Produktionsnetzwerk für die Zukunft.
Zum „Tag der Batterie“ zeigen wir einen kleinen Ausschnitt davon, wie die BMW Group an ihren Produktionsstandorten weltweit das Thema Elektrifizierung umsetzt und die Mobilität der Zukunft gestaltet.
„Klimaschutz ist jetzt relevant und nicht erst übermorgen“, so BMW Group CEO Oliver Zipse. Nicht zuletzt daher erhöht die BMW Group weiter deutlich die Schlagzahl beim Ausbau der E-Mobilität. Im Jahr 2023 wird die BMW Group 25 elektrifizierte Modelle auf der Straße haben, die Hälfte davon mit rein elektrischem Antrieb. 2030 soll die Hälfte der in Europa verkauften Fahrzeuge der BMW Group einen elektrifizierten Antrieb haben. Zur Realisierung dieser ehrgeizigen Ziele setzt die BMW Group bei allen Bestandteilen der BMW eDrive Technologie auf Eigenentwicklungen, und baut ihre Produktionskapazitäten für elektrifizierte Fahrzeuge und E-Antriebe kontinuierlich aus.
Berlin
Bereits auf der #NEXTGen 2020 vorgestellt, erweitert das seriennahe Teaser-Fahrzeug BMW Motorrad Definition CE 04 die Elektroflotte von BMW Motorrad. Die Umbauarbeiten für die zukünftige Serienfertigung im Berliner Werk laufen auf Hochtouren. Aktuell wird die bestehende Hochvoltbatteriefertigung technisch erweitert und auf das neue Modell angepasst. Hier läuft bereits der Probelauf für den kommenden Serienbetrieb.
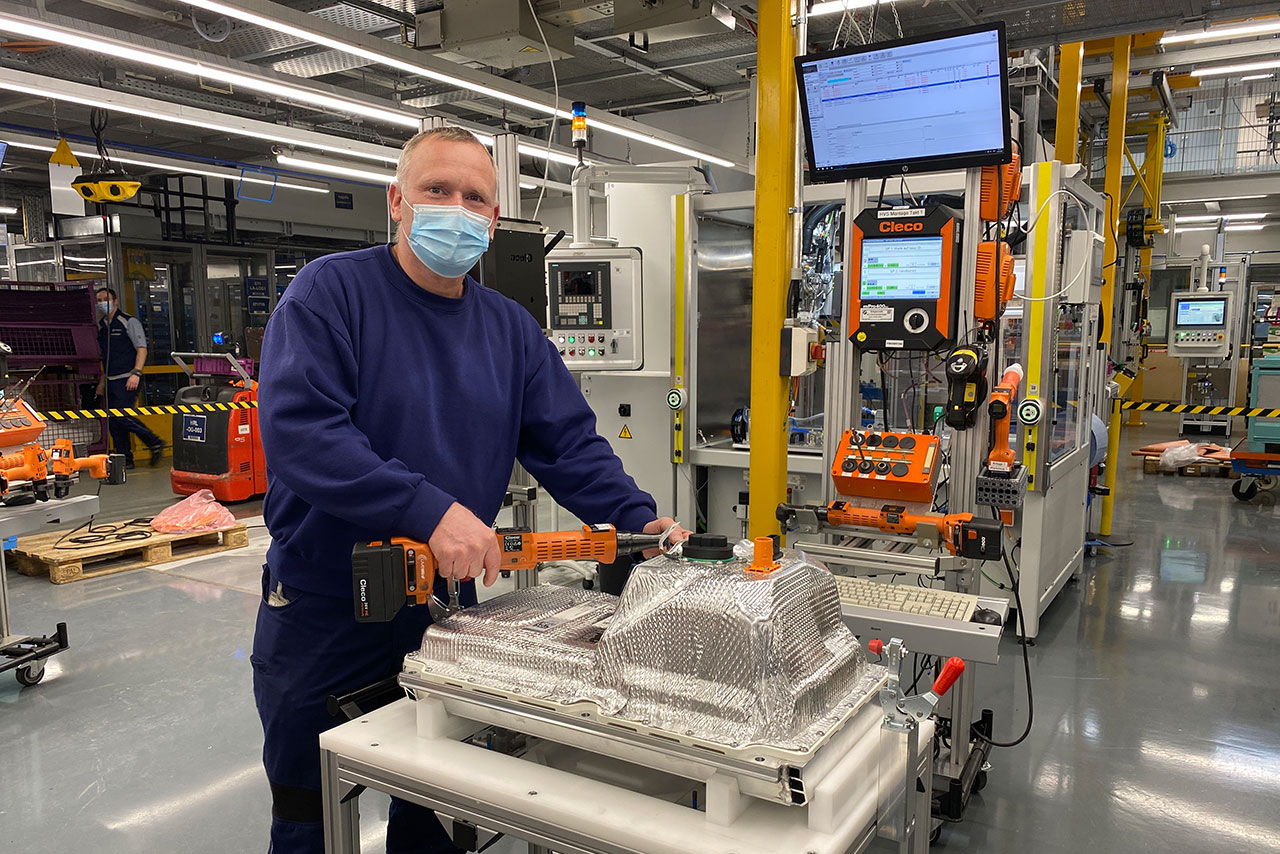
Die in der Batterie verbauten Module der neuesten Generation werden aus dem Werk Dingolfing angeliefert, das Batteriegehäuse wird im Berliner Werk gefertigt. Der Scooter ist ganz auf elektrisches Fahren ausgelegt. Das Serienmodell ist die Weiterentwicklung des BMW Motorrad Concept Link. Es verbindet unter dem Motto „Plugged to Life“ die analoge Welt mit der digitalen und ist sowohl Fortbewegungs- als auch Kommunikationsmittel für den Großstadtpendler.
Dingolfing
Der Standort Dingolfing blickt auf über ein Jahrzehnt Know-how in der Hochvoltbatteriefertigung zurück: zuerst für die BMW ActiveHybrid Modelle und den BMW ActiveE – seit 2013 für die Großserienfertigung des BMW i3 und BMW i8. Mittlerweile ist das Werk 02.20 zum BMW Group Kompetenzzentrum für E-Antriebsproduktion angewachsen: Neben E-Motoren werden dort Batteriemodule gebaut und zu Hochvoltbatterien montiert – anfangs vor allem für Plug-in-Hybride, seit Herbst 2019 mit dem MINI SE auch für vollelektrische Fahrzeuge.
