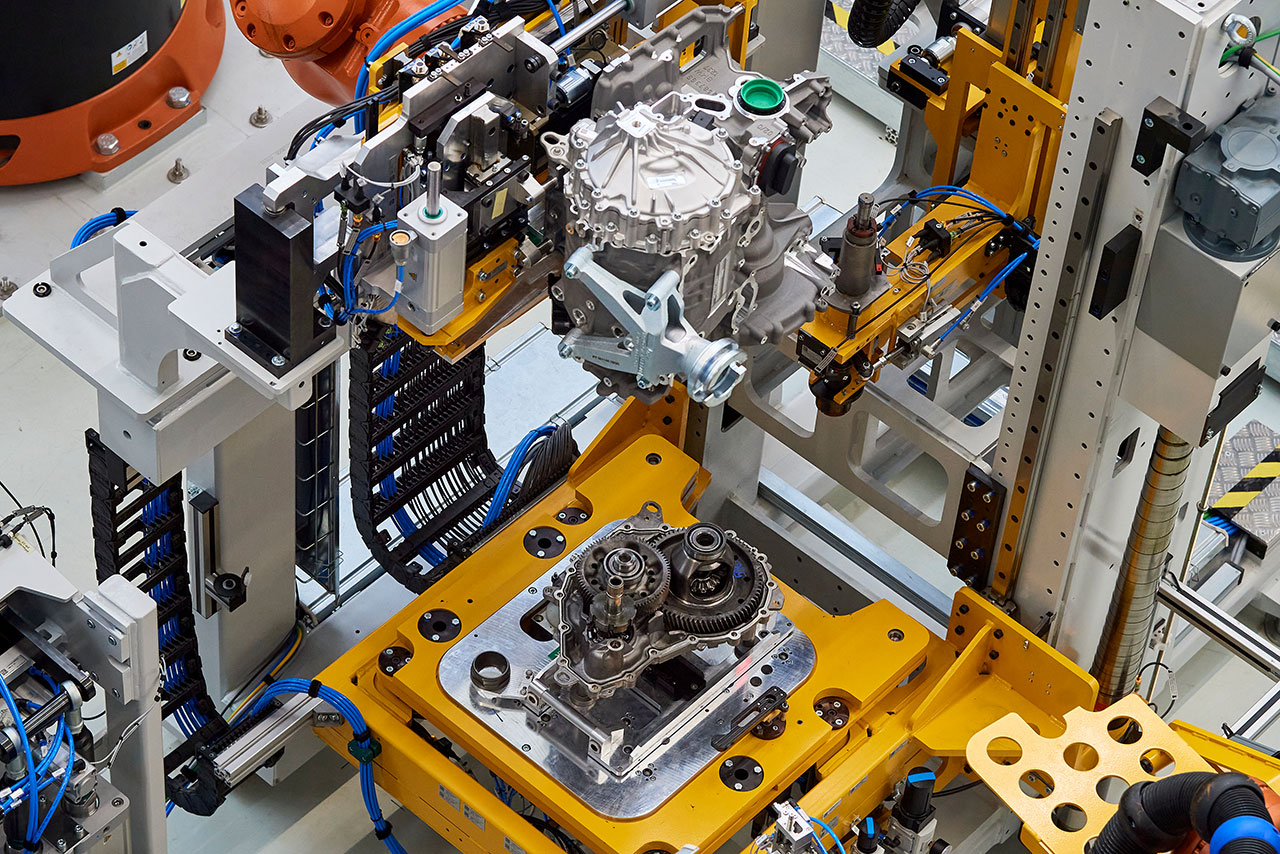
The fifth-generation BMW e-drive combines electric motor, transmission and power electronics in one housing.
The Competence Centre has also standardised the technology used in production of battery modules for the new fifth-generation high-voltage batteries, refining the process to reflect the growing range of electrified models and allowing different module variants to be produced on the same line. In this way, the company is not only setting the course for production technology, but also securing jobs and key qualifications.
Dingolfing site transforms itself for electromobility.
Today, around ten percent of the vehicles produced in Dingolfing are already electrified. With the launch of the BMW iNEXT in 2021, Plant Dingolfing will be capable of producing fully-electric vehicles, plug-in hybrids and models with a combustion engine on a single line.
Dingolfing has years of expertise building components for electric vehicles. Series-produced high-voltage batteries for the BMW i3 have been coming off the line here since 2013. This location has also produced electric motors since 2015. The majority of high-voltage batteries and electric motors for all BMW Group electrified vehicles come from the Competence Centre for E-Drive Production.
