CO2 reduction and resource efficiency drive the vision forwards.
A truck, powered by green hydrogen, carrying components secured with ultralight packaging made from renewable raw materials, driving along optimal transport routes – with CO2 emissions close to zero: This is the vision of the future of logistics at the BMW Group – sustainable through innovation.
The BMW Group has set itself a very clear milestone: to reduce CO2 emissions throughout a vehicle’s entire value chain, from resources to recycling, by 40 percent from 2019 levels by 2030. This ambitious goal requires closely examining a vehicle's entire lifecycle and identifying potential for lowering emissions. Logistics plays an important role in a vehicle's value chain. It seamlessly and precisely connects all players involved in the supply and production process via a variety of transport routes. CO2 emissions are produced throughout this process: on plant grounds (intralogistics), as a result of supplying plants with parts and from shipping the finished vehicles for worldwide distribution (upstream and downstream transport logistics). Karl-Friedrich Koch is responsible for all logistics planning at the BMW Group: “Logistics is definitely a relevant lever for reducing the BMW Group’s environmental footprint, also when considering the entire vehicle lifecycle.”
Technological innovations are needed for low-emission drive trains and resource-efficient packaging for global logistics. In recent years, the BMW Group has launched a variety of activities in these areas. Research and pilot projects, collaborations with service providers in its partner network and the principle of open technology are all part of these efforts. The BMW iFACTORY. LEAN. GREEN. DIGITAL. provides an overarching strategic vision for the global production network – and therefore also for logistics. Flexibility, efficiency, sustainability and digitalisation are key to all processes.
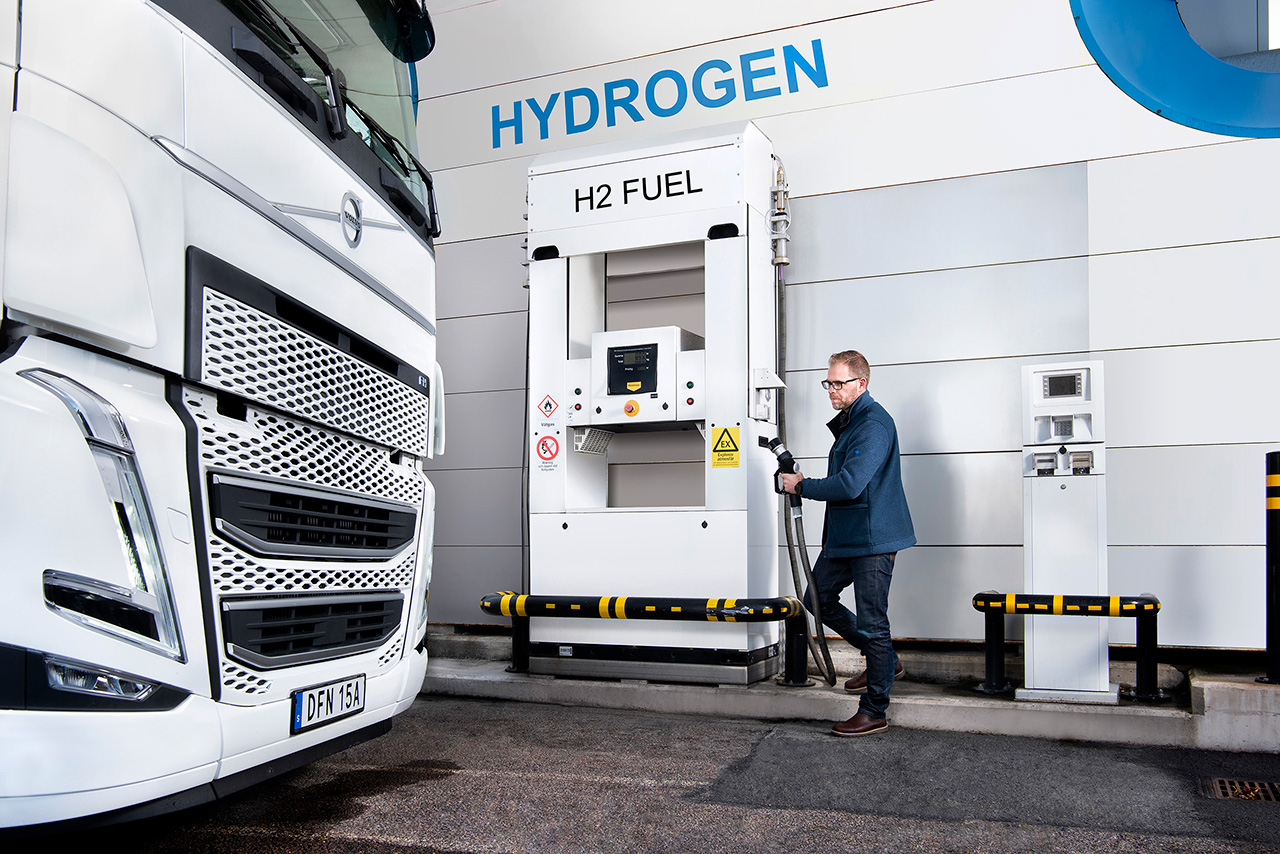
Efficient and innovative transport logistics