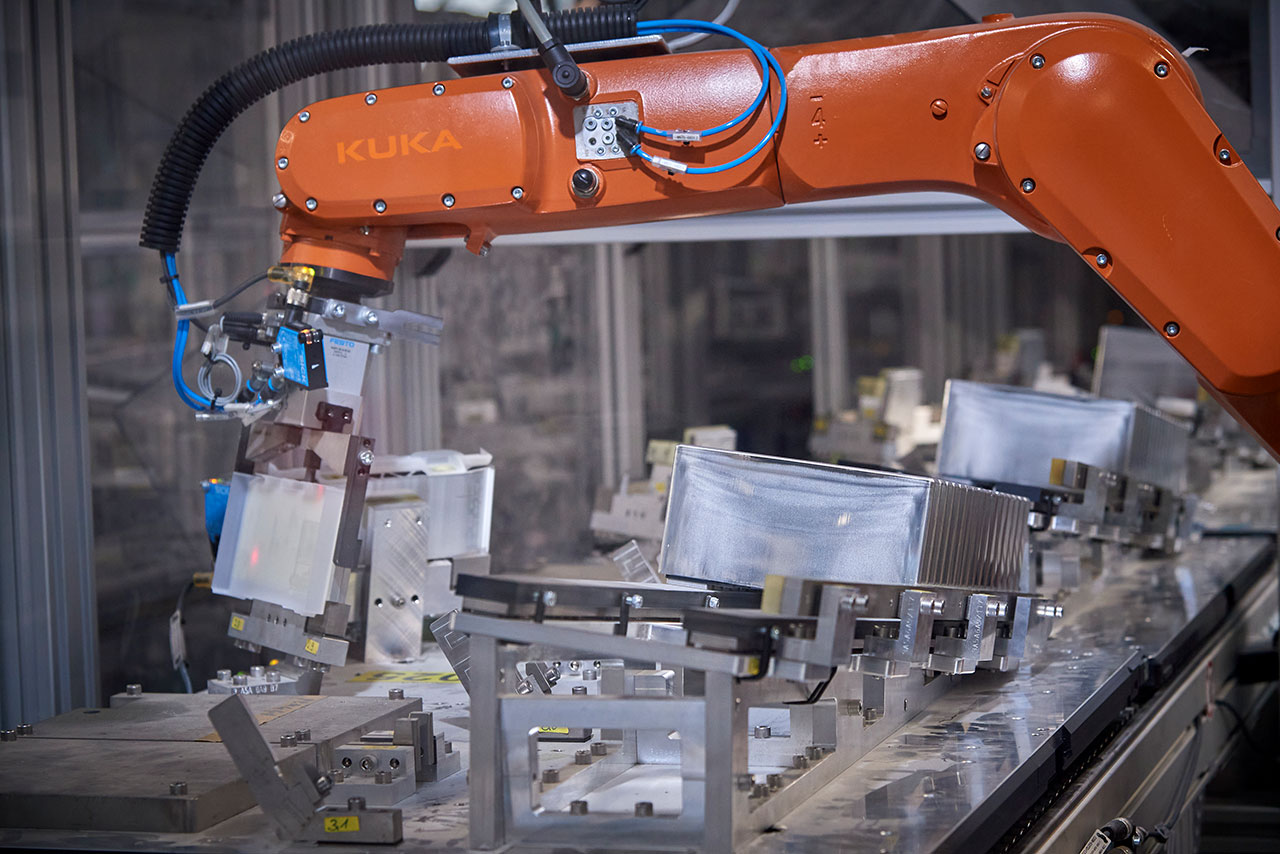
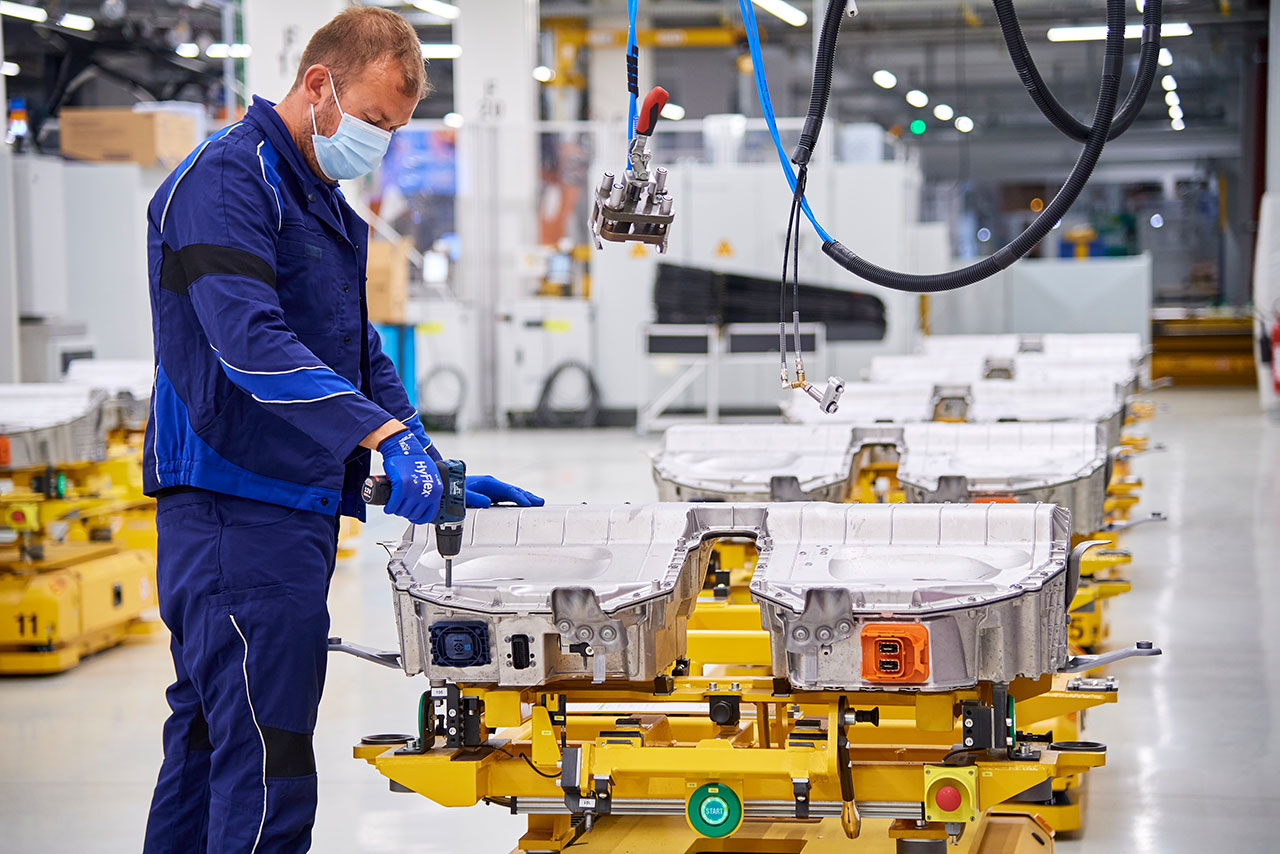
In diesem Jahr läuft die neueste, bereits fünfte, Generation der Hochvoltbatterieproduktion in Dingolfing an. Sie kommt zuerst im BMW iX und BMW i4 zum Einsatz. Das Besondere daran: Unsere Lieferanten haben sich verpflichtet, zur Batteriezellherstellung ausschließlich nachhaltigen „Grünstrom“ einzusetzen.
Landshut
Die Batterie ist unerlässlich für die Elektromobilität. Dasselbe gilt für viele Komponenten, die im BMW Group Werk Landshut gefertigt werden. So steckt jede Menge Landshuter Innovationskraft im vollelektrischen BMW iX.
