Large quantities of water are consumed in the production of vehicles. The BMW Group’s global production network is making a significant contribution to reducing the consumption of this precious resource through the use of innovative technologies.
Water is fundamental for life on our planet. However, this vital resource is becoming increasingly scarce worldwide. This is why the careful use of water has been a vital consideration for the BMW Group for decades.
Careful use of water is a matter of course for the BMW Group. Reducing water use and waste-water generation throughout the production network is one of its most important goals in its drive towards sustainability. That is why the company continuously invests in water-saving processes and innovative technologies.
Continuous reduction of water consumption
The BMW Group has been able to reduce its water consumption worldwide by over 30 per cent compared to its 2006 figures. The total water consumption per vehicle produced in 2020 was 2.25 m³ (source: BMW Group Report 2020).
New technologies and continuous improvement measures all contribute to this.
Measures to help save water.
Water is needed in many processes in automotive production. Consequently, the BMW Group constantly strives to establish innovative technologies and more efficient processes in production and, in doing so, steadily reduce water consumption.
Processes that have been piloted and proved successful at individual locations are continuously refined, and the expertise gained in the process is then rolled out to our worldwide network of plants.
Water reused thanks to recirculation.
The paint shop is a major consumer of water, but a particularly large proportion of water gets recirculated here too. As a result, this valuable resource gets reused many times: water that has already been used and contaminated is purified and recycled, enabling it to be used several times.
Large amounts of water are also consumed in the pre-treatment and multiple cleaning of the body shell before the painting process. The BMW Group relies on what are known as cascade systems in this process. These allow contaminated process water to be intelligently reused several times in a process that runs in harmony with the bodywork process. In addition, some of the waste water that has passed through the cascades can also be recycled and reused.
Thanks to recirculation, a large proportion of the water used is treated and reused – for example, in the BMW Group’s new car wash facilities. The circulation system also plays a significant role in the “shower chamber”, where the vehicles are sprayed with water from all sides once again to test for leaks before they are completed. This saves on water consumption. Several hundred litres of water are used on a single leak test.
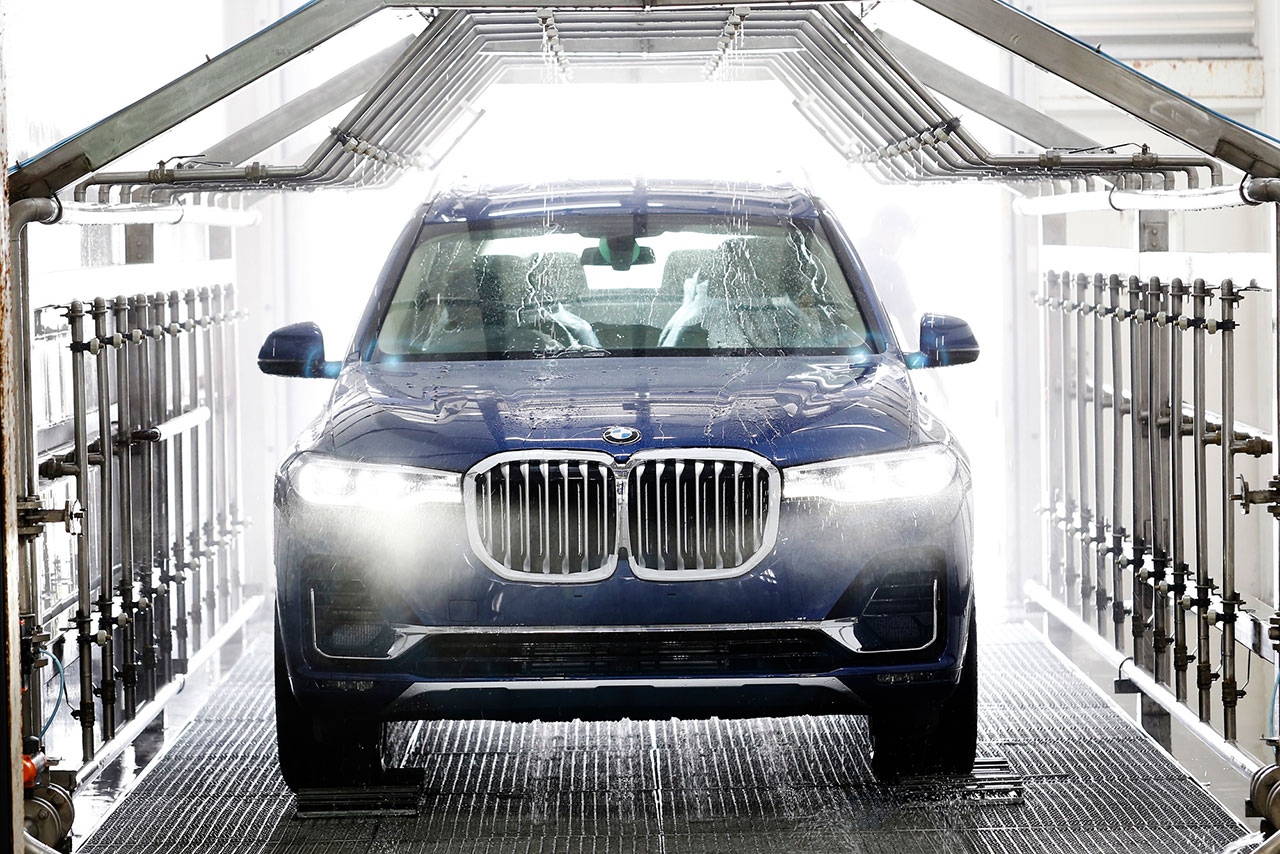
Less water thanks to dry separation.
The principle of dry separation is another initiative for saving water in the painting process. The air contaminated with paint particles is cleaned using a special recirculation system and cardboard filters instead of “washing out” the excess paint particles with water.
Less evaporation through recooling.
Water is also needed in automotive manufacturing to cool machines down and humidify air in air-conditioning systems. A lot of water evaporates during hot weather in particular.
The loss of evaporated water is reduced by using closed instead of open cooling circuits. This is why the BMW Group is increasingly using hybrid coolers when modernising recooling systems.
Treatment of rainwater.
The company pays particular attention to carefully using this raw material in regions where there is a shortage of water, respecting the natural conditions of the respective locations. For example, about six million litres of rainwater are collected during the monsoon season at the plant in Chennai, India, providing up to 50 per cent of the plant’s water needs.
Sustainable use of this precious resource is also an important concern for the BMW Group outside its production facilities as well. The company is committed to the highest environmental and social standards in its operations and throughout its supply chain, and engages in a number of environmentally and socially sustainable projects and initiatives. The BMW India Foundation commissioned a rainwater harvesting system in the Nuh district in the northern Indian state of Haryana in September 2020 as part of the “water for future” project.
This project was carried out in cooperation with the Indian non-governmental organisation SM Sehgal Foundation. A special biosand filtration technology was installed for this in the water tanks of five schools in the region. This technology removes microbes and other impurities from the collected rainwater to produce clean drinking water. More than 2,200 students and teachers from these schools have since had access to this clean water.
These measures and projects are just a few examples of how the BMW Group has firmly anchored environmental and social sustainability in its strategy across the entire value chain. In doing so, the company consistently pursues the goal of CO2-neutral and sustainable production and the conservation of natural resources.