“Keeping distances between the supplier and the production plant as short as possible, as well as regional availability of alternative drive technologies and fuels are important decision criteria for designing sustainable logistics concepts – always taking the basic requirements for logistics into account: being able to deliver the right quantity of the right products in the right condition at the right cost at the right time to the right place,” according to Karl Volker Blume, head of Material Control, Transport, Delivery Assurance.
Location plays a major role. In addition to local sourcing of materials, the “production follows the market” principle also applies. Ideally, the production site should be located close to where customers for the finished vehicles are found. Wherever possible, longer transport journeys to supply plants and the markets should be carried out by rail, with overseas transport by sea. Trucks will remain a relevant aspect of overland transport in the future. For short distances within plant grounds or between plants located close to one another, a (still small) percentage of the trucks used today are already powered by sustainable drive trains, including pure electric motors. This is already being realised to a limited extent at Plants Munich, Landshut, Dingolfing, Spartanburg in the US and Shenyang in China. Second-generation biofuel is also being piloted for both road transportation and sea freight. The fuel is made from residual and waste materials and therefore not in competition with the food industry,
Eugen Schantini, head of global vehicle distribution, underlines: “For transporting finished vehicles, we choose the most efficient method of transport with the best-possible use of capacity and technologies that reduce CO2 emissions – across all modes of transport. In this way, we are shaping the transformation of the logistics sector together with our transport service providers.”
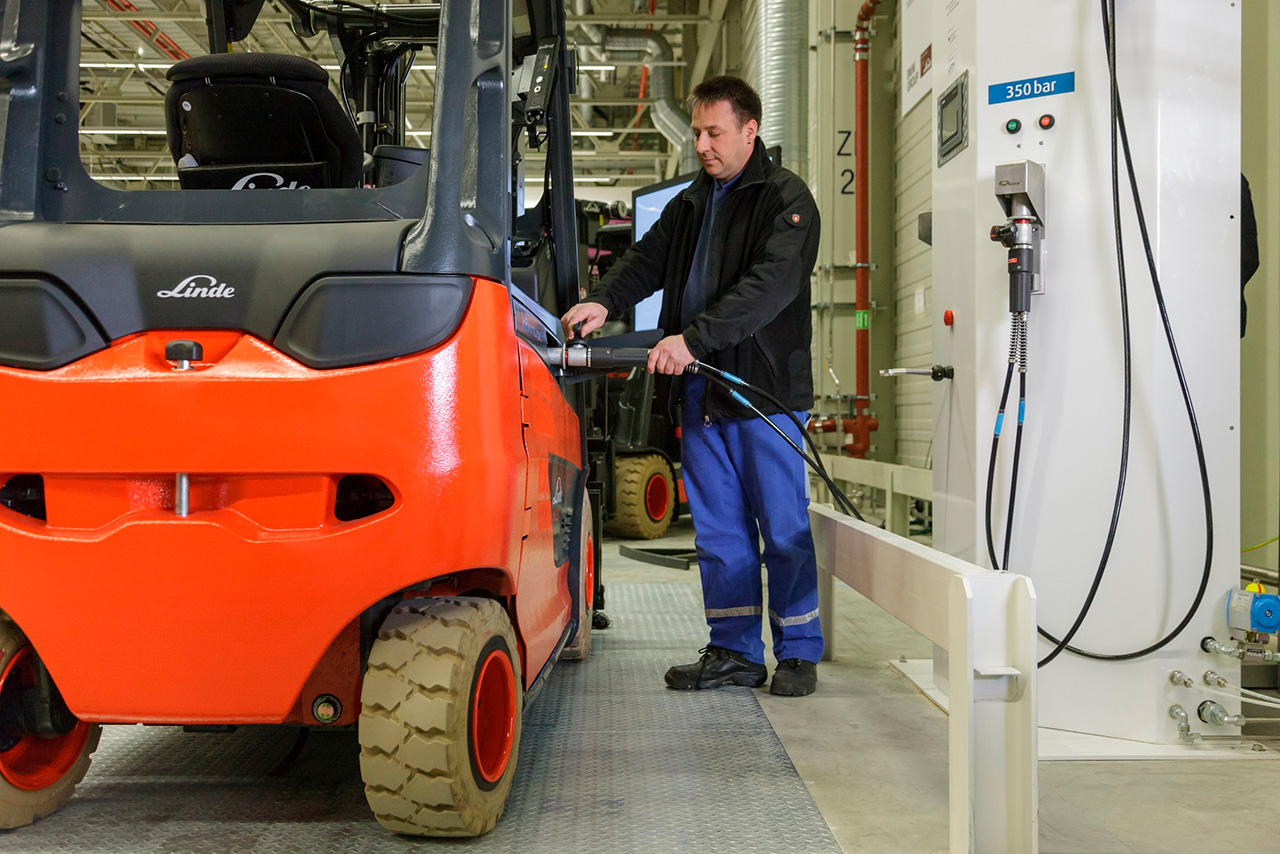
