The BMW iFACTORY focuses on LEAN. GREEN. DIGITAL. new standards in automotive production. LEAN stands for greater agility, leaner processes and forward-looking structures.
It is a significant turning point in automobile production: flexibility, sustainability and digitalisation are the cornerstones of a new, innovative production philosophy. If the increasing customer demand for innovative and individually built vehicles, even in the course of the transformation to e-mobility, is to be met, processes need to be completely redefined. The BMW Group has developed a visionary master plan for this: the BMW iFACTORY. “Automotive manufacturing of the future requires a new, holistic way of thinking,” says Milan Nedeljković, Member of the Board of Management for Production at BMW AG. “With our BMW iFACTORY, we are leading the way and setting new standards in flexibility, efficiency, sustainability and digitalisation.”
The BMW iFACTORY represents the strategic goal of a worldwide production network, pursuing a global, integrative approach that is being implemented in all plants – from the 100-year-old main plant in Munich to the new plant in Debrecen, Hungary. The BMW Group is concentrating on three key strands: LEAN. GREEN. DIGITAL. LEAN stands for efficient, precise and flexible. GREEN encompasses resource-optimised and circular production. DIGITAL is the effective use of artificial intelligence, data science and virtualisation.
LEAN: More integration-capable and variable.
The demands on production at the BMW Group are clear: it must be efficient, precise and flexible: LEAN. All processes in the BMW iFACTORY are made more integrable and variable. The best example of this transformation is the Neue Klasse, which will be produced from 2025 and is based on a completely new vehicle architecture. Its clear focus on all-electric drives creates the environment needed for efficient production of future vehicle generations in line with the profitability and quality targets of the BMW Group.
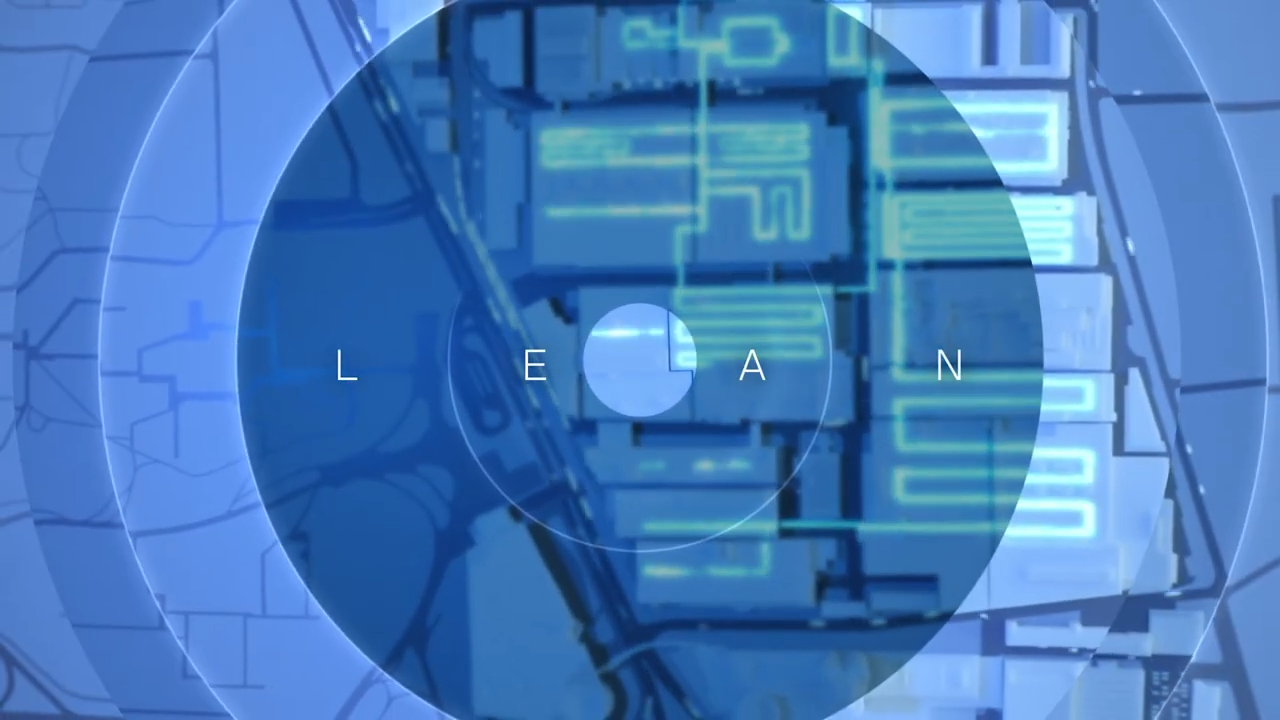
The resulting flexibility gives the BMW Group its key competitive advantage in production. LEAN is the driving force of the production system. All production processes interlock even more efficiently and are combined more intelligently than ever before. Quality, costs and time are the criteria for optimisation.
At the same time, BMW iFACTORY’s production is so flexible that it can integrate new models into existing structures. For example, the BMW Group already produces all drive types on a single production line in Munich, Dingolfing and Regensburg.
Even more precise, more transparent and faster.
The BMW iFACTORY also exploits advances in digitalisation. The production system will become even more precise, transparent and faster in the future thanks to meaningful real-time data on the entire production process. This enables production to spontaneously cushion supply bottlenecks and react extremely flexibly to fluctuations on demand. What this means for our customers is that they can still change the configuration of the vehicle they have ordered up to six days before production starts.
There is one particularly important factor for stable and reliable processes in the plants and to create premium quality products: the employees – after all, they are the ones who drive the BMW iFACTORY forward. They have to think flexibly to implement LEAN, constantly face new challenges and continuously learn innovative technologies and processes.
The BMW Group helps equip them for this by training and coaching its employees at all levels in their individual development. The end result is the most modern and “leanest” automobile production facility in the world – the BMW iFACTORY. LEAN. GREEN. DIGITAL.