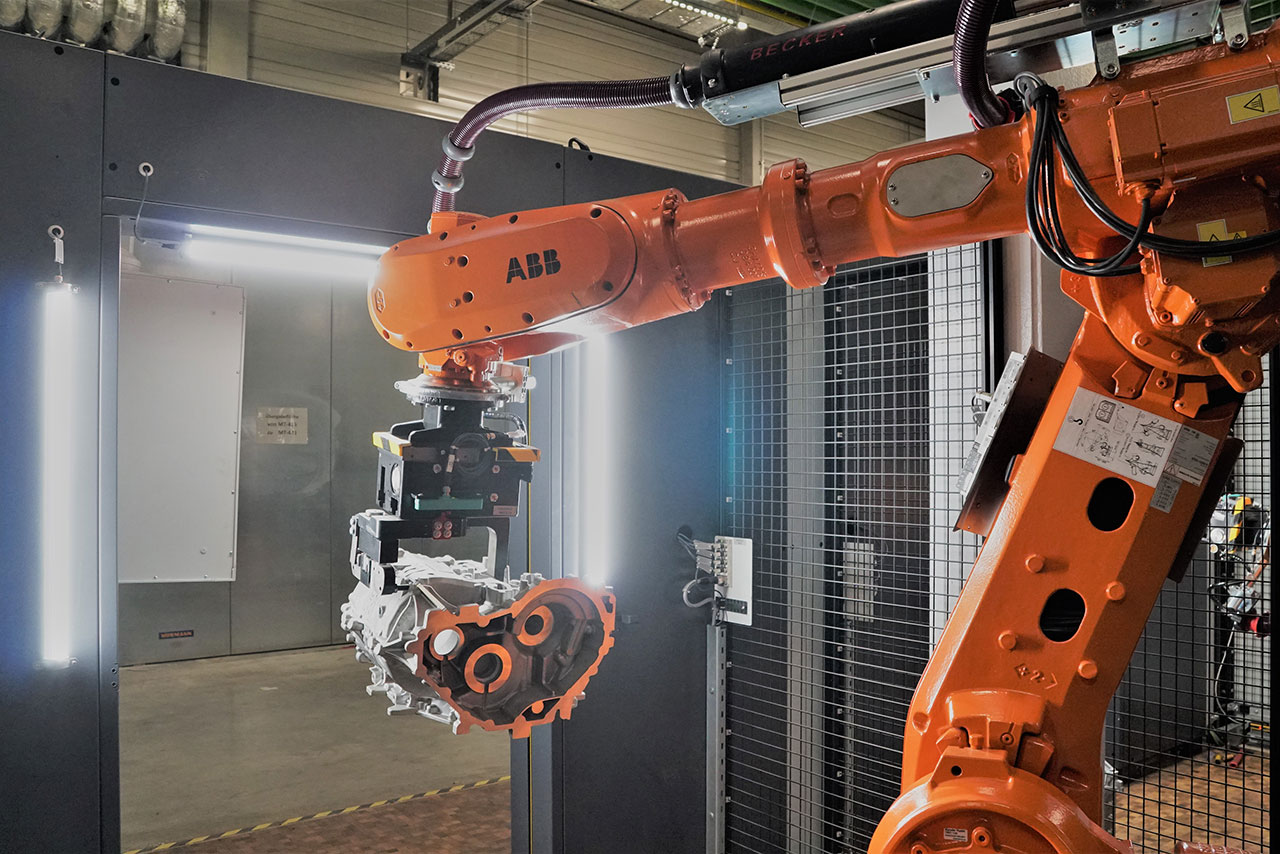
In der dortigen Leichtmetallgießerei entsteht das Gehäuse des hochintegrierten E-Antriebs der fünften Generation. Es besteht bis zu 50% aus recyceltem Aluminium und wird im speziell entwickelten, weltweit einzigartigen Injector-Casting-Gussverfahren (ICA) produziert. Übrigens kommt der E-Antrieb der fünften Generation komplett ohne seltene Erden aus.
Leipzig
Im Werk Leipzig spielen die Themen Batterie und Elektromobilität eine herausragende Rolle. Seit 2013 produziert das Werk Leipzig das erste vollelektrische Fahrzeug der BMW Group: den BMW i3. Im Oktober 2020 rollte bereits das 200.000ste Fahrzeug vom Band. Die über die Jahre gesammelte Kompetenz wird für zukünftige Modelle konsequent genutzt und weiter ausgebaut. Die BMW Speicherfarm auf dem Leipziger Werksgelände verwendet gebrauchte BMW i3 Batterien, zur Speicherung von Windenergie, wieder. Damit demonstriert die BMW Group, wie eine nachhaltige und profitable Zweitnutzung von Hochvoltbatterien aussehen kann.
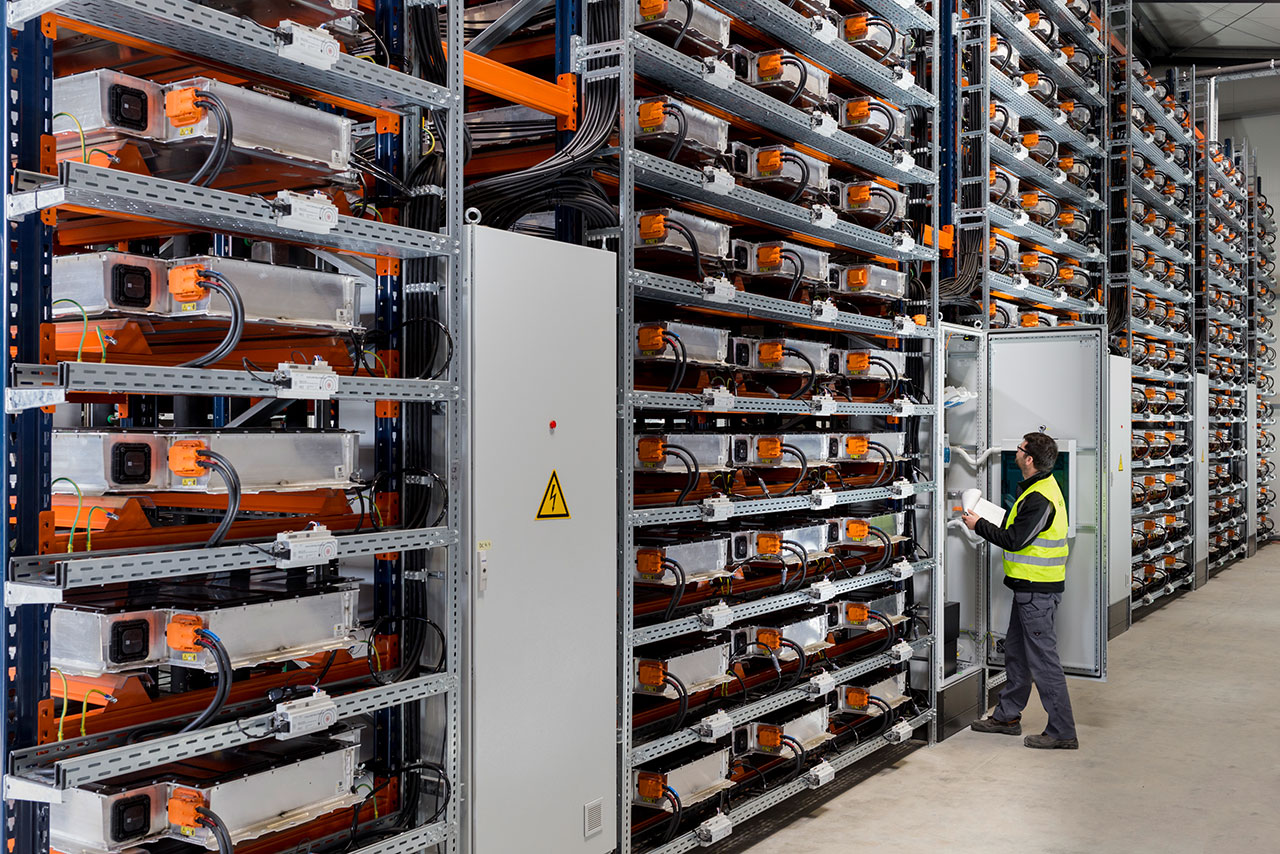

Mit der Inbetriebnahme der neuen Produktionslinie für Batteriemodule steht dem BMW Group Werk Leipzig ein weiterer Meilenstein bevor. Derzeit befindet sich die Batteriemodulproduktion kurz vor dem ersten Testlauf, im Mai soll die Serienfertigung beginnen.