Green hydrogen as the fuel of the future
Since the transport of goods will remain unavoidable in the future, using innovative, sustainable drive technologies for long distances is a central task. To this end, the BMW Group adopts a technology-open approach. The BMW Group believes hydrogen has great potential as a fuel and is engaged in intensive research in this area. Hydrogen is a promising energy source, due, among other factors, to its short filling time, versatility and attractive range. Green hydrogen, produced from renewable energies, should be prioritised. Plant Leipzig is a trailblazer in this respect, pursuing two research projects. Sustainability is deeply rooted in the plant structure and taken into account during the planning stage.
The aim of the “H2Haul” European research project is to develop and pilot electric fuel cell trucks. The scope of the German project includes two fuel cell trucks, which the BMW Group intends to use to transport goods between Plant Leipzig and Nuremberg. As the consortium leader of the second research project, “HyCET”, the BMW Group is directing development and testing of trucks with hydrogen combustion engines, with the aim of demonstrating their potential for transport logistics. The other issue for HyCET, alongside technology development, is the required infrastructure, such as publicly accessible hydrogen filling stations.
Hydrogen: already standard for intralogistics at Plant Leipzig
Hydrogen has played a major role in plant logistics for quite some time, especially at Plant Leipzig. With over 130 industrial trucks powered by fuel cells, the plant operates the largest fleet in Germany. Germany’s first indoor hydrogen filling station was set up on the grounds of Plant Leipzig, back in 2013, for refuelling forklift trucks and tugger trains used in intralogistics. There are five hydrogen filling stations on the plant grounds, the newest of which was just put into service and enables fully automated filling processes for the first time.
