Artificial Intelligence-based in-house technologies, such as Car2X and AIQX, transform BMW vehicles into connected players – right from the production process.
The vehicle itself a communicative and intelligent participant in production? The BMW iFACTORY and Artificial Intelligence (AI) make it possible. The BMW Group is making vehicle construction faster, more reliable and more efficient with its own AI innovations such as Car2X and AIQX. But not only this; it is also turning the models in production into communicative helpers that, for example, provide constant information about their assembly status or independently identify and report assembly errors. At the same time, visual and acoustic quality assurance using Artificial Intelligence in the BMW iFACTORY is already raising the bar on standards. The BMW Group is optimising its production thanks to this progressive strategy, using state-of-the-art AI-based technology and consistently driving forward its digital transformation.
The use and further development of digital technologies such as Artificial Intelligence in vehicle construction is an integral part of the BMW iFACTORY with its three pillars of LEAN. GREEN. DIGITAL. The master plan of the BMW Group for the production of tomorrow relies on our in-house-developed cloud-based AI innovations – at all BMW Group plants worldwide – to automate and optimise processes.
Car2X: intelligent production driven by Artificial Intelligence
One of the most exciting AI technologies from the BMW Group is Car2X. Car2X is a cloud-based feature enabling real-time communication and interaction between the vehicle and the BMW production system during the production process. Car2X “transforms” every BMW on the production line into an active and connected participant in our industrial IoT (Internet of Things) ecosystem that self-analyses, interacts in real time with employees in the plant and automatically shares and documents relevant messages. Autonomous communication is ensured during production by means of data streams that allow the vehicle to actively interact with countless production resources and the cloud, wherever they are physically located.
Practical examples for Car2X in use
Car2X technology from the BMW Group comprises several specific use cases. A common factor in all these cases, however, is that the vehicle under construction communicates in real time – thus playing an active role in its own production:
Plug connections
The vehicle compares its intended and actual assembly status. The Artificial Intelligence identifies any variances, such as faulty plug connections, and reports them to the system. This means that assembly errors can be rectified instantaneously, resulting in significantly less rework.
Object recognition
The vehicle is able to analyse its surroundings. It uses its built-in cameras to scan the car ahead of it on the production line. If, for example, the warning triangle is not fitted, the AIQX optical quality control system helps the vehicle identify this and it immediately reports discrepancies to employees and production systems.
Parking space recognition
The vehicle can be contacted at any time, is networked and has its entire value creation process in view. It instructs employees on the assembly line with specific assembly instructions and navigates them in real time to their planned parking space on the outdoor areas.
Visual and acoustic quality inspection by AIQX
Alongside Car2X, the custom-developed IT platform AIQX – short for Artificial Intelligence Quality Next – is a core component of the BMW iFACTORY. AIQX uses sensor technology and AI to automate quality processes by establishing camera systems and sensors in the conveyor belt process. Algorithms and AI analyse the data recorded by these in real time and send employees on the production line immediate feedback via smart devices. AIQX can therefore be used to determine variants, check completeness and detect anomalies in the assembly process.
But that’s not the full extent of what AI at the BMW Group can do: Production not only sees quality defects better, it also hears them thanks to Artificial Intelligence. The BMW Group Plant Dingolfing uses a sub-area of AIQX, Acoustic Analytics. This is an AI model that automatically carries out an audio-based quality check. Microphones on the car seats record all driving noises and uses AI to analyse and classify them. The AI model uses its extensive previous training to recognise whether there is any background noise. This is the final check before the vehicle is handed over to the customer. The advantages of audio testing using AI are obvious: the automated process is faster, more efficient and eliminates subjective perception of the sounds.
The bottom line for the customers of the BMW Group: more enjoyment and safety with every BMW model. The BMW Group is constantly revolutionising the quality process in vehicle construction thanks to in-house AI developments such as Car2X and AIQX.
Ongoing further development in the digital sector
The BMW Group sees the use and further development of Artificial Intelligence as critical elements in vehicle production. The company is therefore constantly expanding its knowledge in the field of AI, training employees and continuously developing new, digital, and intelligent processes. Innovations such as Car2X and AIQX are already making crucial contributions to the successful expansion of the BMW iFACTORY and the digital transformation of the BMW Group.