München
„Power of Choice“ im BMW Group Werk München: Hier läuft die komplette BMW 3er Familie auf einem Band – in verschiedenen Antriebsvarianten. Egal ob Benziner, Diesel oder Plug-in-Hybrid: unsere Produktionsprozesse und unsere MitarbeiterInnen sind flexibel und für die Erfüllung aller Kundenwünsche ausgebildet.
Für den Umgang mit elektrischen Antriebskomponenten gibt es im Werk eine Vielzahl von Qualifizierungsmaßnahmen. Allein im vergangenen Jahr haben über 300 MitarbeiterInnen Schulungen dazu absolviert.
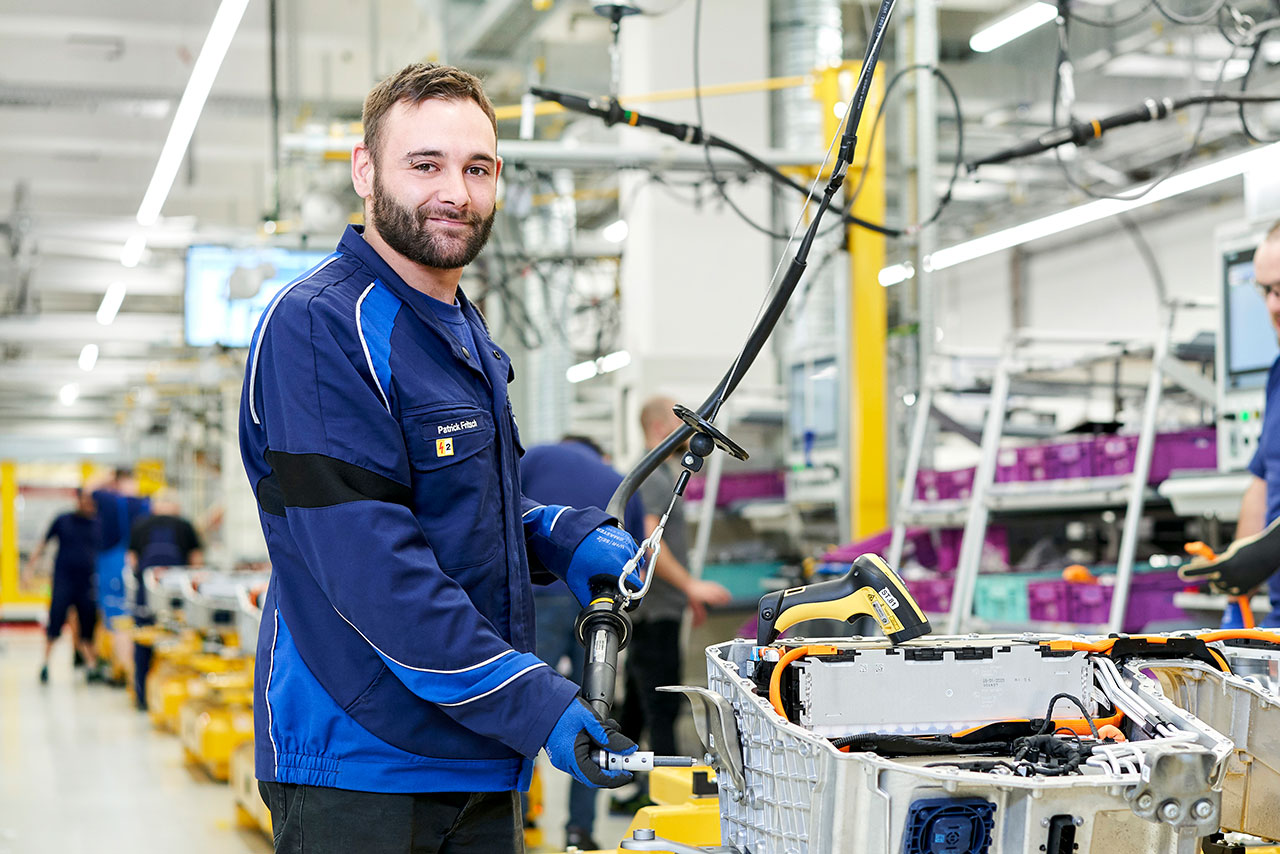
Dieses Jahr läuft das Qualifizierungsprogramm auf Hochtouren weiter, denn das Werk München bereitet sich auf den Anlauf des vollelektrischen BMW i4 vor. Eine weitere Antriebsvariante für noch mehr „Power of Choice“.
Oxford
Das erste vollelektrische Modell von MINI ist längst vollständig in den Produktionsprozess in Oxford integriert und läuft auf der gleichen Linie wie die Modelle mit Verbrennungsmotor. Aufgrund der hohen Flexibilität im Werk Oxford kann die Produktion des vollelektrischen MINI SE an die weltweite Nachfrage angepasst werden. Im Jahr 2020 wurden im Werk Oxford 17.580 MINI SE gebaut und weltweit verkauft. Dieses Jahr wird jeder dritte MINI 3-Türer elektrisch sein. Das spiegelt die steigende Kundennachfrage nach Elektrofahrzeugen wider.

Regensburg
Der „Tag der Batterie“ ist für das BMW Group Werk Regensburg dieses Jahr ein „Zukunftstag“: Hier entsteht derzeit die erste von mehreren Produktionsstraßen für Lackierung von Batteriezellen. Bereits im April 2021 geht die Anlage in Betrieb. Damit ist Regensburg offizieller Bestandteil des BMW Produktionsnetzwerks für E-Antriebskomponenten.