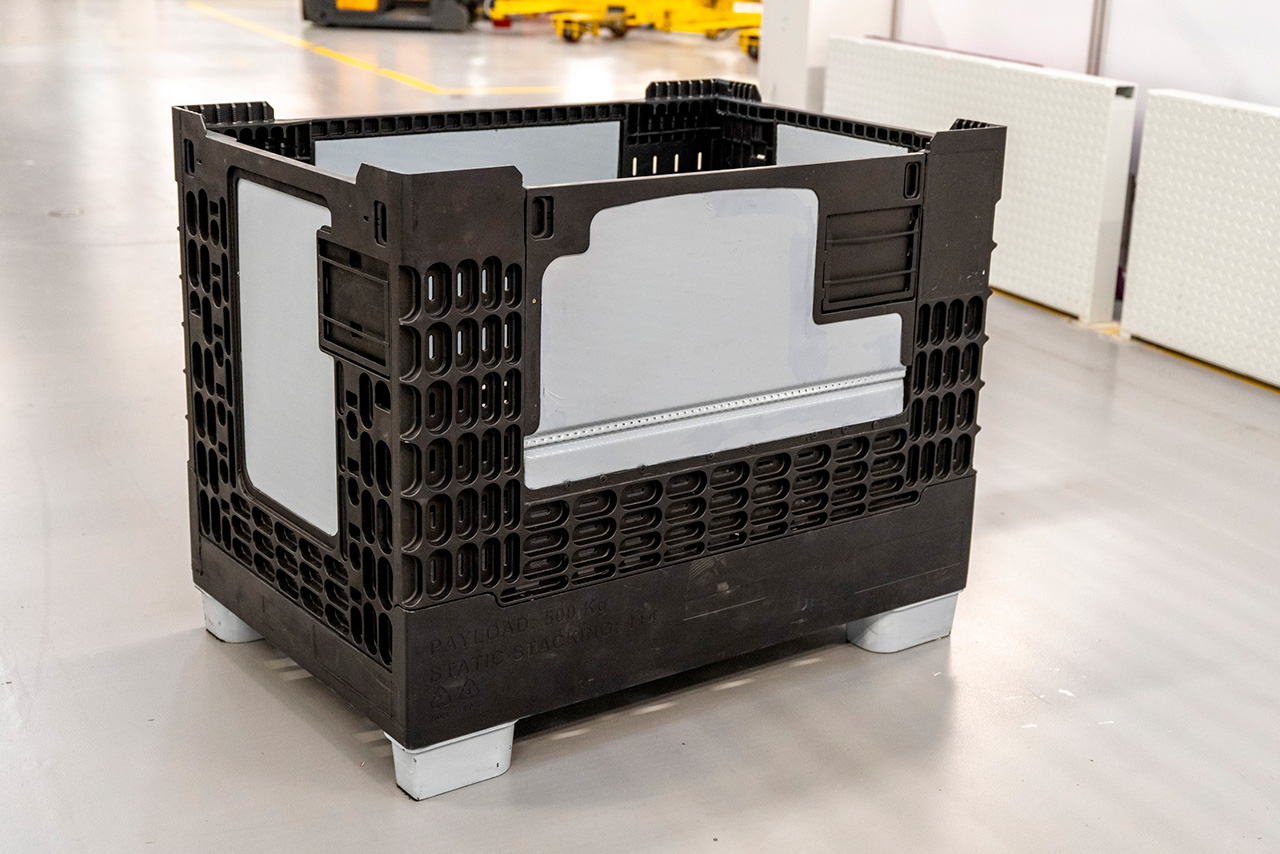
Sustainable, lightweight packaging logistics
Efficient transport logistics also includes sophisticated packaging logistics. Weight, volume and material play a key role in saving resources. Efficient recycling, reducing the amount of disposable packaging, using innovative packaging materials and space-saving lightweight packaging are all factors that can bring these numbers down. The BMW Group is working closely here with its supplier network and can track the impact of individual initiatives using a CO2 calculator. One of the criteria for selecting container suppliers, in consultation with materials purchasing, is availability of alternative fuels.
