The BMW Group has been producing high-voltage batteries for our fully-electric vehicles and plug-in hybrids for a long time. We have also been focusing a great deal on battery cells for over 10 years, to ensure we have the same level of knowledge as established cell manufacturers. This article explains the difference between a battery cell and a high-voltage battery, and outlines the six steps that go into building battery cell prototypes at our new Battery Cell Competence Centre. We have pooled all our knowledge and know-how in this area at this one location.
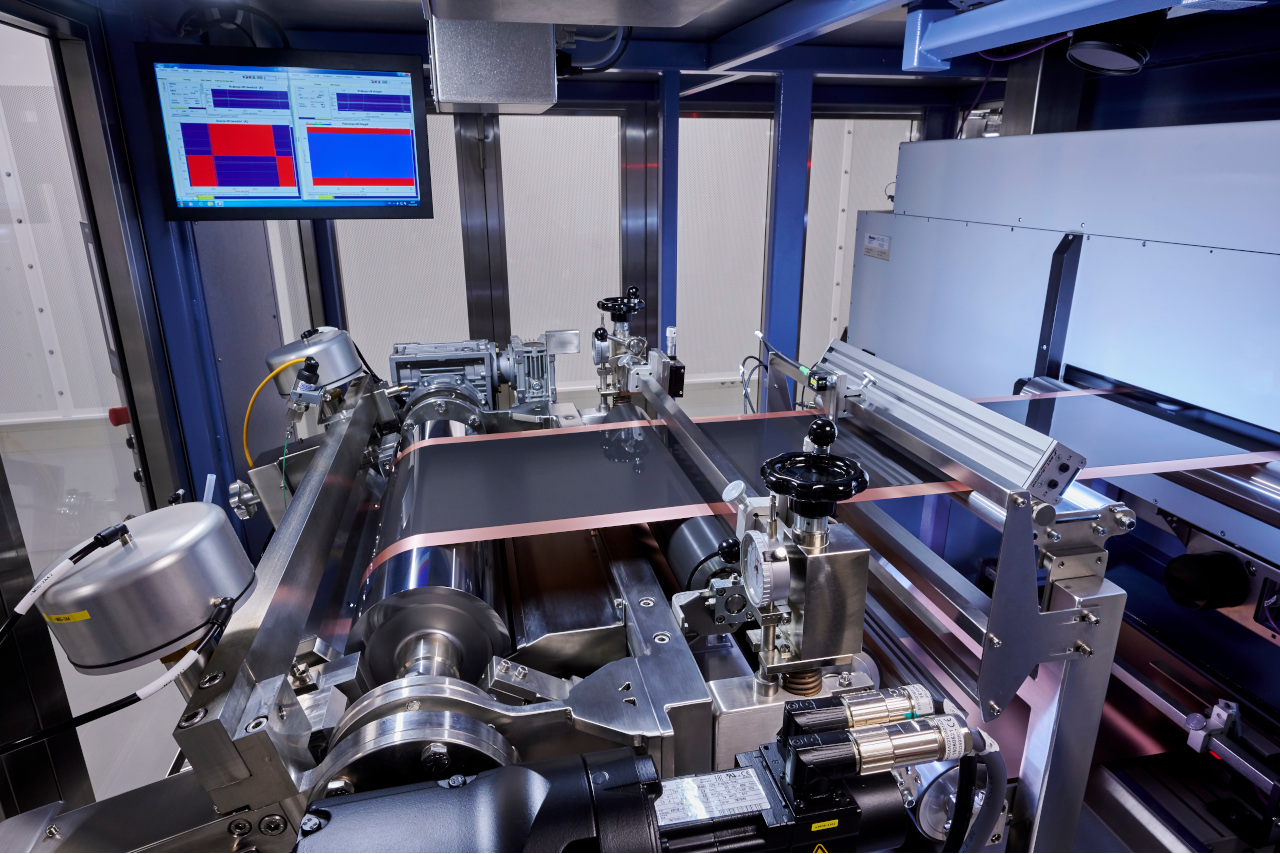