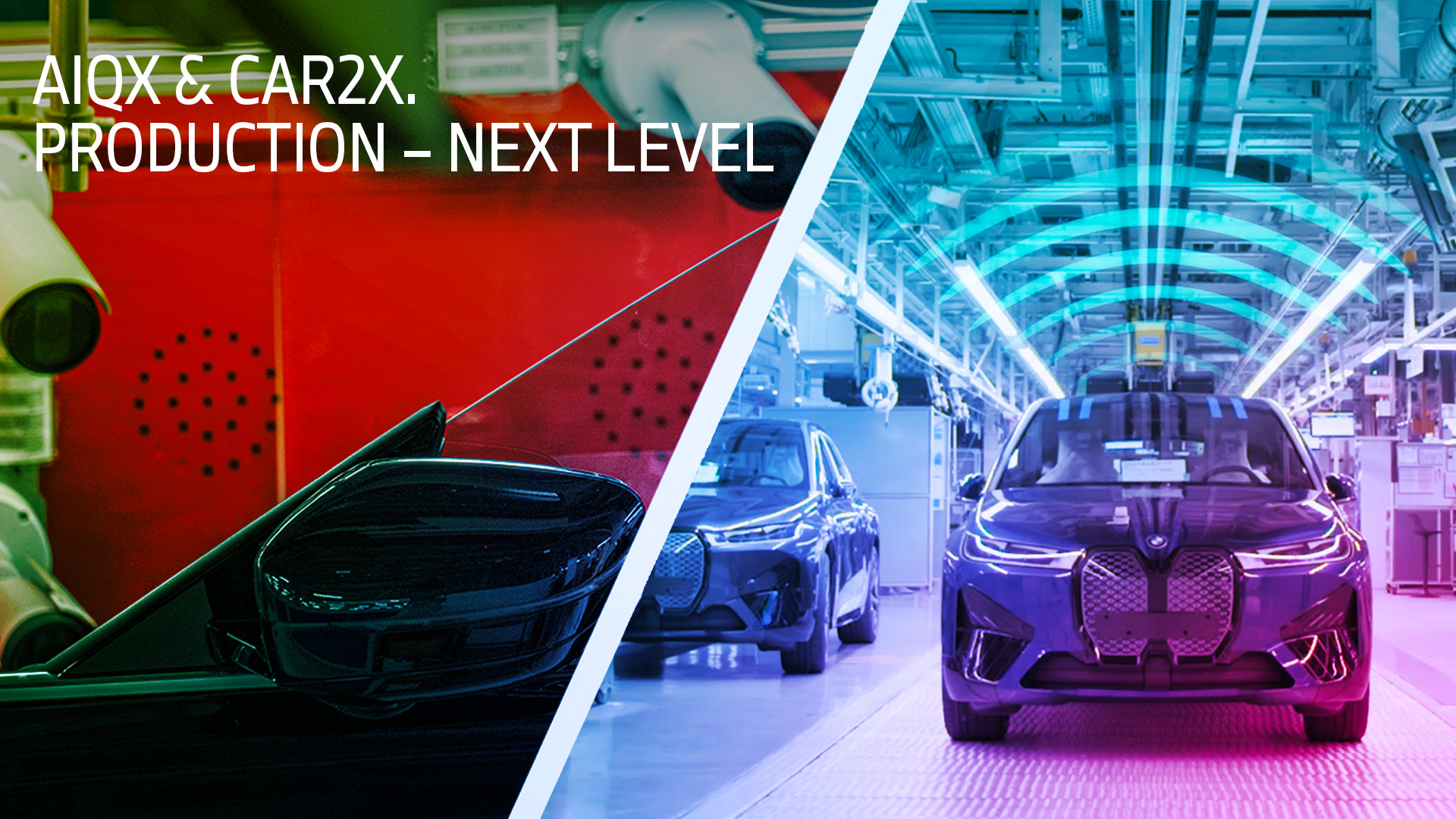