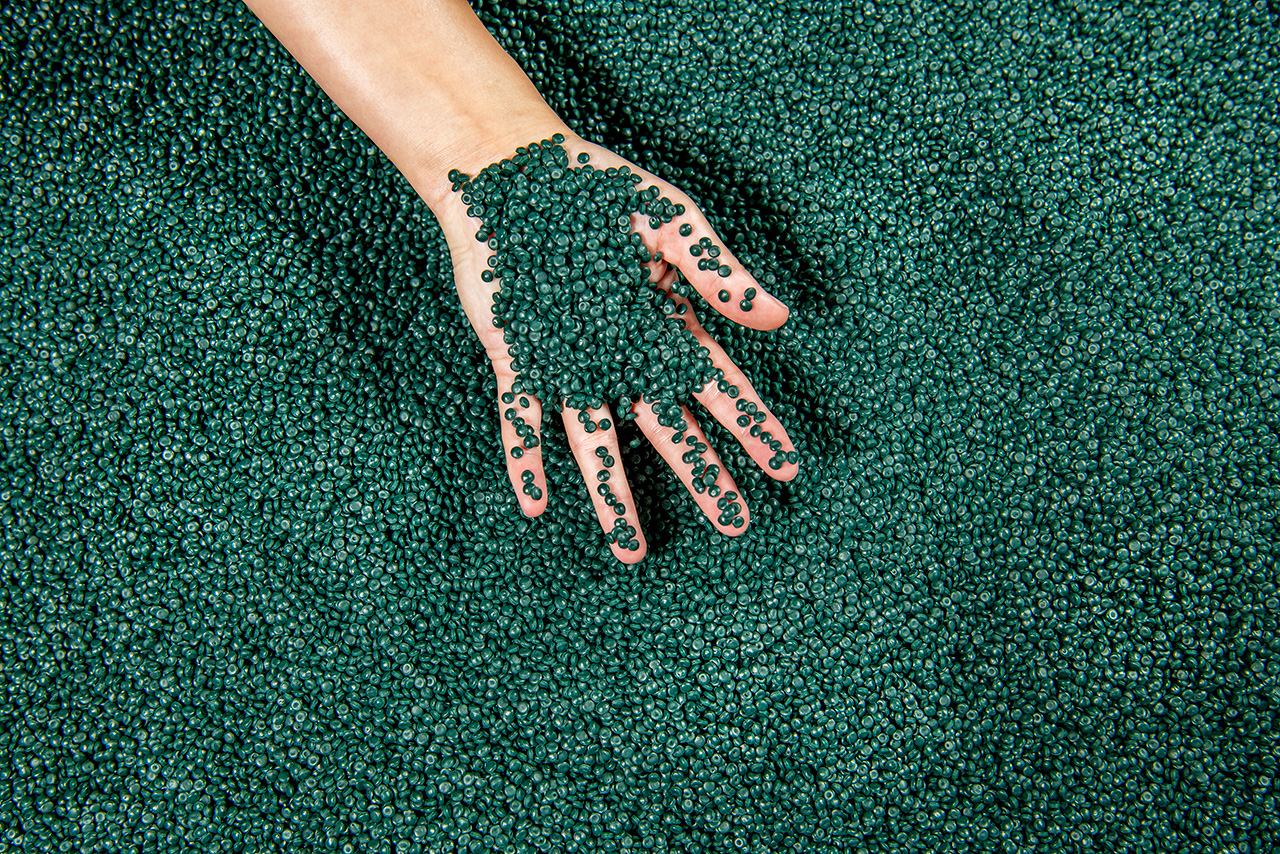
What recycled material can do
With increased recycling to reduce the use of resources, packaging logistics can contribute to implementation of the strategic vision of the BMW iFACTORY and help realise the principles of the circular economy in the best possible way, initially at European plants. It is already having an effect: In 2022, the recycling rate, which measures the use of recycled plastics, was increased from around 20 percent to over 35 percent in new logistics contracts for reusable packaging. The use of recycled material for so-called EPP packaging is particularly promising. EPP, which stands for Expanded Polypropylene, is suitable for use as a malleable and adaptable packaging material, especially for components with delicate surfaces. The percentage of recycled material in newly-developed EPP packaging is already at 25 percent and avoids almost 280 tonnes of CO2 per year. The aim is to continue to expand the amount of secondary material used in packaging. Initial pilot runs with packaging made of 100 percent recycled material are already underway. The use of new large-load carriers has proved even more effective. Collapsible plastic containers made from over 90 percent recycled material will be used instead of steel lattice boxes from 2023 onwards. 15,000 of these innovative containers, when empty and collapsed, not only save space, but also reduce CO2 by about 3,000 tonnes per year. Since this year, the BMW Group has also eliminated the protective film previously used when transporting vehicles. This significant reduction in plastic waste from in-house production and at retail partners will avoid about another 1,400 tonnes of CO2 emissions per year.
Packaging logistics opens up a whole range of future applications. There is still a lot of research to be done into the use of bio-based materials – but the possibilities are endless. The long-term goal of packaging logistics is to switch completely to alternative, resource-efficient raw materials (e.g. renewable materials).
