Besides setting milestones with the production of MINIs, the Oxford MINI plant is also a leader in sustainability.
Oxford is far more than just home to the oldest university in the anglophone world. Around 150,000 inhabitants live and work in this renowned city – in part made famous thanks to the filming of Harry Potter – in a wide variety of sectors including education, publishing, technology and science and the automotive industry. The city is also known for its MINI factory, which has belonged to the BMW Group since 1994 and is one of Europe’s oldest car manufacturing plants.
The MINI plant in Oxford is more than just the birthplace and heart of MINI production. Just like the hundreds of vehicles produced here each day, exported to more than 110 countries around the world, the plant is unique – especially when it comes to sustainability. This is not just down to the much-loved vehicle which will enter the market as the zero-emissions MINI Electric next year. The Oxford plant follows a 360-degree sustainability strategy, encompassing a solar roof, heat regeneration, lighting systems, environmentally friendly production, the use of rainwater, setting up bird boxes and ideas for raising awareness for ways to enhance sustainability among employees.
“One of Great Britain’s largest solar energy facilities can be found on the roof of our plant,” says Manuel Sattig, Head of Communications UK Production. More than 11,000 solar panels covering an area equivalent to five football fields supply production halls and the administration department with more than three megawatts of renewable energy.
The Oxford plant has set itself ambitious environment goals – and the results are clear for all to see. Last year, employees managed to reduce power consumption by 41 percent. The picture is similar for water consumption, which was lowered by 40 percent, and the reduction of waste (down 90 percent). There was also a 28-percent drop in solvent emissions. “Using LED light bulbs, alongside other measures, has helped us to achieve these great results. We have already replaced more than 18,000 bulbs. We even have the means to programme over 4,000 light bulbs to suit requirements,” says Sattig.
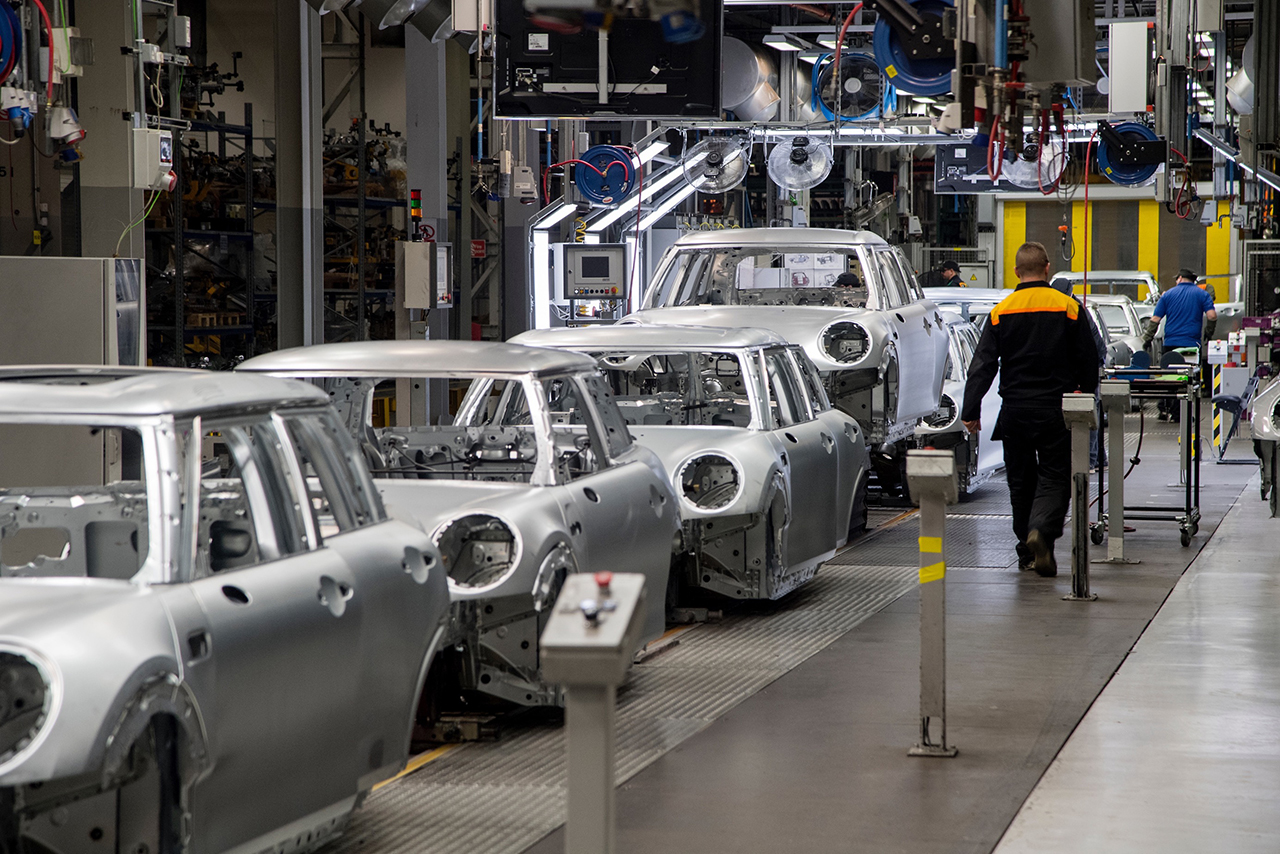
The water savings were largely down to extensive modernisation of the paint shop: “We need demineralised water for production. Thanks to the new ion exchange system, we can now produce high-quality demineralised water, which is free from chemicals and significantly improves the efficiency of the paint shop. This saves us 11,000 litres of water per hour,” says Darren Green, Process Engineer at the Oxford plant.
The paint shop has another unique feature up its sleeve. The Oxford plant was the first in the BMW Group to launch the Integrated Paint Process (IPP), which is now also used in the Spartanburg (USA), San Luis Potosi (Mexico) and Tiexi (China) plants. This process makes it possible to circulate air in the booths, dramatically reducing energy consumption. State-of-the-art technology is also used to regenerate heat throughout the plant so that any heat produced can be fed back into the system.
There are also smaller measures in place that increase the sustainability of the plant, which employs about 4,500 people: Each employee receives a reusable coffee mug, rainwater is collected to be used in the toilets and a network of incubators around the plant offers birds a safe place to lay eggs for their offspring.
“We also try to get employees and the area surrounding the plant involved in our sustainability efforts,” says Sattig. For instance, improvement suggestions are collected and stored in an ideas database, which is made available to other BMW plants around the world, as part of a special idea management scheme. Last year, information booths were set up on Family Day so that people could find out more about enhancing energy efficiency and the importance of biodiversity.