In economically and politically volatile times like these, the strategic setup and flexible responsiveness of the BMW Group’s production network are becoming more and more important. A key role in this regard falls to the global balance of value creation across the key regions of the world: production volumes in Europe, America and China roughly reflect the sales in those regions. “The strategic setup and flexibility of our production network makes us more resilient and competitive,” explains Milan Nedeljković, Member of the Board of Management responsible for Production. And that, in turn, makes the network more robust in terms of trade and geopolitics.
GLOBALLY BALANCED PLANT UTILISATION.
When it comes to decisions around plant utilisation, i.e. which models are produced where, one criterion is market proximity. Plant Spartanburg in the US, for example, is the centre of excellence for BMW X models because the US is the main market for BMW Group Sports Activity Vehicles. In 2024 production and sales volumes amounted to just under 400,000 units, with almost 50 percent of all BMWs sold in the US made at Plant Spartanburg.
The Chinese market accounts for over a quarter of the BMW Group’s total sales and is so large that the joint venture BMW Brilliance Automotive (BBA) produces vehicles almost exclusively for that market. Again, sales and production volumes are equal, with almost 90 percent of vehicles made in China sold in China too.
The German plants in Munich, Regensburg and Leipzig make vehicles in the lower and compact class, which are mainly sold in Europe. Last year, we were able to grow in our home market and produced over one million cars there, despite the volatile environment.
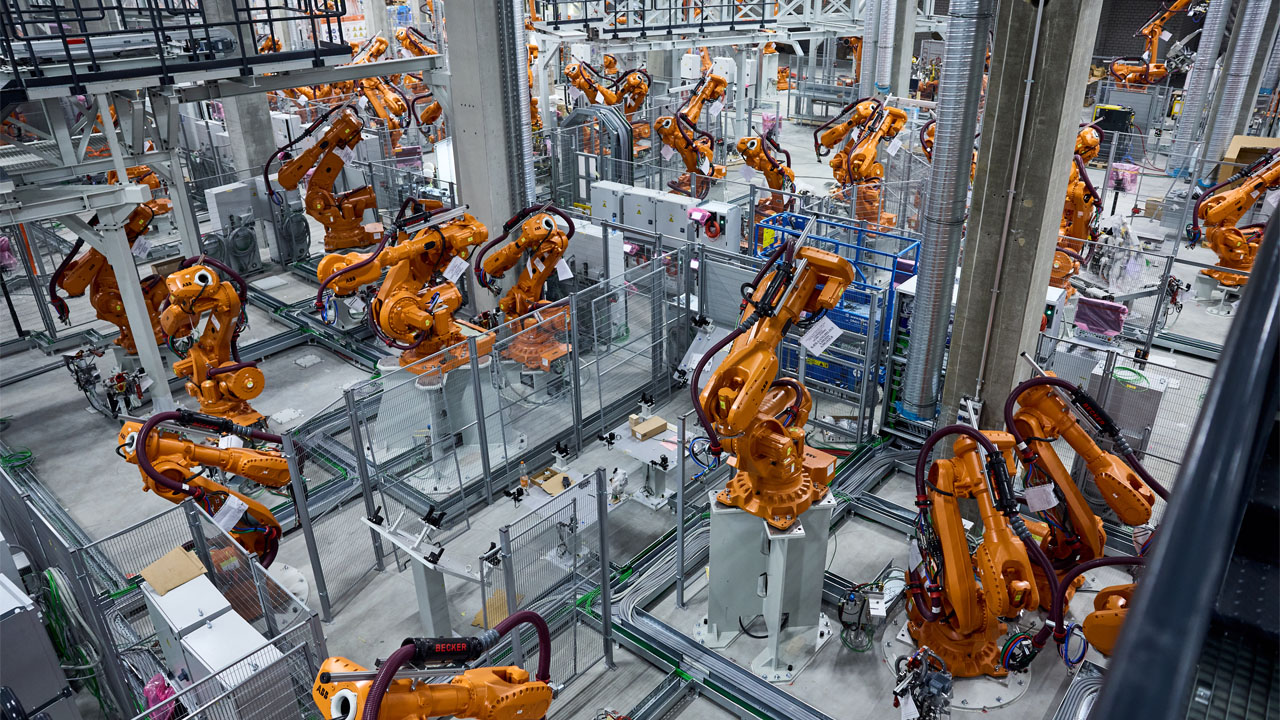
E-MOBILITY AT A GLANCE.