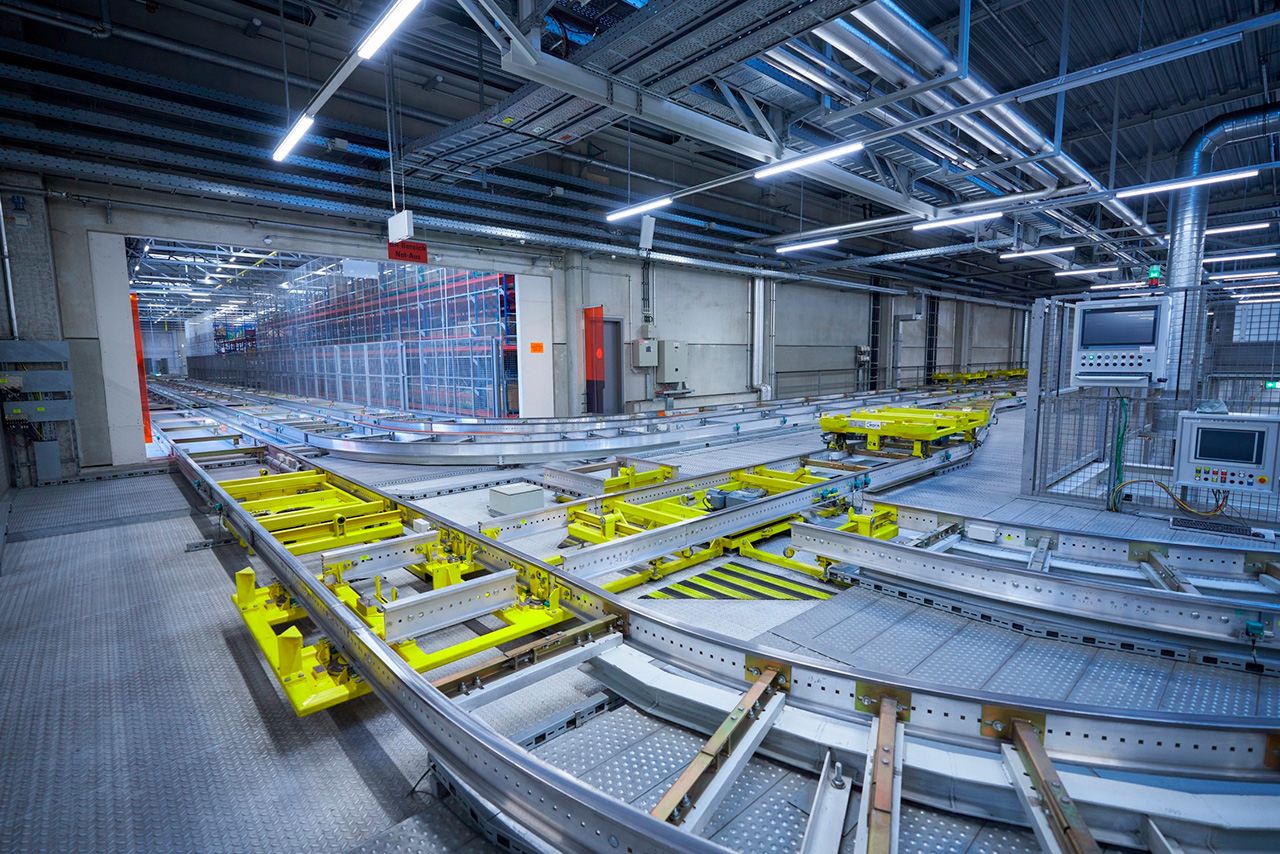
Logistics: circular economy makes transformation essential
Karl-Friedrich Koch summarises: “With its focus on transport, packaging and intralogistics, logistics has huge potential to make a valuable contribution to the BMW Group’s sustainability goals. Carbon-neutral and low-emission drive trains, resource-efficient packaging materials, sustainable and resilient global supply chains (“local for local”) and well-organised transportation are the key levers.”
The principle of sustainability that is enshrined in all areas of the BMW Group has also set a fundamental transformation in motion within logistics. Going forward, the growing importance of the circular economy will be a driving force for this change process. End-of-life vehicles will be used much more as a source of high-quality secondary raw materials that can be fed back into the raw materials cycle in sophisticated ways. These are challenges that not only demand new infrastructures, but also the courage to innovate – and, in many areas, become pioneers.