The World Economic Forum is a Swiss-based non-profit foundation, best known for its annual meeting in Davos. Once a year, leading international players from the worlds of business, politics and academia, as well as journalists, come together to discuss current global challenges. The World Economic Forum also follows – and recognises – developments in Industry 4.0. In this connection, BMW Group Plant Regensburg, representing the BMW Group production system as a whole, was honoured just a few days ago as a beacon of the fourth industrial revolution.
At the end of a selection process in which the World Economic Forum examined around 1,000 production facilities across different industries, the BMW Group plant in Regensburg, together with six other factories, emerged as a pioneer in digitalisation of industrial production. The plant is representative of the BMW Group’s production system as a whole.
Digital solutions are the only way the BMW Group can manage the growing complexity of production: 30 production and assembly locations in 14 countries, global daily production of around 10,000 vehicles with a large percentage of individually-configured orders, more than 40 BMW, MINI and Rolls-Royce model variants – all of these demand a high-performance production system. That the many digital solutions used in this production system are having a positive impact has now been confirmed by the World Economic Forum, which named the Regensburg plant a “Lighthouse of the Fourth Industrial Revolution”.
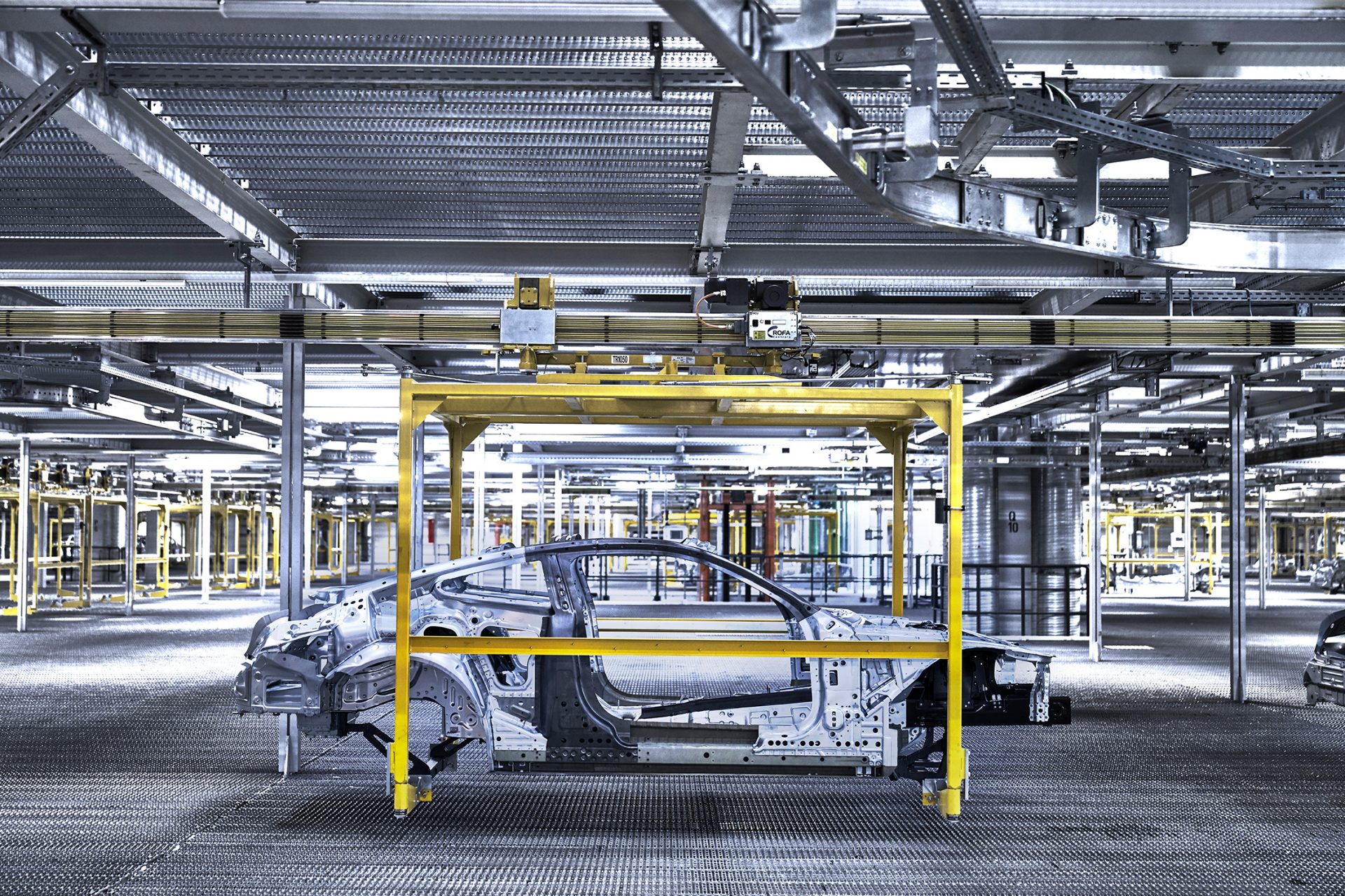
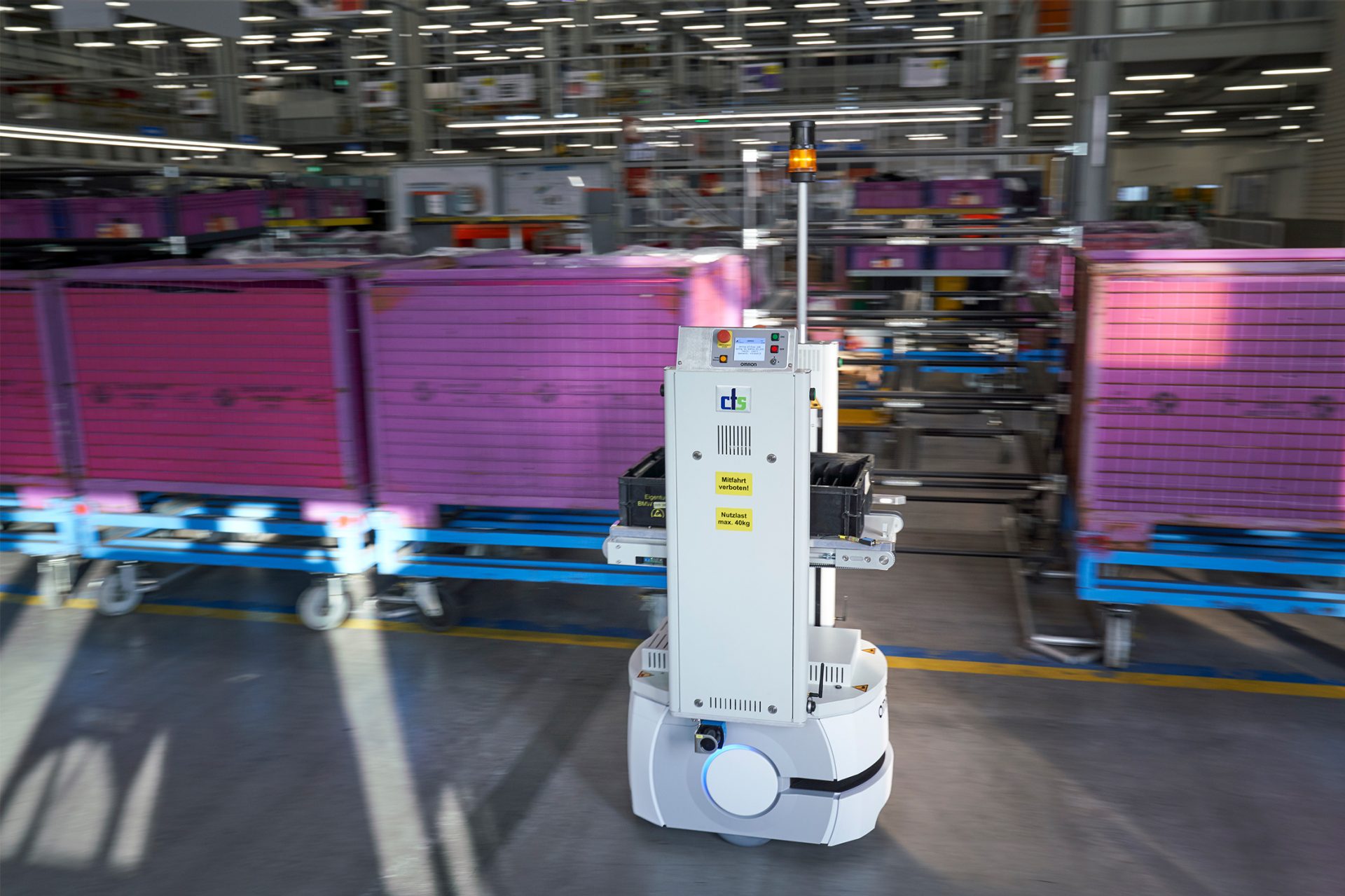
In choosing digital solutions, the BMW Group’s main focus is on innovative automation and assistance systems, additive manufacturing, smart data analytics and smart logistics. The BMW Group’s intranet-of-things platform also plays a crucial role in ensuring new digital applications are integrated smoothly into production IT.