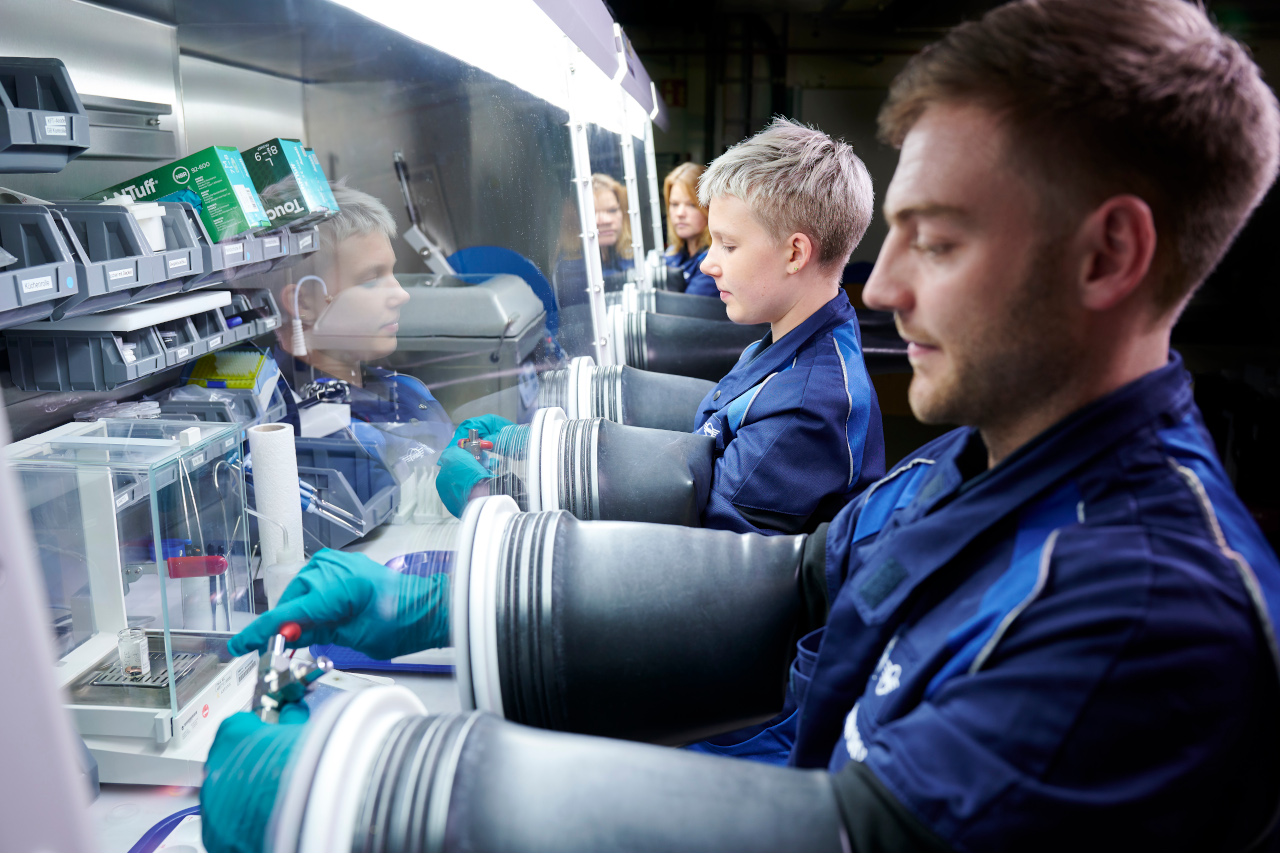
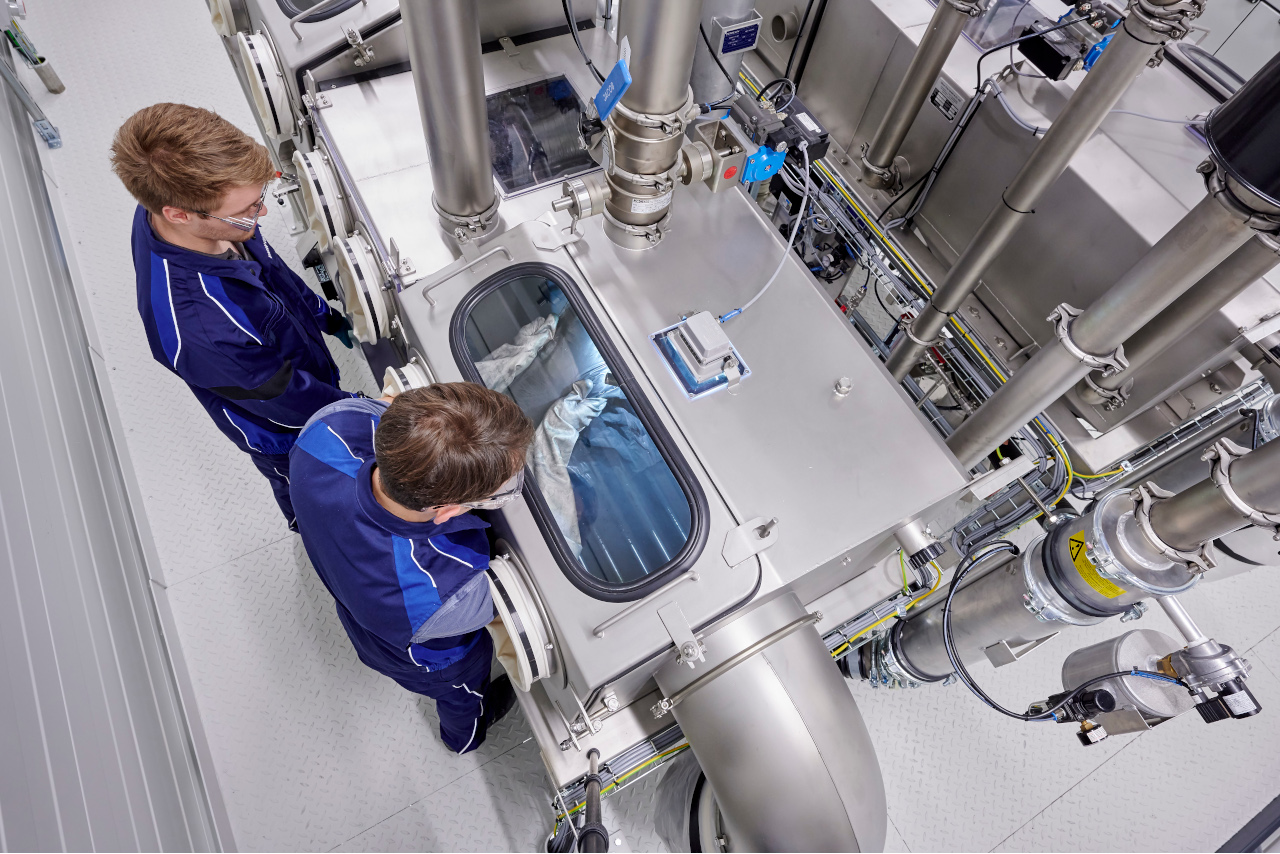
From development to material selection to battery cell prototypes and comprehensive real-life testing – everything takes places at the new Battery Cell Competence Centre north of Munich.
Battery cell: We know how to do it
We have been analysing battery cells for more than 10 years: materials, mechanics, design and recycling. This gives us the same level of knowledge as established cell manufacturers. At the same time, we want to further expand our battery cell and production know-how – also in the area of large-scale manufacturing. Building battery cell prototypes enables full analysis and understanding of value chain processes for the cells. This allows us to work at the same level as our suppliers and enable them for technology and production. Our strategy of not setting up our own standard production of battery cells has worked extremely well so far. Whether we produce the cells ourselves in mass production at a later date depends to a large extent on the development of the supplier market. As long as there is global competition among sufficient suppliers, there will be no significant dependency.
