ANOTHER
STEP TOWARDS THE BMW iFACTORY:
THE DIGITAL PAINT SHOP AT BMW GROUP PLANT
REGENSBURG.
BMW Group Plant Regensburg is the first car plant in the world to use an end-to-end digitalised and automated process to inspect, process and mark painted vehicle surfaces in series production. AI-controlled robots apply objective quality standards to process each vehicle individually. A world first.
STEP 1: AUTOMATED SURFACE INSPECTION.
For decades now, the BMW Group has considered itself the benchmark in production technologies and operative excellence in vehicle manufacturing. And Plant Regensburg – one of over 30 BMW Group production sites worldwide – is no exception. It’s been in operation since 1986, and about 1,300 BMW X2 vehicles roll off its production lines every working day.
Automated Surface Processing has been in use in series production since March 2022, using an AI-based process to treat freshly painted vehicle surfaces. First of all, Automated Surface Inspection identifies and logs any imperfections in the topcoat. This is done by means of a technology called deflectometry, in which large-scale monitors project geometric patterns onto the surface of the vehicle. These patterns are then scanned by cameras to identify even the smallest imperfection in the surface of the paint. Based on the camera data, the computer system creates a digital 3D image of the vehicle and classifies it according to objective inspection criteria.
STEP 2: Automated Surface Processing.
Step 2 is where Automated Surface Processing comes in. Each surface is worked through individually based on the 3D image of the body. The robots sand the surfaces and apply polishing compound, switch their own attachments and, if needed, correct even the tiniest irregularities in the surface of the paint. Tailored to each individual car, the process is stable and reproducible, delivering the same high standard of quality throughout.
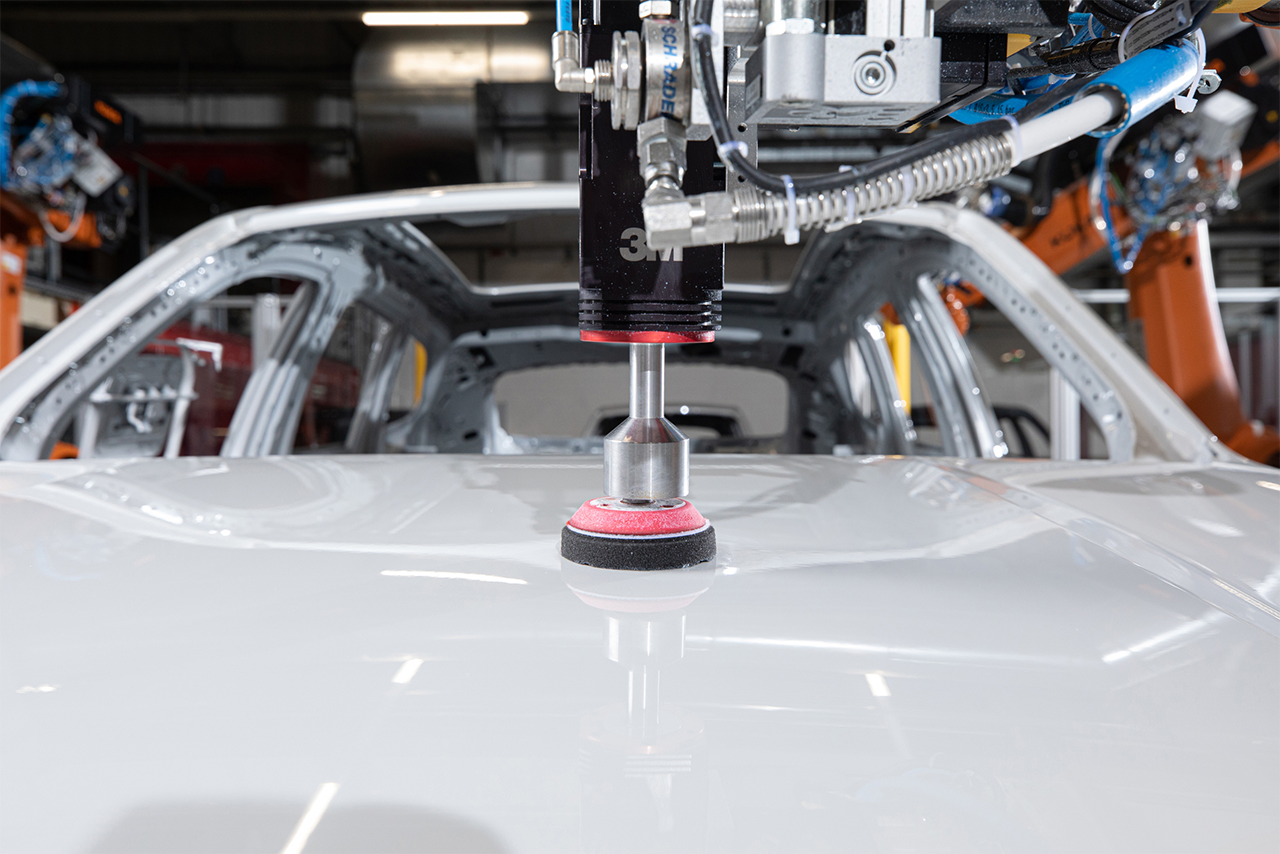
STEP 3: AUTOMATIED SURFACE MARKING.
The final stage of the three-step digital and automated process is Automated Surface Marking. Here, a laser projector marks out potential flaws in the surface of the paint to ensure employees don’t miss anything when they conduct the final inspection. The human eye can become fatigued after a while – but Automated Surface Marking is there for support.
In the future, the plan is to avoid imperfections altogether. This will be done with the help of data stored in the cloud, including automatic tracking of every stage of an employee’s work – which will in turn save time as they no longer have to switch between the computer and the car body.
And all this is just the beginning: we are currently assessing a potential rollout of the three-stage process in other plants as well, taking us one step closer to the digital and smart factory – the BMW iFACTORY.