In the digital transformation, it is especially important that the wide range of technological possibilities are integrated effectively into production. In the view of the World Economic Forum, the BMW Group’s approach and implementation of its innovative platform solution has helped the Regensburg plant integrate new applications 80% faster and significantly reduced logistic costs.
“The recognition of our Regensburg plant as a lighthouse motivates us to stick to our chosen path. Our clear strategic focus on the effectiveness of digital solutions and structural decisions, like the overarching BMW IoT platform, are definite success factors. We rely, in particular, on our staff’s creative energy and integration skills,” according to Dr. Christian Patron, head of Innovation, Digitalisation and Data Analytics.
The platform provides employees with a digital toolbox of resources they can combine to create their own “plug and play” solutions. As such, human beings remain at the heart of value creation, while gaining more room for creativity.
Manfred Erlacher, head of BMW Group Plant Regensburg, therefore also views employees as the central element in successful implementation of new digital solutions: “Our people, their creativity and their experience are the main drivers for effective innovations and the continued development of the production system. Because, once a smart solution has been successfully implemented, it soon catches on in other production areas and at other locations.”
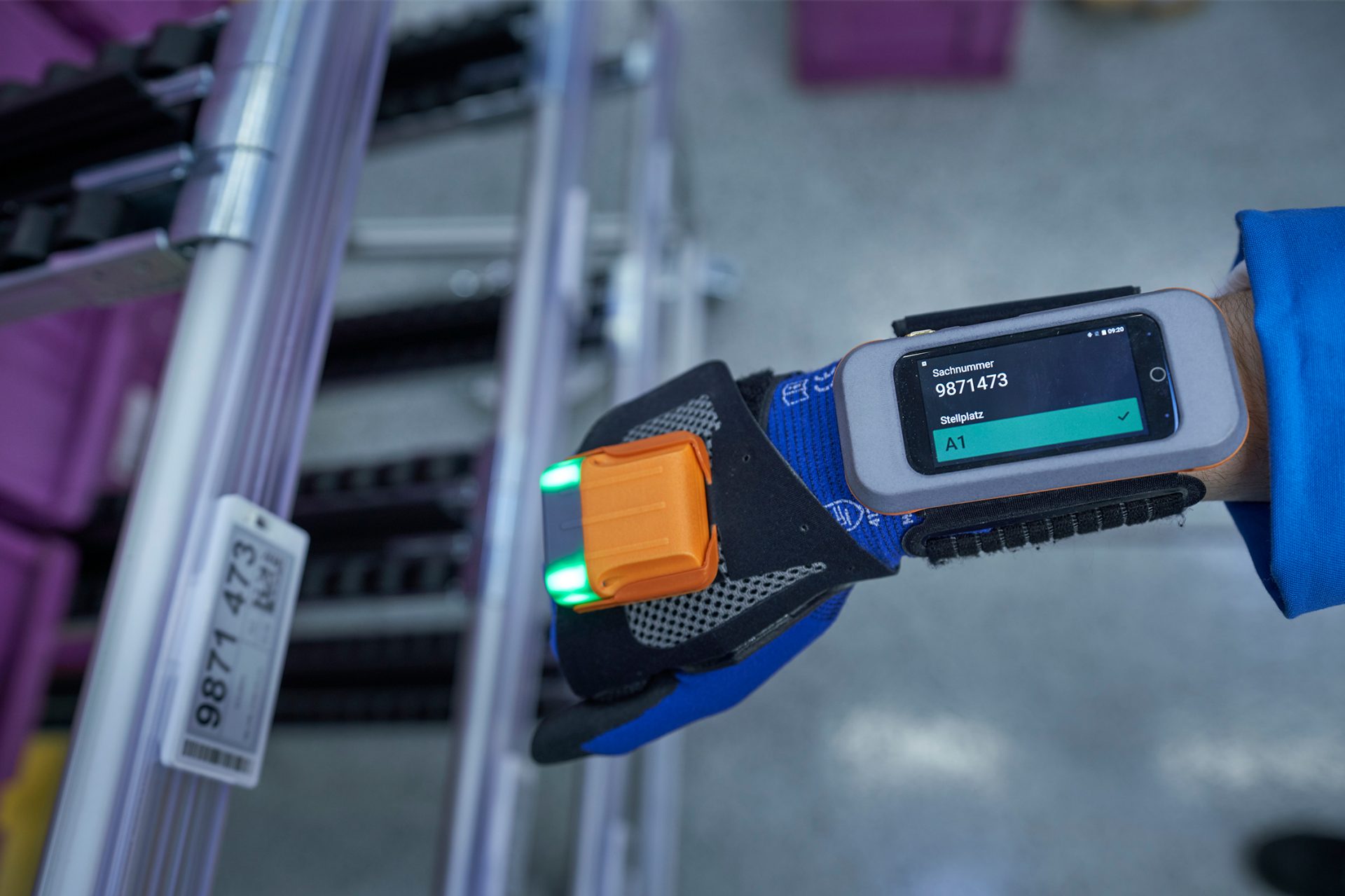
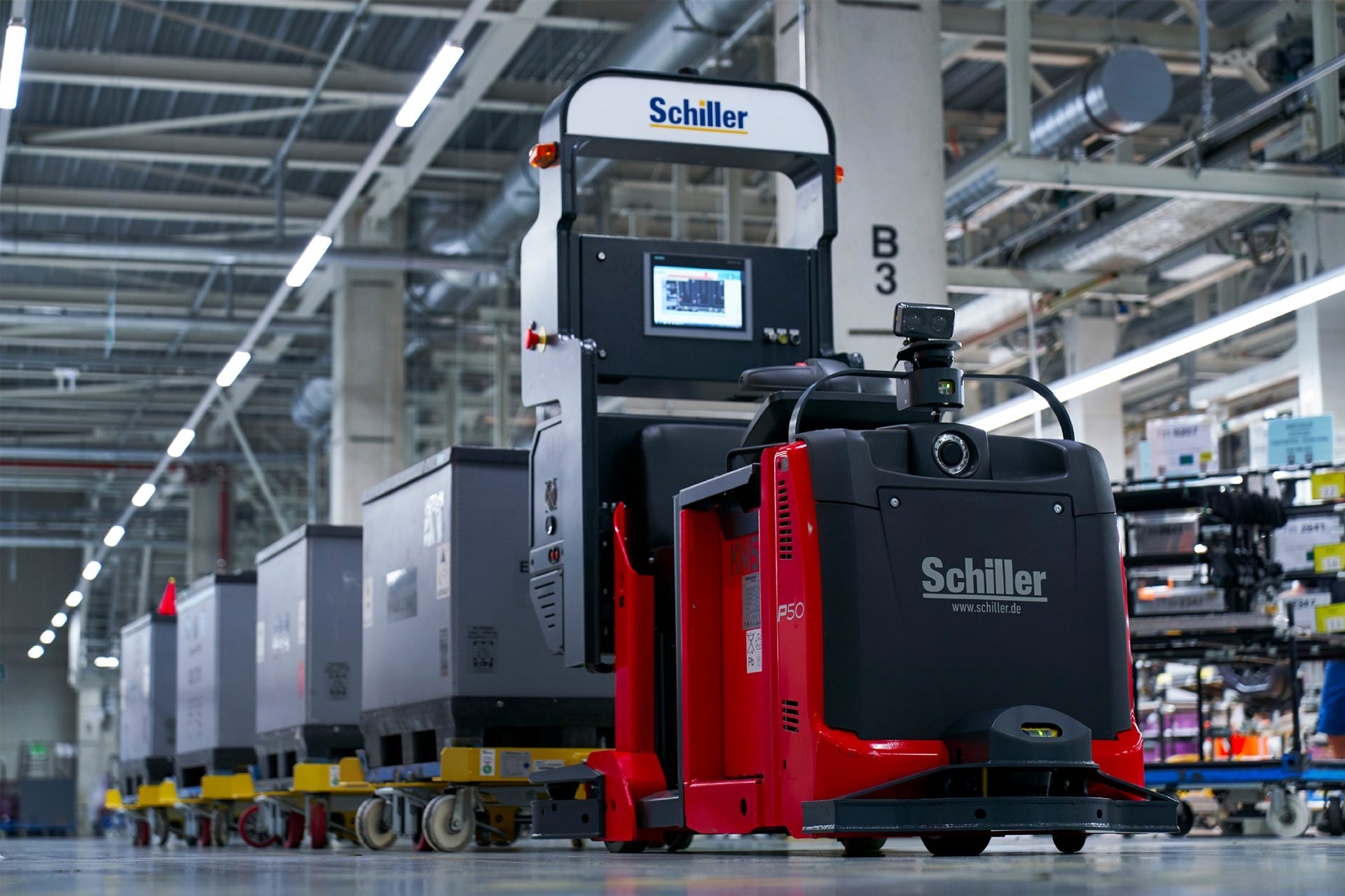
The BMW Group production system is characterised by this combination of digital developments with clear employee involvement in the digitalisation process – making it more agile and future-proof and essentially ensuring that the Regensburg plant can now consider itself one of the “factories of the future”.