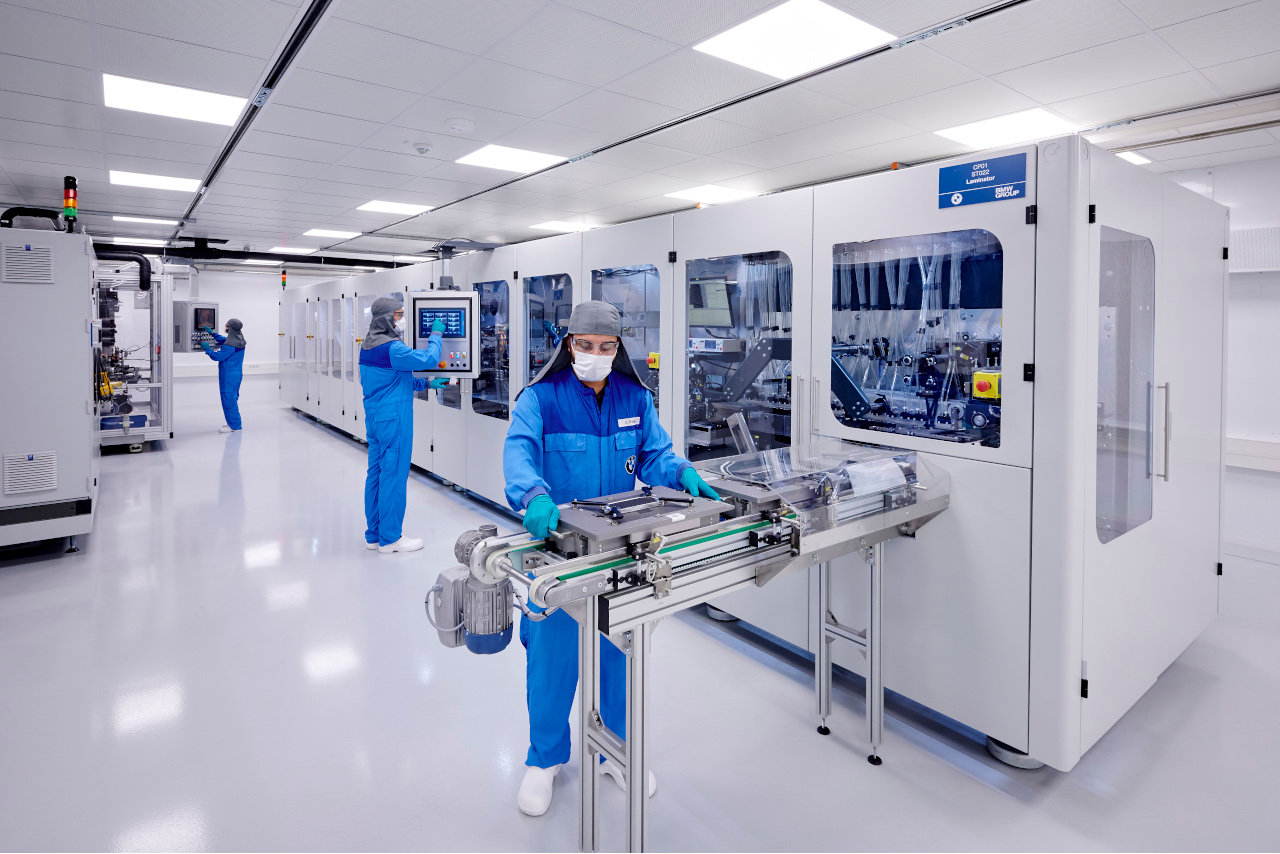
We are investing 200 million euros in the Battery Cell Competence Centre and creating up to 200 jobs. The building houses 8,000 m² of workshops, testing equipment, laboratories and prototype production facilities, including 1,000 m² of drying rooms and 4,000 m² of office space.
Cell + cell + … = high-voltage battery
However, what we have always produced ourselves are our high-voltage batteries: The first step is to turn supplied individual cells into high-performance battery modules, which we then combine, in a second step, to create high-voltage batteries. These are controlled by our highly intelligent electronics that are also developed in-house to ensure optimal performance characteristics for our vehicle models. This all takes place at four locations: at our battery factories in Dingolfing (Germany), Spartanburg (USA), Shenyang (China) and at our partner in Rayong (Thailand).