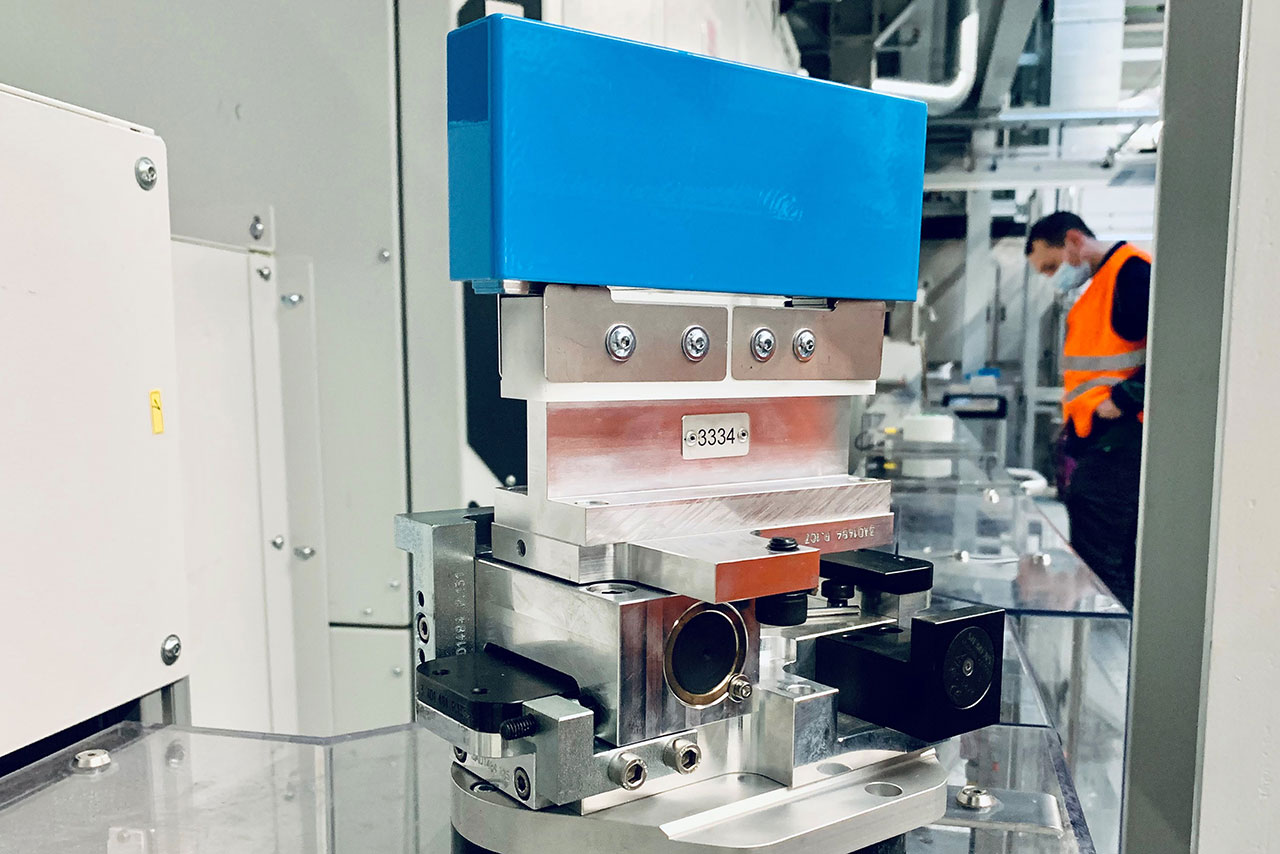
Bis Ende 2021 werden vier Lackierstraßen im Serienbetrieb laufen, zusätzlich geht im Jahr 2022 ein Montagezentrum für Hochvoltbatterien in Betrieb. So schafft die BMW Group in Regensburg mindestens 300 Arbeitsplätze mit Zukunft.
Momentan arbeiten rund 50 MitarbeiterInnen mit Hochdruck an Aufbau und Inbetriebnahme der Lackieranlagen. Ihren Weg durch die Produktionsanlage nehmen die Batteriezellen nicht auf einem schnöden Förderband, sondern auf einem vollflexiblen Multi-Carrier-System. Ein kleines Beispiel für die vielen Innovationen des neuen Regensburger Standorts, das zeigt: Hier zieht die Zukunft ein.
San Luis Potosí
Im Jahr 2020 startete das BMW Group Werk San Luis Potosí die Produktion seines ersten PHEV-Fahrzeugs, des BMW 330e. Dieser gehört zur neuen Hybrid Generation 4.0, die sich durch eine höhere Reichweite als seine Vorgänger auszeichnet.
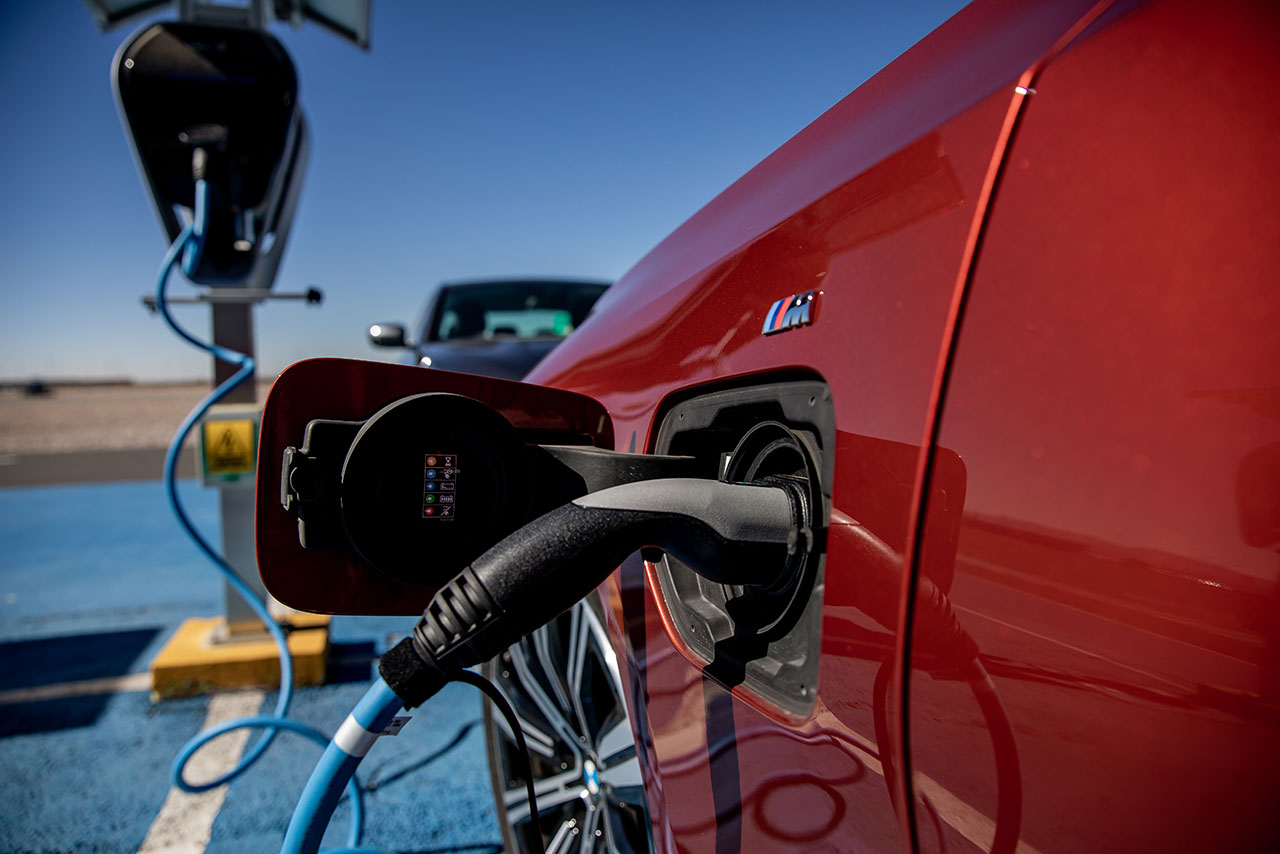
Das Antriebssystem des BMW 3er PHEV besteht aus einem 4-Zylinder-Benzinmotor mit TwinPower-Turbotechnologie, einem 8-Gang-Automatikgetriebe mit integrierter elektrischer Maschine. Der Hauptvorteil der im BMW 330e eingesetzten Hybridtechnologie ist gesteigerte Antriebsleistung im Vergleich zum konventionell angetriebenen BMW 3er – und das bei geringerem Kraftstoffverbrauch.