Rather than happening in a linear fashion, electromobility is ramping up at different speeds around the world. That’s why the BMW Group has so far relied on flex plants that can produce combustion as well as electrically powered vehicles. In Germany, Plants Munich, Dingolfing, Regensburg and Leipzig each produce at least one fully electric model for the global market in addition to conventional drives.
But electromobility is not just advancing at our German plants: our Chinese plants have fully electric vehicles in their production portfolios too. In addition, the electrification of Plant Spartanburg is about to start, with all-electric vehicles joining the existing production portfolio at the end of 2026. Plant San Luis Potosí in Mexico is also preparing for all-electric Neue Klasse vehicles, with production set to launch in 2027.
As the product portfolio becomes ever more electrified, the plant landscape is changing too. By the end of this decade, the BMW Group expects a roughly 50/50 sales split between fully electric and combustion-powered vehicles. That’s why Plant Debrecen in Hungary – and, in future, the BMW Group’s home plant in Munich too – will be the first facilities to deliver all-electric vehicles only. As electrification is rolled out across the production network, the new plant in Debrecen will launch production of the all-electric Neue Klasse this year. Plant Munich will switch purely to fully electric vehicles when work on its conversion is completed, in 2027.
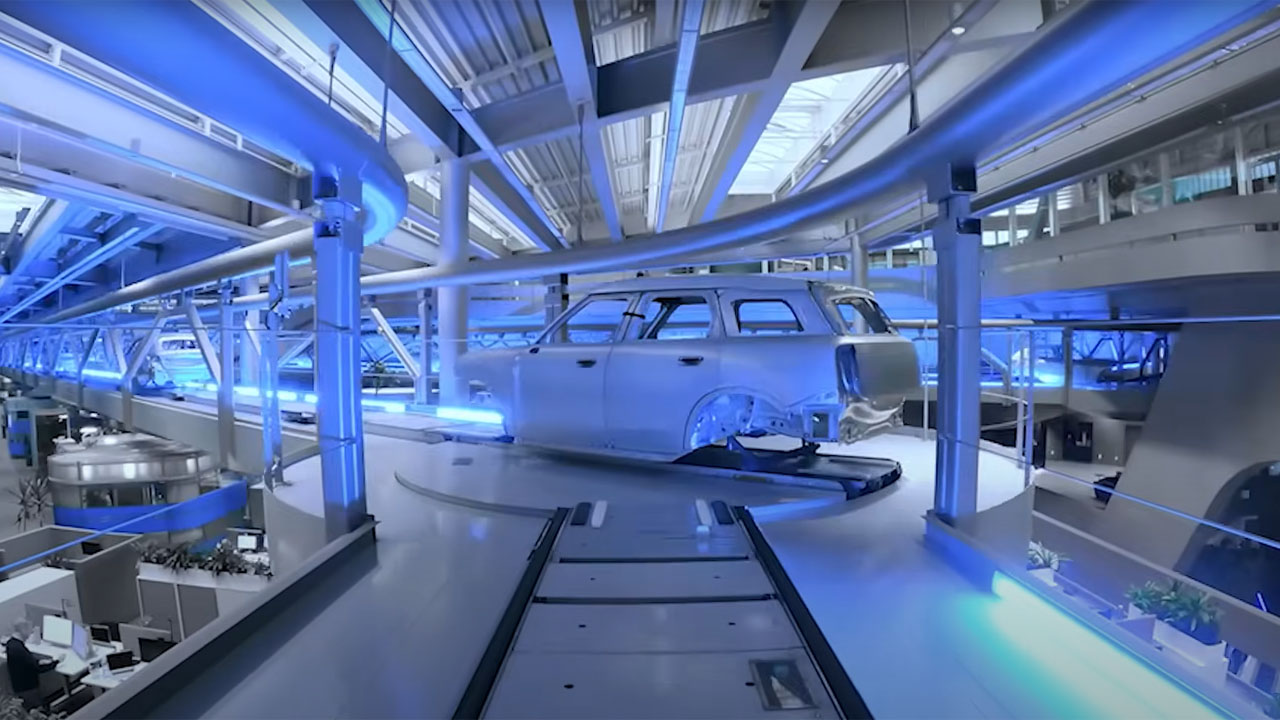
COUNTDOWN AT PLANT MUNICH.
