BMW 3D printing takes over in production: individual robot grippers play a crucial role.
3D printing – or additive manufacturing, as it’s also known – has been in use at the BMW Group for the last 30 years. Initially it was only used to produce individual parts, but it is now being used to create tools and work aids as well. This has a range of advantages for different areas of production – including the use of robot arms.
3D printing – a modern tradition.
The BMW Group has been using 3D printers since 1991, to design components for special models, concept cars, prototypes and race cars as well as for production models. But the technology is also used to produce work aids for car construction and manufacturing at BMW plants. These days more than 400,000 parts a year worldwide are produced by 3D printing, which is primarily a cost-efficient and flexible way of quickly producing the individual parts required. But it’s now even more than that and has even been used to create entire devices.
The BMW Group understands the advantages and benefits of the technology and has focused on them extensively. The Additive Manufacturing Campus in Oberschleissheim, just north of Munich, is the company’s dedicated base for research and production. In 2023 alone, it 3D-printed over 300,000 parts, with further components manufactured across the BMW Group’s global production network.
“The increasing use of additive manufacturing in the BMW Group production system has many benefits. For example, we are able to quickly, economically and flexibly produce our own production aids and handling robots, which we can adapt to specific requirements at any time as well as being able to optimise their weight. Less weight allows higher speeds on the production line, shorter cycle times and reduced costs. Plus, smaller robots can be used in the medium term, which also cuts CO2 emissions and costs,” says Jens Ertel, Head of the Additive Manufacturing Campus.
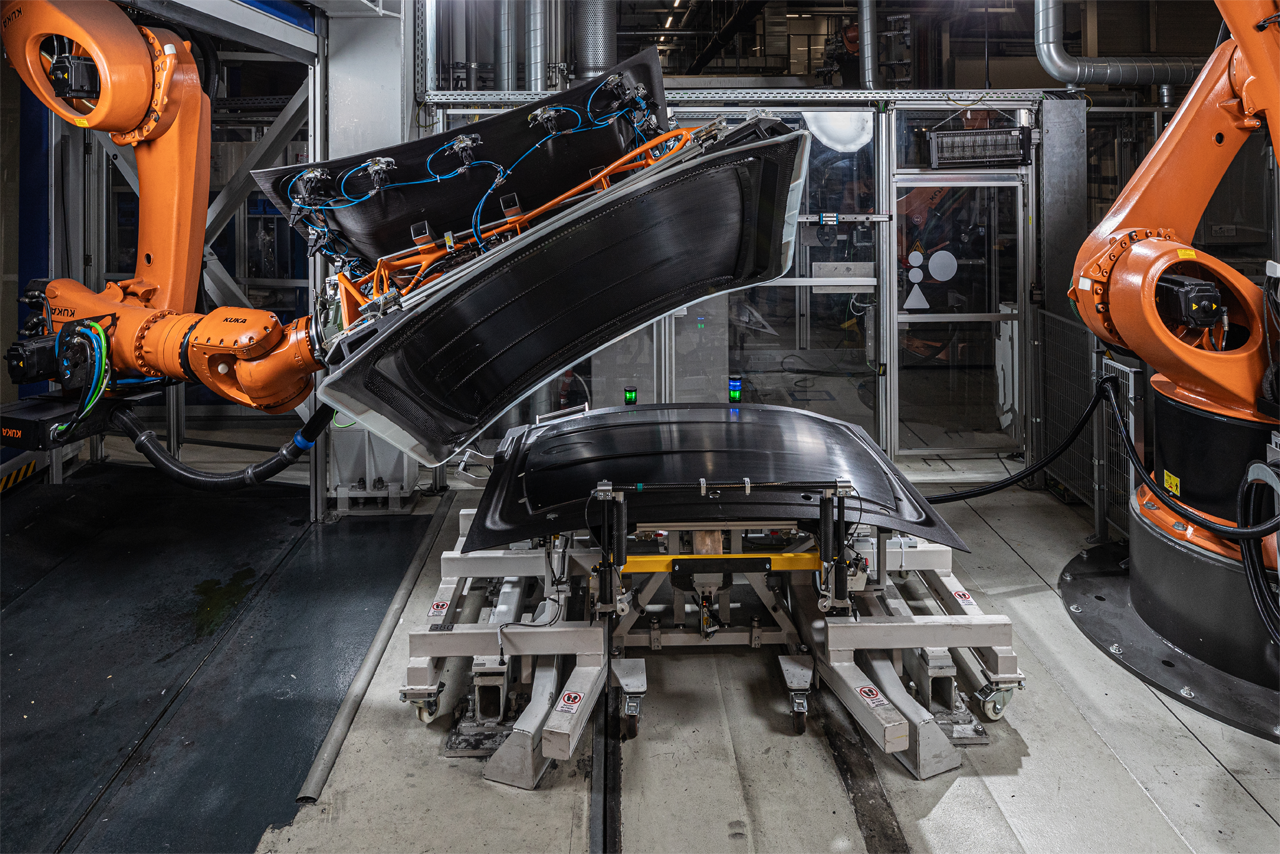
A grip on advances – robot grippers at BMW plants.
3D printing also offers extensive benefits in production. The Lightweight Construction and Technology Centre in Landshut uses a gripper element that took 22 hours to print and weighs just 150 kilogrammes. Fitted to a press, it is used to produce CFRP roofs for BMW M models. Because of the way it was made, it is about 20 percent lighter, which in turn makes the robot gripper more durable and resilient and extends maintenance intervals. Within the 3D printing process, LSP (large-scale printing) enables large components to be manufactured more sustainably, as the combination of injection moulding granules and recycled plastics, or residual materials from CFRP, cuts CO2 emissions from robot gripper production by more than 60 percent.