Der Elektroantrieb des BMW 330e ermöglicht vollelektrisches, emissionsfreies Fahren bei Geschwindigkeiten bis 140 km/h und einer maximalen elektrischen Reichweite von 60 Kilometern.
Shenyang
Die BMW Brilliance Powertrain Plant hat 2017 mit der Produktion von Hochvoltbatterien begonnen. Im Jahr 2020 folgte mit der Verdopplung der Produktionskapazitäten dank der Eröffnung der Batteriezentrum II bereits der nächste große Sprung. Dort wird die Hochvoltbatterie der fünften Generation als erstes im Produktionsnetzwerk der BMW Group hergestellt. Unter anderem wird diese Batteriegeneration im bandneuen BMW iX3 verbaut. Bis Mitte 2021 plant BBA die 100.000ste Hochvoltbatterie zu produzieren.
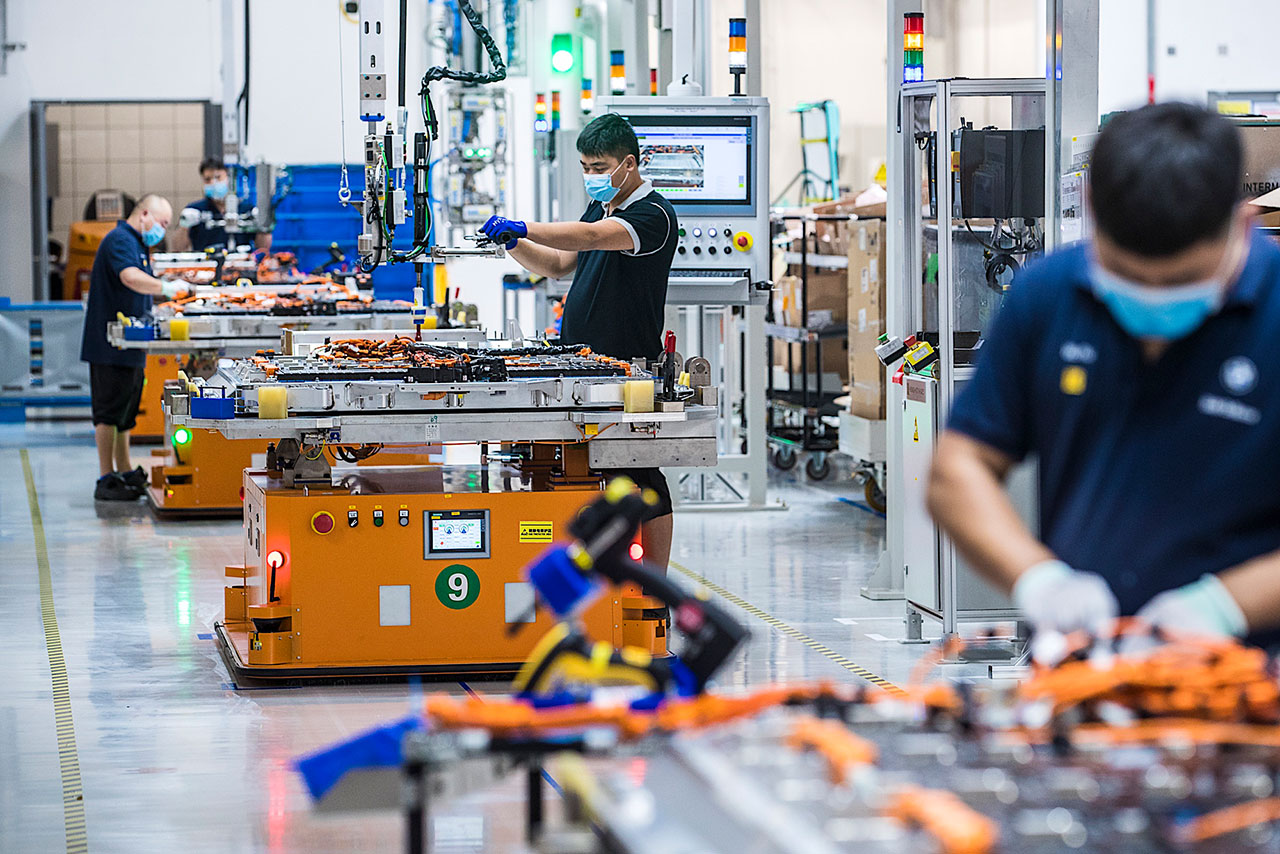
Spartanburg
Zwei Plug-in-Hybride aus der BMW Group Werk Spartanburg stellten 2020 neue Rekorde auf: Vom BMW X3 xDrive30e wurden fast 23.000 Stück produziert; vom BMW X5 xDrive45e über 24.000 Stück. Diese, zusammen über 47.000, elektrifizierten BMWs machten im vergangenen Jahr 13 Prozent der Gesamtproduktion des Werks Spartanburg aus.