Plant Munich will launch production of the Neue Klasse in the summer of 2026. Three new halls are currently being built to accommodate the bodyshop, assembly and the associated production logistics – while series manufacturing is ongoing. “For the production start of the Neue Klasse, we will have a state-of-the-art plant in Munich that is characterised by flexibility, innovation and, above all, efficiency,” says Plant Director Peter Weber.
The first pre-series Neue Klasse vehicles will be built in 2025 – but with the new assembly line still under construction, they will be made in the pilot plant at the Research and Innovation Centre FIZ. The experienced launch team at Plant Munich will use virtual simulations and cooperate with colleagues at the new plant in Debrecen to ensure a smooth production launch.
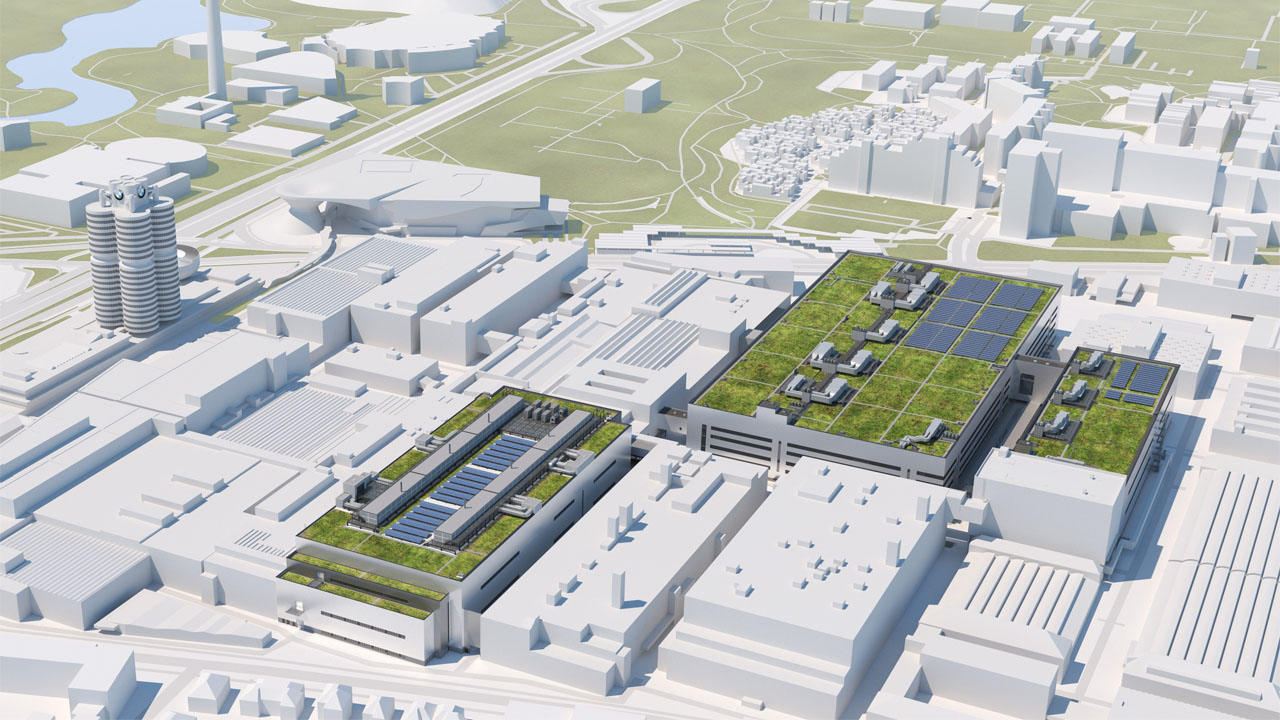