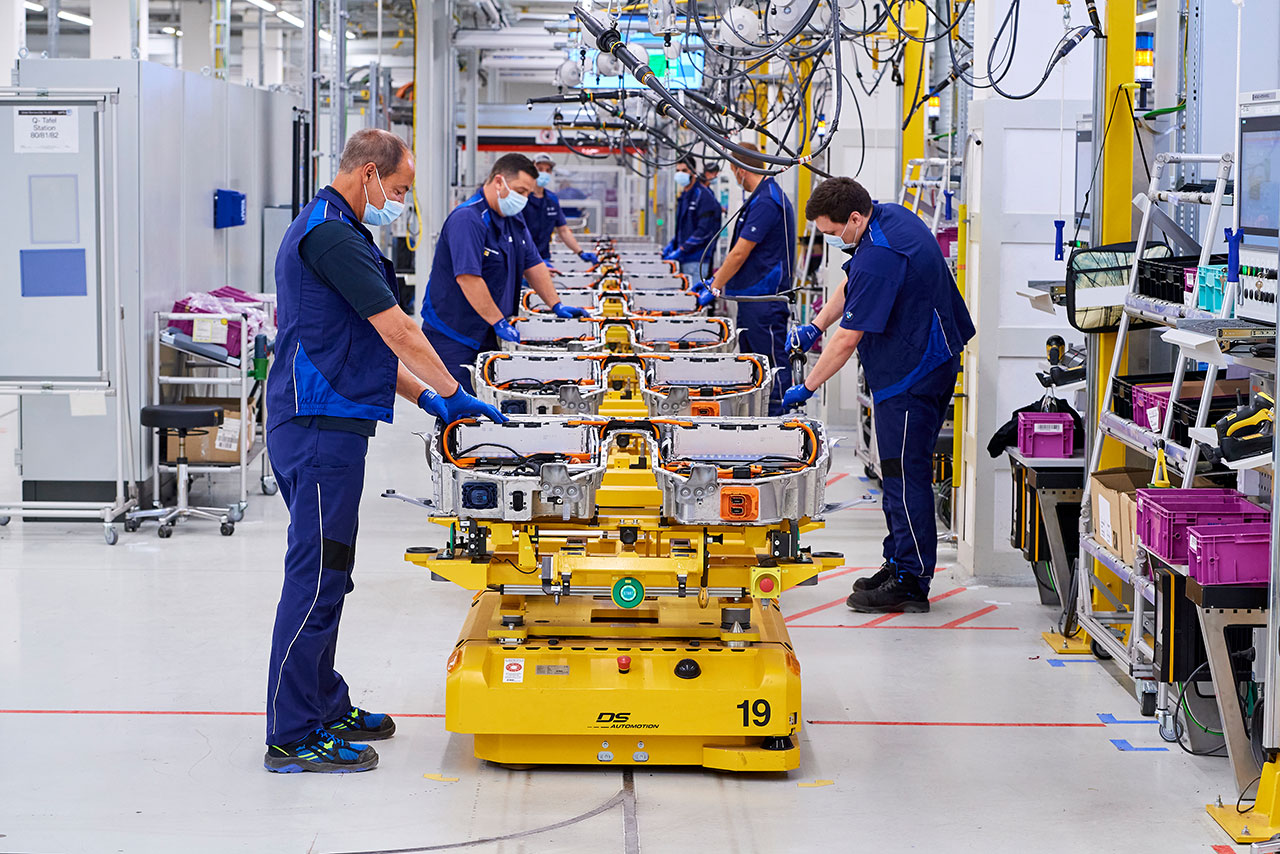
High-voltage batteries with fifth-generation BMW eDrive technology are scalable, modular and flexible in how they can be used.
Fifth-generation BMW eDrive technology.
On the same day as the official opening, the Competence Centre also began production of the fifth-generation electric drive train. This highly integrated electric powertrain component combines the electric motor, transmission and power electronics in one housing. Rare earths are also no longer required. The drive train is compatible with all vehicle concepts and will be available with various power levels for different models. The system’s highly integrated design increases power density significantly.
The fifth-generation BMW eDrive technology features new and more powerful high-voltage batteries. Thanks to their scalable, modular design, these can be used flexibly in the respective vehicle architecture and at the respective production locations. The Competence Centre is currently preparing to ramp up production of these new high-voltage batteries.