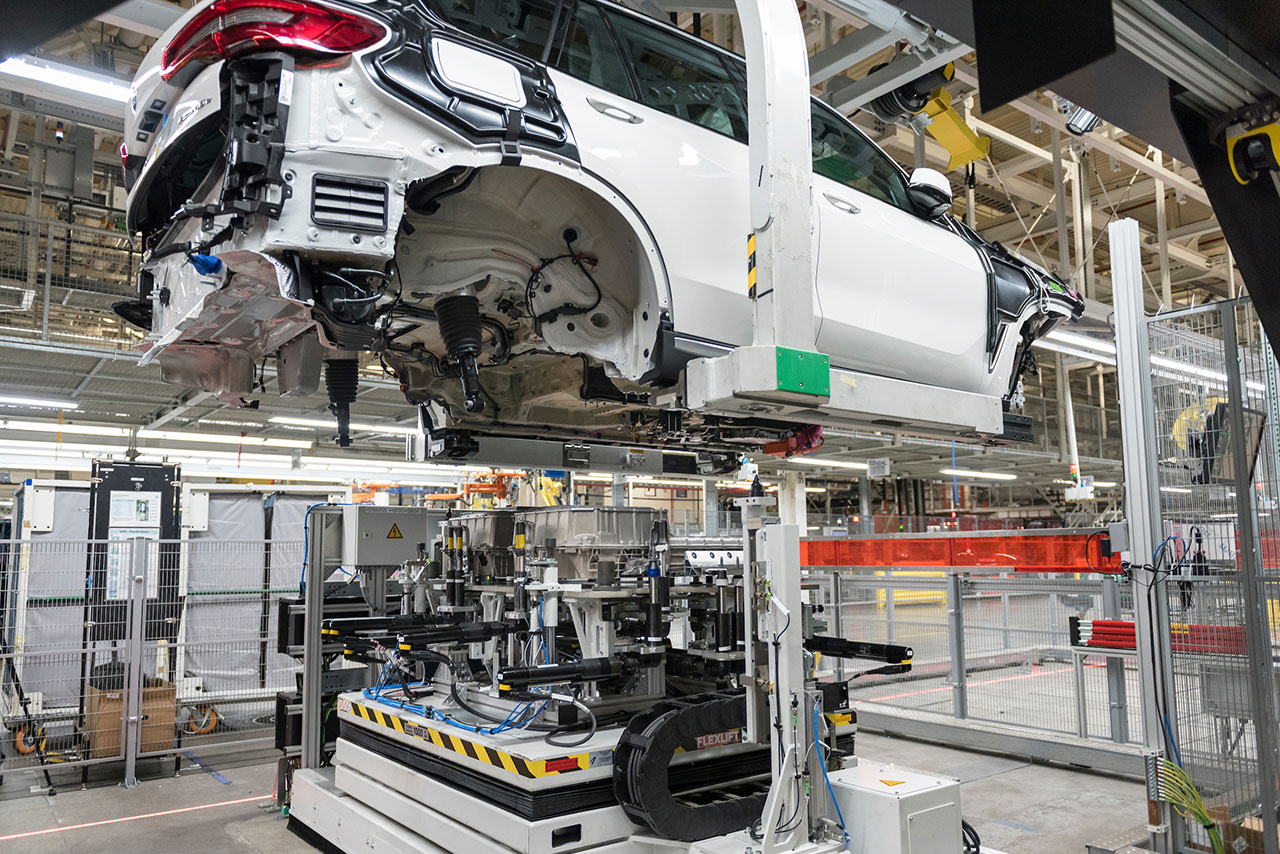
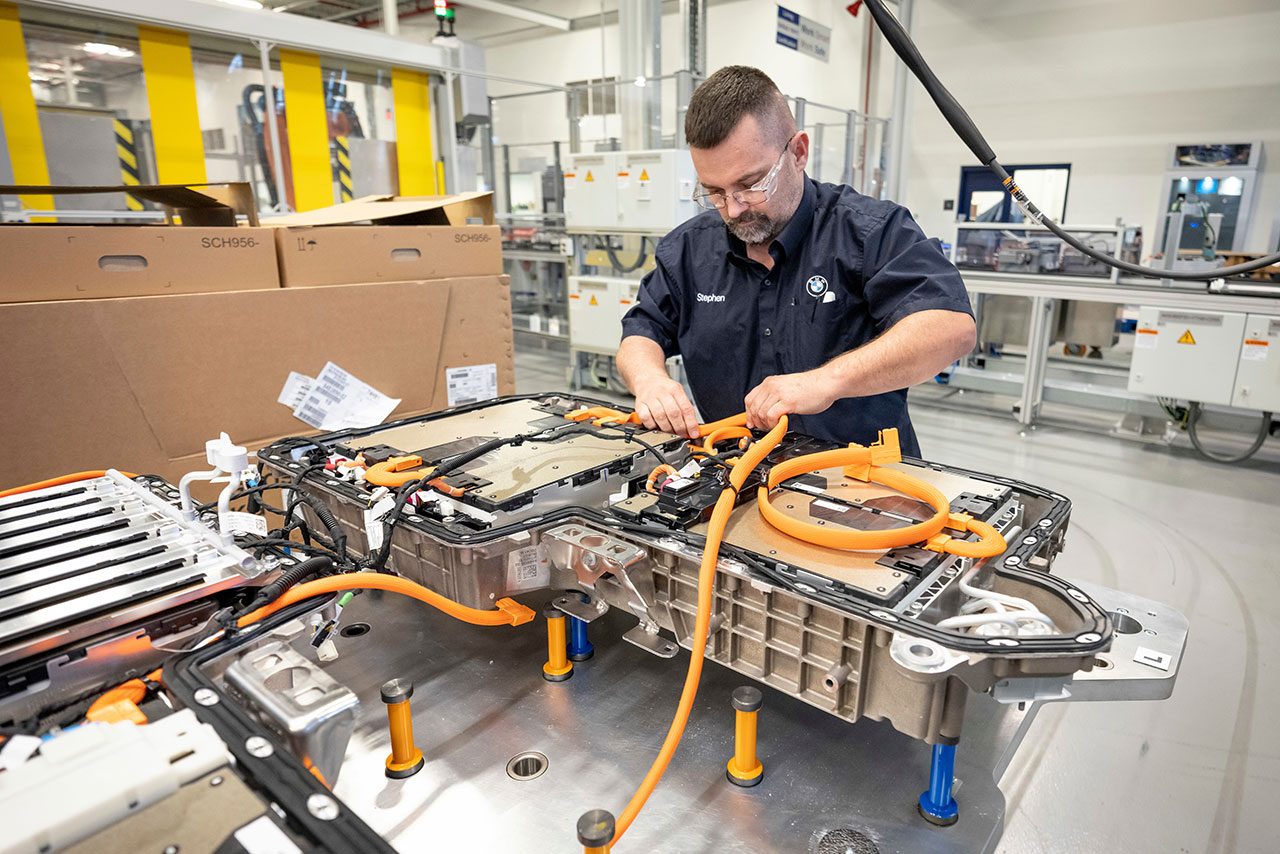
Möglich war das nur dank der 2019 erfolgten Erweiterung der Hochvoltbatterieproduktion. Bereits seit 2015 werden im Werk Hochvoltbatterien für elektrifizierte Fahrzeuge montiert. Damit ist die BMW Group auch in den USA ein Pionier der Elektromobilität.
Steyr
Im BMW Group Werk Steyr werden viele Komponenten entwickelt und produziert, die für Elektromobilität notwendig sind. Technologiekraft aus Steyr steckt unter anderem im BMW iX3, iX und i4. In der Motorenmontage des Werks werden rund ein Viertel aller Hybridmotoren für die Fahrzeuge der BMW Group gebaut. Seit letztem Jahr werden in der Mechanischen Fertigung in Steyr die Gehäuse des hochintegrierten E-Antriebs der fünften Generation gefertigt.