Since 2023 the BMW Group has been using new, even lighter grippers. These bionic, topologically optimised robot parts are another 25 percent lighter, so just one robot with double grippers is needed in CFRP roof production rather than the previous three. These double grippers are all individually made in-house at BMW Group Plant Landshut – by 3D printing.
The BMW Group also uses 3D-printed work aids in the bodyshops of other German plants. In Munich, for instance, bionic robot grippers can hold and move the entire floor assembly of a BMW i4. This new gripper generation has been even further optimised in terms of weight and maximum load, and each one now weighs in at about 100 kilogrammes, add-ons included. This makes it 30 percent lighter than its predecessor. The delicate structure is made possible by a mix of sand-casting and aluminium and can be used for heavy-load robots, saving energy and therefore CO2.
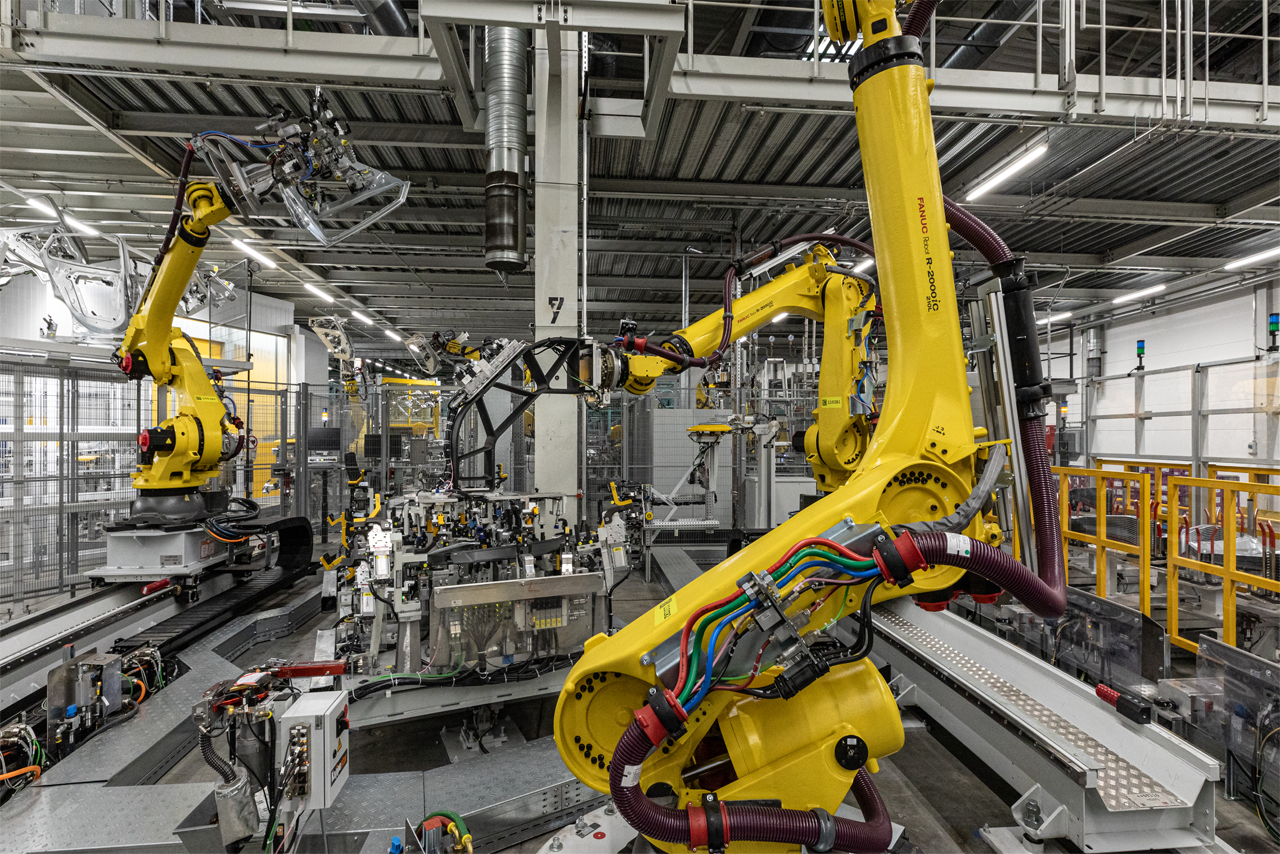
Optimised from hardware to software.
For optimum 3D printing, structures must be designed and calculated in minute detail. This is done with the help of specialist software tools such as Synera, formerly Elise. Synera software has been strategically and intricately developed by BMW iVentures and is now used in numerous areas of the BMW Group. By efficiently optimising existing processes and calculations, Synera allows bionic structures to be 3D printed almost one-to-one to the intended design, thanks to a high degree of flexibility.
Synera is undergoing further enhancement as well, primarily at the Additive Manufacturing Campus in Oberschleissheim. Here, a team of design and construction specialists compares various software solutions to uncover further potential for optimisation. Solutions have also been developed for the BMW 3D printers that make the robot grippers, to automate the engineering of the material structure and make printing even faster and therefore more efficient.
For more on production and its development at BMW Group plants, click here.