Six steps to create a cell: What happens at the Battery Cell Competence Centre
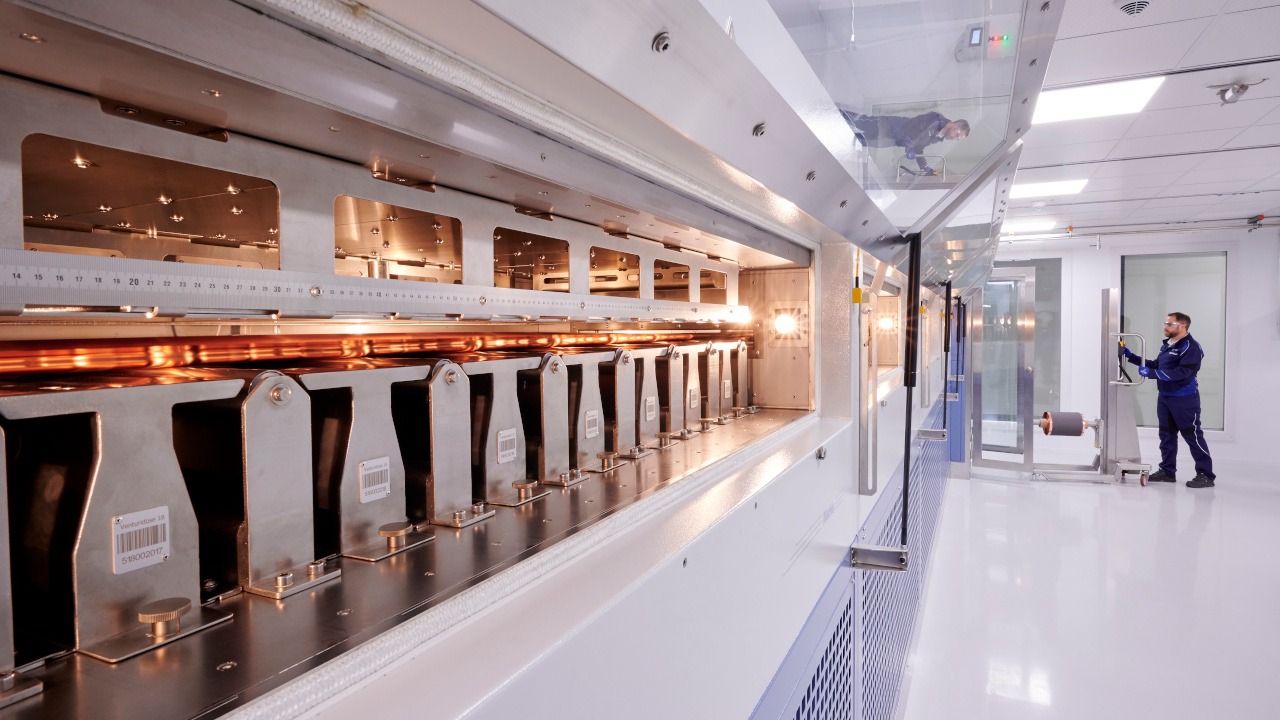
- Material and cell development: The first step is for battery cell specialists to analyse materials and battery cells and refine various concepts.
- Mixing and dosing: The anode (negative pole) and cathode (positive pole) of a battery cell are made of different materials, such as cobalt or lithium. In this production step, the formulas are mixed together, and new combinations tested.
- Coating and drying: The previously mixed electrode pastes are then applied to electrode films and must be allowed to dry.
- Calendering and cutting: In this process step, the electrode paste coating the foil is compacted by rollers, so it can then be cut into smaller electrode bands.
- Assembly: The battery cells are then assembled, and the battery cell housing welded.
- Analysis and test area: One of the next steps is forming, in which freshly manufactured cells are charged and discharged. This has a significant impact on a battery cell’s properties. Various tests are also conducted in the safety lab to test the resistance and service life of different battery cell types.