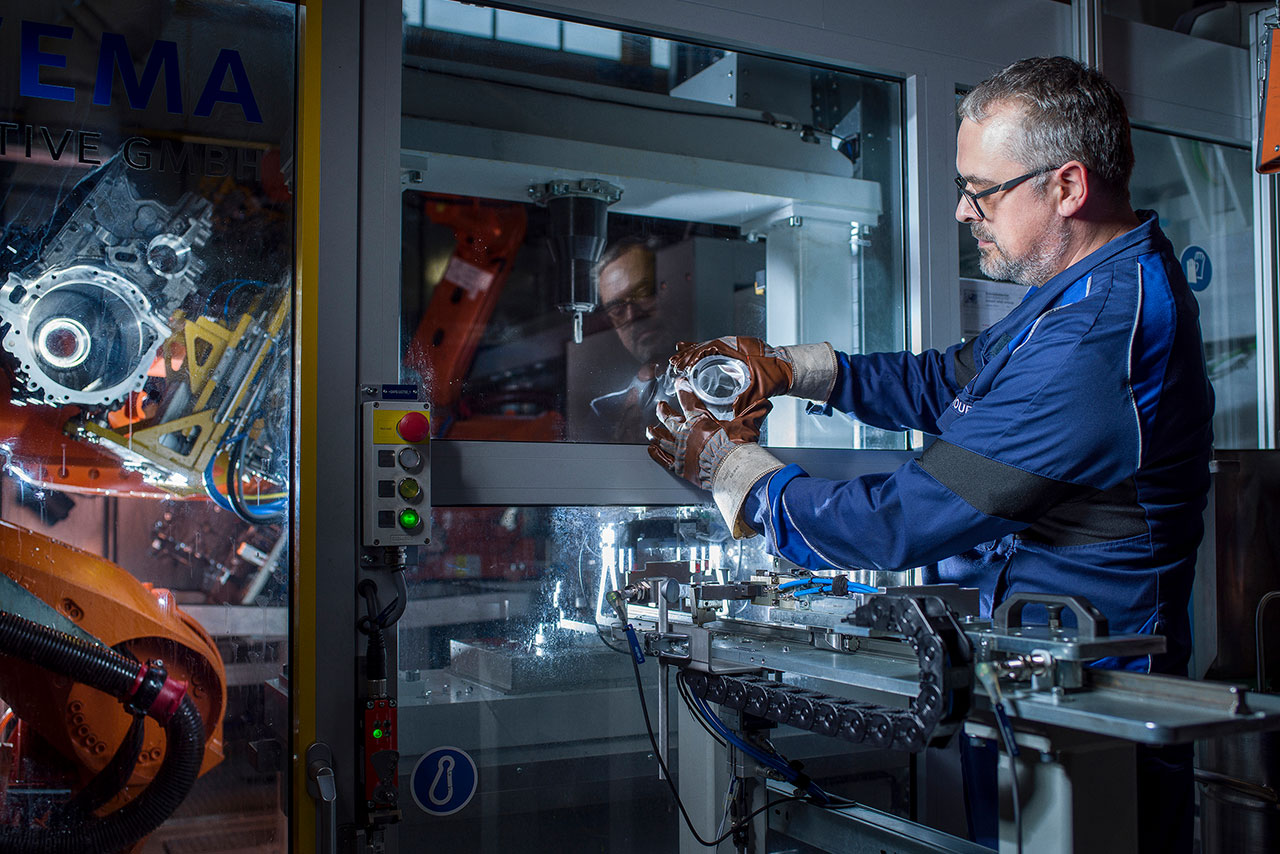
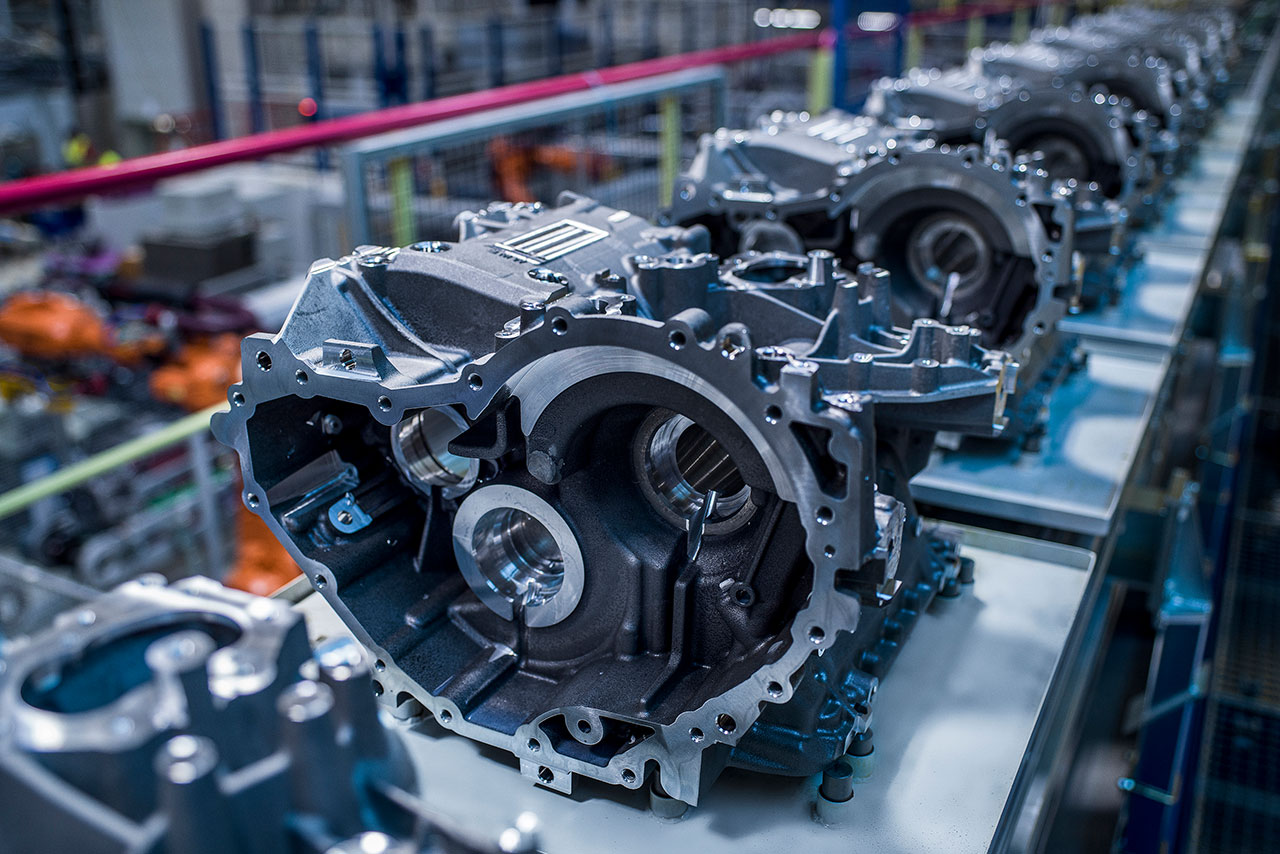
Die MitarbeiterInnen in der Entwicklung arbeiten sowohl an der Weiterentwicklung unserer sparsamen Verbrennungsmotoren als auch an alternativen Antrieben. Des Weiteren werden die Kühlkreisläufe für alle neuen, batterieelektrischen Fahrzeuge am Standort entwickelt und erprobt. Rund 10 Prozent der MitarbeiterInnen im Entwicklungszentrum beschäftigen sich bereits mit dem Thema Elektromobilität.