Production Network 2 of the
BMW Group.
The heart of the “Bayerische Motoren Werke” is located in Bavaria. Alongside the parent plant in Munich, the state capital, BMW Group also operates high-volume full plants in Dingolfing and Regensburg. As more BMWs roll off the line at the BMW Group Plant Leipzig in Germany, they are now accompanied by MINI vehicles. There are also major international locations, such as Spartanburg in the USA, Rosslyn in South Africa, Shenyang in China, and San Luis de Potosí in Mexico, while the BMW Group Plant Debrecen is currently under construction in Hungary. In Great Britain, the BMW Group manufactures MINI vehicles in Oxford and Rolls-Royce cars in Goodwood. These internationally renowned production facilities together form Production Network 1.
However, the BMW Group also operates Production Network 2 - and has done since 1957! What started with the production of the BMW Isetta in England now encompasses seven locations in Asia, North Africa, and South America. All of these are in markets with high rates of duty on imported vehicles. Cars manufactured in those markets are not subject to these customs regulations.
First production of high-voltage batteries in PNW2 in Thailand.
As part of PNW2, the BMW Group operates three of its own plants in Brazil (since 2014), India (2007) and Thailand (2000), where the first independent production of high-voltage batteries for electrified cars within PNW2 was recently launched. PNW2 also manufactures cars in four plants run in collaboration with local partners located in Indonesia (started in 1976), Malaysia (1979), Vietnam (restarted in 2021) and Egypt (restarted in 2023).
“The BMW Group Production Network 2 is not only fundamental to gaining a foothold in emerging markets with potential for growth, but also a profitable component of our business area. It is fascinating to see what innovative assembly solutions are used on one production line in manufacturing our products, from MINI to the BMW X7. That is a prime example of the high degree of versatility of our whole production system,” said Michael Nikolaides, Senior Vice President Production Network.
High versatility the key to success.
When it comes to local production depth (only a paint shop on site in certain places) or the number of local supply parts (local content), different legal regulations apply in the countries in which PNW2 manufactures vehicles. Furthermore, versatility is a key factor in the success of PNW2 in two regards. On the one hand, the system allows fast access to new markets and, should it be made necessary by changes to market demands, easy withdrawal. On the other hand, production itself is extremely versatile at the individual sites. For example, up to 14 different models - from MINI and the BMW 1 Series to a BMW X7 - are manufactured on the same production line and up to 30 new vehicles can be introduced in a single year. This is all possible thanks to simple, creative solutions, a low degree of automation and individually different cycle times - without affecting quality. All vehicles meet the same delivery standard as in the large full plants in PNW1, of which Rosslyn in South Africa and Shenyang in China stem from PNW2, incidentally. In 2023, the BMW Group produced roughly 50,000 vehicles plus BMW motorcycles in the PNW2 plants - all with almost exclusively local employees and management.
Close collaboration with Production Network 1.
Figures like these are only possible in close collaboration with PNW1, for example in production planning, technical integration and component manufacture. These parts are prepared for distribution by six packing operations – three in Germany and one each in China, Mexico and the USA. That is where the relevant components are put together in ready-to-assemble kits, based on the IKEA model, and distributed to the PNW2 plants.
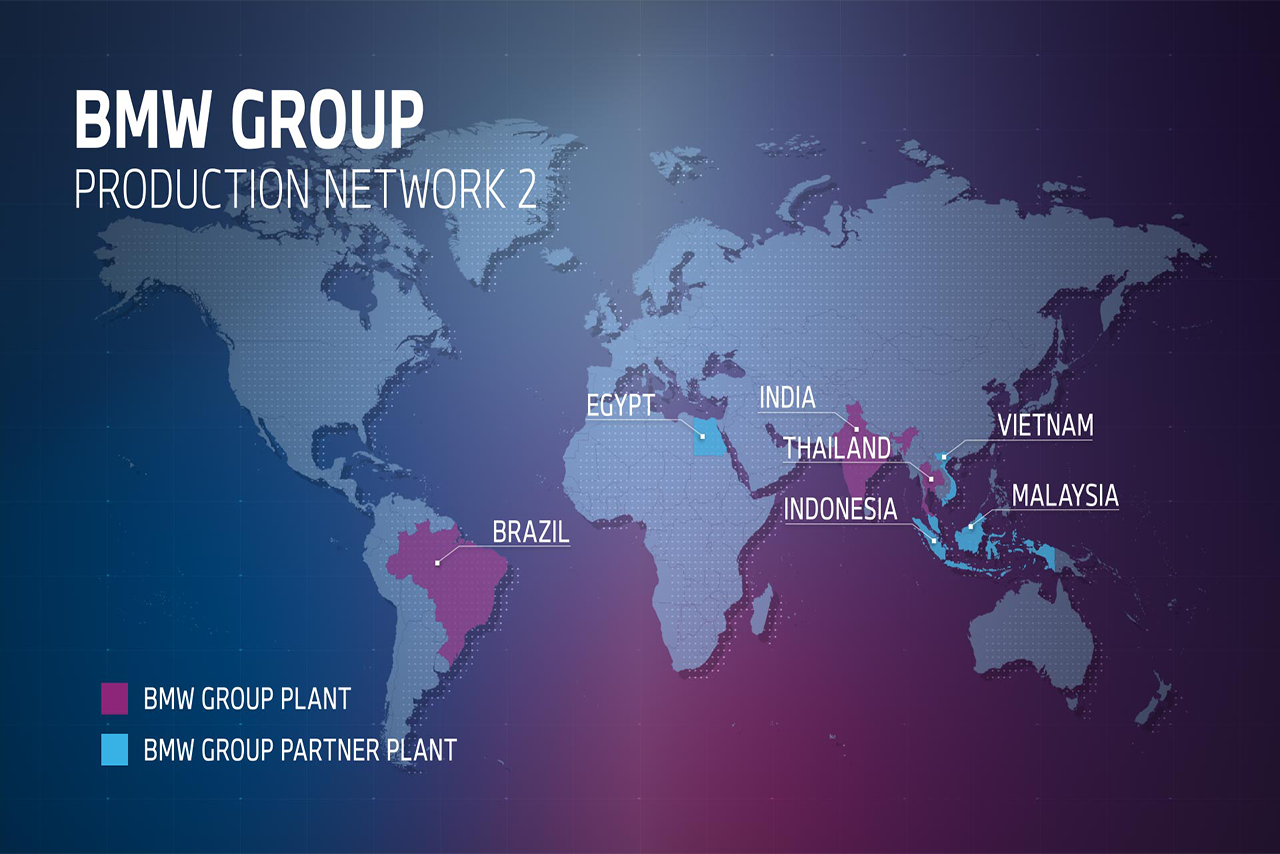